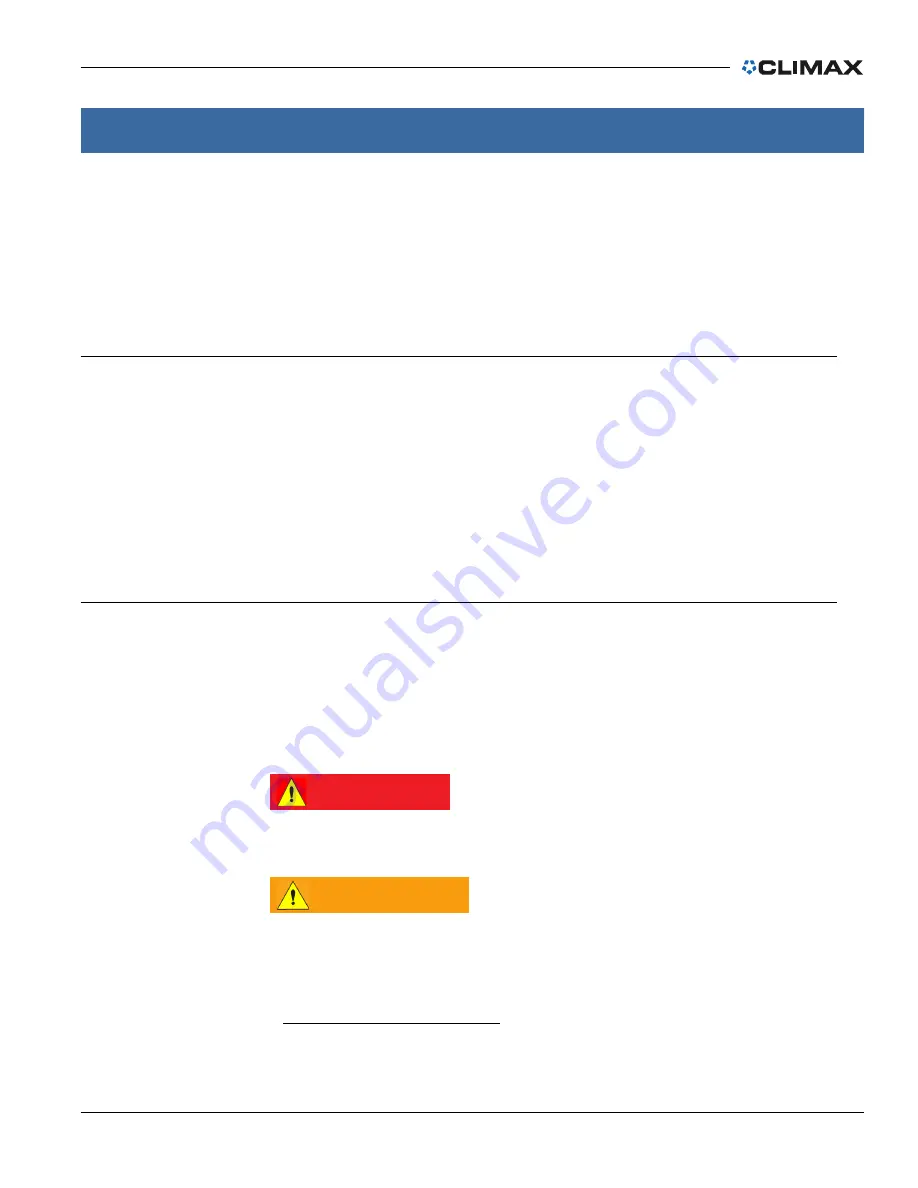
P/N 90075, Rev. 1
Page 1
1
INTRODUCTION
IN THIS CHAPTER:
- - - - - - - - - - - - - - - - - - - - - - - - - - - - - - - - - - - - - - 1
- - - - - - - - - - - - - - - - - - - - - - - - - - - - - - - - - - - - - - - - - - - 1
- - - - - - - - - - - - - - - - - - - - - - - - - - - - - - - - - - - 2
- - - - - - - - - - - - - - - - - - - - - - - - - - - - - - - 3
ISK ASSESSMENT AND HAZARD MITIGATION
- - - - - - - - - - - - - - - - - - - - - - - - - - - - - - 4
- - - - - - - - - - - - - - - - - - - - - - - - - - - - - - - - - - - - 5
1.1
H
OW TO USE THIS MANUAL
This manual describes information necessary for the setup, operation, mainte-
nance, storage, shipping, and decommissioning of the VM1700S-1900S.
The first page of each chapter includes a summary of the chapter contents to help
you locate specific information. The appendices contain supplemental product
information to aid in setup, operation, and maintenance tasks.
Read this entire manual to familiarize yourself with the VM1700S-1900S before
attempting to set it up or operate it.
1.2
S
AFETY ALERTS
Pay careful attention to the safety alerts printed throughout this manual. Safety
alerts will call your attention to specific hazardous situations that may be encoun-
tered when operating this machine.
Examples of safety alerts used in this manual are defined here
1
:
DANGER
indicates a hazardous situation which, if not avoided,
WILL
result in death or severe injury.
WARNING
indicates a hazardous situation which, if not avoided,
COULD
result in death or severe injury.
1. For more information on safety alerts, refer to
ANSI/NEMA Z535.6-2011, Product
safety Information in Product Manuals, Instructions, and Other Collateral Materials
.
Summary of Contents for VM1700S
Page 2: ......
Page 4: ...Page B VM1700S 1900S Operating Manual CLIMAX GLOBAL LOCATIONS...
Page 5: ...P N 90075 Rev 1 Page C CE DOCUMENTATION...
Page 12: ...Page 2 VM1700S 1900S Operating Manual This page intentionally left blank...
Page 18: ...Page 6 VM1700S 1900S Operating Manual This page intentionally left blank...
Page 38: ...Page 26 VM1700S 1900S Operating Manual This page intentionally left blank...
Page 48: ...Page 36 VM1700S 1900S Operating Manual 4 6 CONICAL SEATS OPTIONAL...
Page 54: ...Page 42 VM1700S 1900S Operating Manual This page intentionally left blank...
Page 58: ...Page 46 VM1700S 1900S Operating Manual FIGURE A 1 ASSEMBLY...
Page 59: ...P N 90075 Rev 1 Page 47...
Page 60: ...Page 48 VM1700S 1900S Operating Manual...
Page 61: ...P N 90075 Rev 1 Page 49...
Page 62: ...Page 50 VM1700S 1900S Operating Manual FIGURE A 2 470 10S N01 00 DRIVE MOTOR...
Page 63: ...P N 90075 Rev 1 Page 51 FIGURE A 3 240 11S N01 00 ELECTRIC DRIVE 220V...
Page 64: ...Page 52 VM1700S 1900S Operating Manual FIGURE A 4 240 13S N01 00 PNEUMATIC DRIVE...
Page 65: ...P N 90075 Rev 1 Page 53 FIGURE A 5 240 15S N01 00 ELECTRIC DRIVE 110V...
Page 66: ...Page 54 VM1700S 1900S Operating Manual FIGURE A 6 470 16S N01 00 AIR DRIVE WITH EX CERTIFICATE...
Page 67: ...P N 90075 Rev 1 Page 55 FIGURE A 7 470 20S N01 00 UPPER GEAR BOX...
Page 68: ...Page 56 VM1700S 1900S Operating Manual FIGURE A 8 470 30S N01 00 MACHINE ARM...
Page 69: ...P N 90075 Rev 1 Page 57 FIGURE A 9 470 31S N01 00 MACHINE ARM GENERAL PARTS...
Page 70: ...Page 58 VM1700S 1900S Operating Manual FIGURE A 10 470 33S N01 00 MACHINE ARM T 1400...
Page 71: ...P N 90075 Rev 1 Page 59 FIGURE A 11 470 40S N01 00 BALL JOINT COUPLING...
Page 72: ...Page 60 VM1700S 1900S Operating Manual FIGURE A 12 470 41S N01 00 TYP 15...
Page 73: ...P N 90075 Rev 1 Page 61 FIGURE A 13 170 10S N01 00...
Page 74: ...Page 62 VM1700S 1900S Operating Manual FIGURE A 14 470 42S N01 00 TYP 25...
Page 75: ...P N 90075 Rev 1 Page 63 FIGURE A 15 170 40S N01 00...
Page 76: ...Page 64 VM1700S 1900S Operating Manual Mounting system...
Page 77: ...P N 90075 Rev 1 Page 65...
Page 78: ...Page 66 VM1700S 1900S Operating Manual...
Page 79: ...P N 90075 Rev 1 Page 67...
Page 80: ...Page 68 VM1700S 1900S Operating Manual FIGURE A 16 470 50S N01 00 MOUNTING SYSTEM...
Page 81: ...P N 90075 Rev 1 Page 69 FIGURE A 17 470 51S N01 00 TILTING ADAPTER...
Page 82: ...Page 70 VM1700S 1900S Operating Manual FIGURE A 18 470 52S N01 00 FLANGE SETUP...
Page 83: ...P N 90075 Rev 1 Page 71 Tooling FIGURE A 19 LIST OF ABRASIVES...
Page 84: ...Page 72 VM1700S 1900S Operating Manual FIGURE A 20 470 70S N01 00 TOOLING...
Page 85: ...P N 90075 Rev 1 Page 73 FIGURE A 21 470 71S N01 00 PLANET WHEELS DN 200 DN 500...
Page 86: ...Page 74 VM1700S 1900S Operating Manual FIGURE A 22 470 72S N01 00 PLANET WHEELS DN 500 DN 700...
Page 87: ...P N 90075 Rev 1 Page 75 FIGURE A 23 470 76S N01 00 EXTENSION FROM DN1000 TO DN1200...
Page 89: ...P N 90075 Rev 1 Page 77 FIGURE A 25 470 80S N01 00 ABRASIVES...
Page 90: ...Page 78 VM1700S 1900S Operating Manual FIGURE A 26 240 81S N01 00 ABRASIVES VM 2350...
Page 91: ...P N 90075 Rev 1 Page 79 FIGURE A 27 240 84S N01 00 ABRASIVES VM 2500...
Page 92: ...Page 80 VM1700S 1900S Operating Manual This page intentionally left blank...
Page 93: ......
Page 94: ......