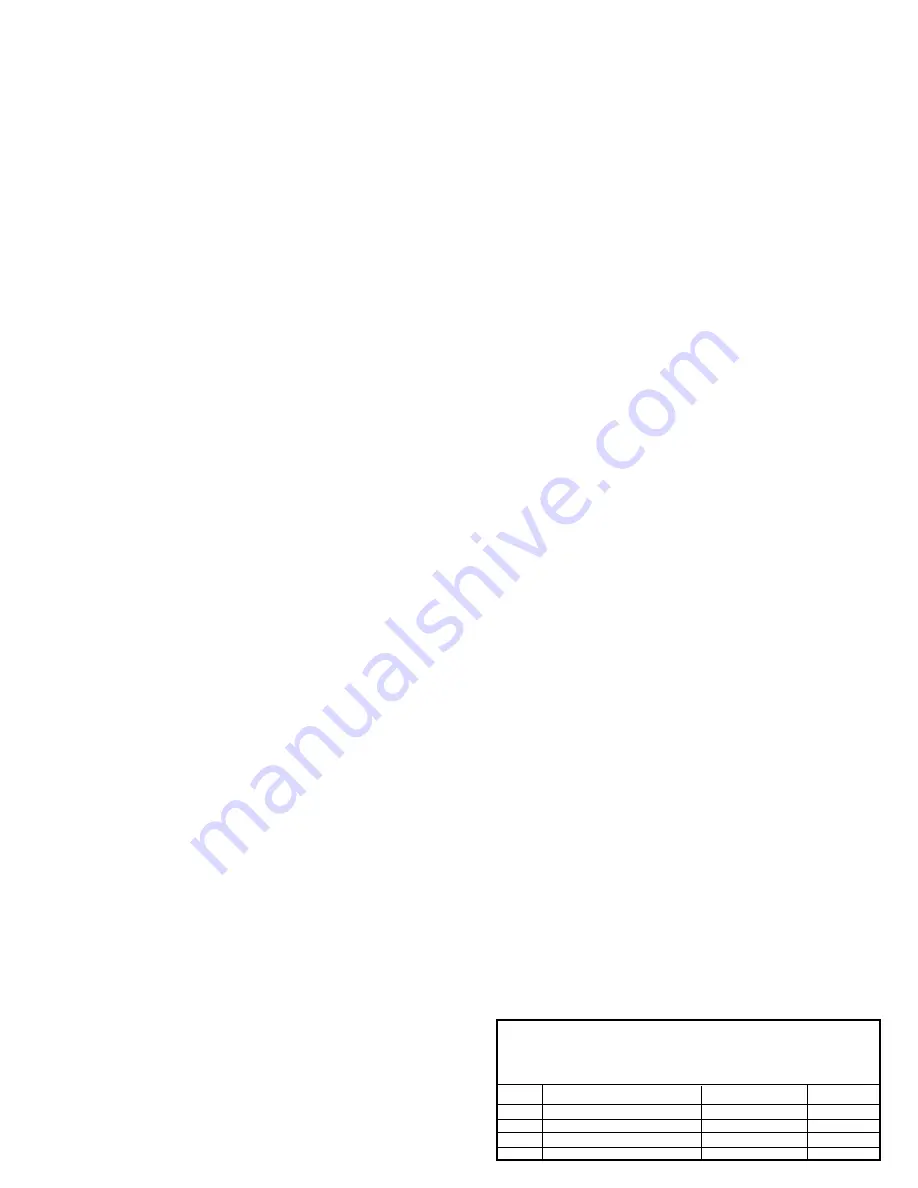
HARNESS CERTIFICATION AND USE
Rescue and work harnesses from CMC Rescue are
designed to comfortably support the wearer, creating a safe
work platform. Because our harnesses are used when working
at heights, they are also built with the strength to catch a fall.
NFPA 1983 provides specifications for rescue harnesses. All
front and back D-ring connection points are dynamically and
statically tested to this standard. The side D-rings are tested
as pairs in the manner of use.
USER INFORMATION
User Information shall be provided to the user of the
product. NFPA Standard 1983 recommends separating the
User Information from the equipment and retaining the
information in a permanent record. The standard also
recommends making a copy of the User Information to keep
with the equipment and that the information should be referred
to before and after each use.
Additional information regarding auxiliary equipment can be
found in NFPA 1500,
Standard on Fire Department
Occupational Safety and Health Programs
, and NFPA 1983,
Standard on Life Safety Rope and Equipment for Emergency
Services.
INSPECTION
Inspect the equipment according to your department's policy
for inspecting life safety equipment. Inspect the equipment
prior to entry into service, after each use, and at least once
every 12 months. The equipment should be thoroughly
inspected by an inspector that meets your department's
training standard for inspection of life safety equipment. Keep
a record of the date, person performing the inspection and
results, as well as the date of first use, name of users and any
other pertinent information necessary to keep accurate track of
the equipment’s usage history in the equipment log or on a tag
that attaches to the equipment. Each user should be trained in
equipment inspection and should inspect the equipment before
each use.
When inspecting the equipment, check the webbing and
rope for cuts, worn or frayed areas, broken fibers, soft or hard
spots, discoloration, or melted fibers. Check the stitching for
pulled threads, abrasion, or breaks. Check the hardware for
damage, sharp edges, and improper operation. If any of the
above is noted, or if the equipment has been subjected to
shock loads, fall loads, or abuse other than normal use,
remove the equipment from service and destroy it. If there is
any doubt about the serviceability of the equipment, remove
the equipment from service and destroy it.
The service life of equipment depends greatly on the type of
use and the environment of use. Because these factors vary
greatly, a precise service life of the equipment cannot be
provided.
PUTTING ON YOUR HARNESS
1) Loosen the adjusting buckle on each side of the waist belt
to make the waist larger (one or both waist quick-connect
buckles may be disconnected to facilitate donning the
harness).
2) Holding the harness by the right shoulder strap, unhook the
shoulder and thigh quick-connect buckles. With the
shoulder strap in the right hand, step through the waist
belt.*
3) Pull the waist belt up around your waist while sliding the
shoulder strap over your right shoulder (re-connect the
waist buckles if necessary).
4) Tighten both waist straps until the waist is snug, and the
front D-ring is centered. Fold the ends of the waist straps
under the Web-Keepers™ and secure them tightly.
5) Connect the shoulder strap quick-connect buckle.
6) Adjust the shoulder straps by sliding the webbing through
the adjusting buckle until the straps are snug.
7) Connect the thigh quick-connect buckles and adjust until
snug.
*An optional donning technique is to leave the shoulder strap
connected and disconnect either the left or right waist belt
quick-connect buckle. Step through the space between the
connected side of the waist belt and the leg loop while placing
the shoulder straps over your head.
A suspension test should be carried out in a safe place prior
to putting the harness in service. A suspension test will verify
that the harness is the correct size, has sufficient adjustment
and is of an acceptable comfort level for the intended use.
WARNING: Make sure the straps are snug. This
increases the comfort when sitting in the harness and
helps prevent the quick-connect buckles from
disconnecting. When wearing the harness, double-check
the buckles, adjusters, and fit of the harness immediately
prior to relying on it for support.
ATTACHMENT POINTS
•
The dorsal D-ring is the attachment point accommodates
operations where a dorsal attachment point is warranted
•
The front waist D-ring is the primary rescue/work positioning
attachment point. It allows the user to be in a sitting position
which provides the most comfort and freedom of movement.
•
The front sternum D-ring holds the user in a more upright
position which may provide easier access during a vertical
entry or exit.
•
The side D-rings are for work positioning and must always
be used in pairs.
To prevent roll out when using carabiners to attach to
an attachment point, use only locking models. If using
manual locking carabiners, verify that they are locked
before use. CMC/Roco Harnesses are not intended for
rock climbing. Leadclimbing ropes should not be tied into
the D-ring or connected into it with a carabiner.
CARRYING, MAINTENANCE & STORAGE
During use, carrying and storage keep the equipment away
from acids, alkalis, exhaust emissions, rust and strong
chemicals. Do not expose the equipment to flame or high
temperatures. Carry the equipment where it will be protected
as the equipment could melt or burn and fail if exposed to
flame or high temperatures.
If the equipment becomes soiled, it can be washed in cold
water with a mild detergent that is safe for use with nylon and
polyester. Dry out of direct sunlight. Do not dry in an automatic
dryer. Store in a cool, dry location. Do not store where the
equipment may be exposed to moist air, particularly where
dissimilar metals are stored together.
REPAIR
All repair work shall be performed by the manufacturer. All
other work or modifications void the warranty and releases
CMC from all liability and responsibility as the manufacturer.
SAMPLE INSPECTION AND MAINTENANCE LOG
The sample log suggests records that should be maintained
by the purchaser or user of life safety equipment.
Equipment Inspection and Maintenance Log
Item __________ # __________ Date in Service _____________
Brand/Model ________________ Strength ___________________
Date How Used or Maintained Comments Name