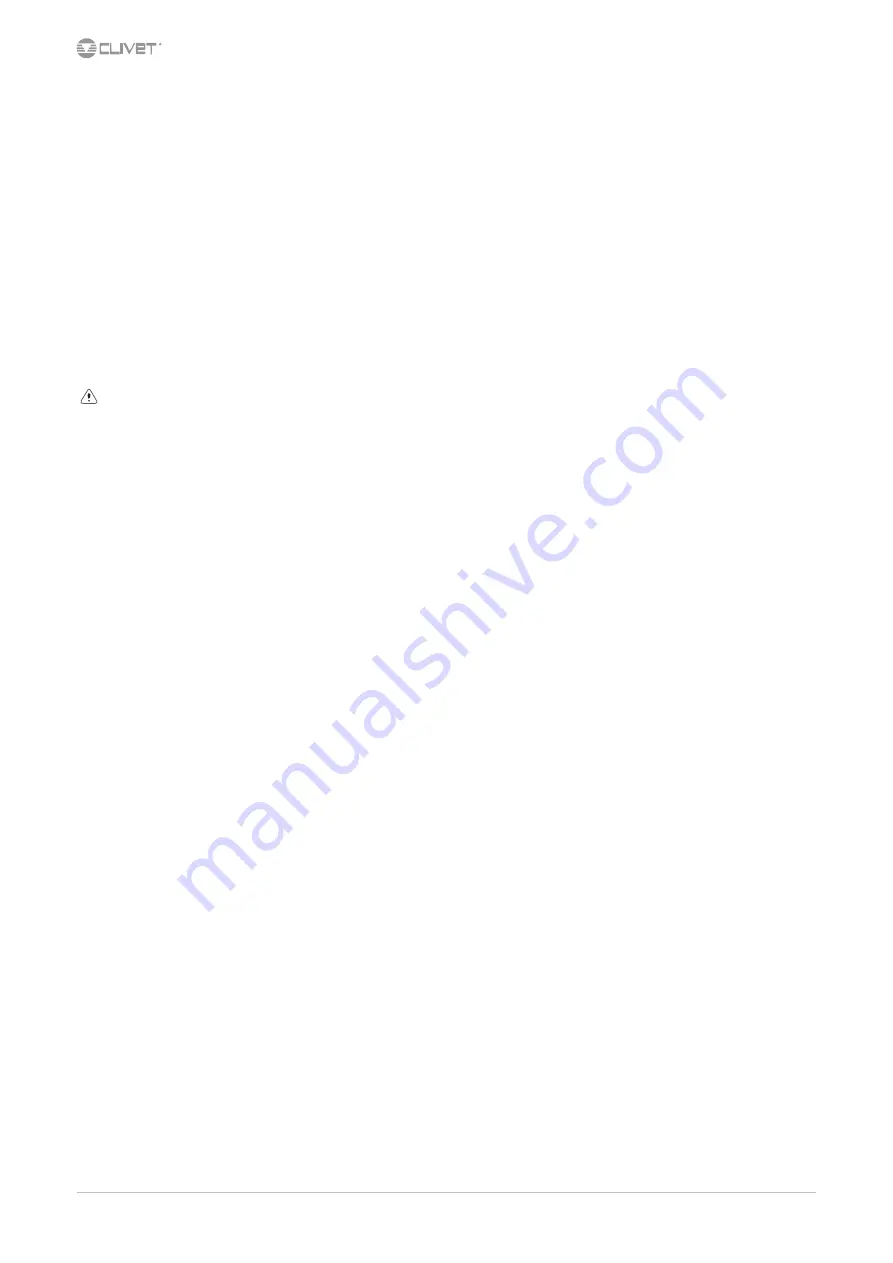
12
WSAN-XSC3 MF 90.4-240.4
M02M40N15-01
4.10 Operation sequence
Close all vent valves in the high points of the unit hydraulic circuit
Close all drain valves in the low points of the unit hydraulic circuit:
•
Heat exchangers
•
Pumps
•
collectors
•
storage tank
•
free-cooling coil
1. Carefully wash the system with clean water: fill and drain the system several times.
2. Apply additives to prevent corrosion, fouling, formation of mud and algae.
3. Fill the plant
4. Execute leakage test.
5. Isolate the pipes to avoid heat dispersions and formation of condensate.
6. Leave various point of service free (wells, vent-holes etc).
Neglecting the washing will lead to several filter cleaning interventions and at worst cases can cause damages to the exchangers and the
other parts.
4.11 hydronic assembly
For details see:
9 Accessories p. 47
Summary of Contents for WSAN-XSC3 MF 200.4
Page 20: ...20 WSAN XSC3 MF 90 4 240 4 M02M40N15 01 6 4 Configuration for 2 pipe system ...
Page 45: ...M02M40N15 01 WSAN XSC3 MF 90 4 240 4 45 8 17 Compressor replacement ...
Page 46: ...46 WSAN XSC3 MF 90 4 240 4 M02M40N15 01 8 18 Exchanger replacement ...
Page 47: ...M02M40N15 01 WSAN XSC3 MF 90 4 240 4 47 9 Accessories 9 1 Anti vibration mount support ...