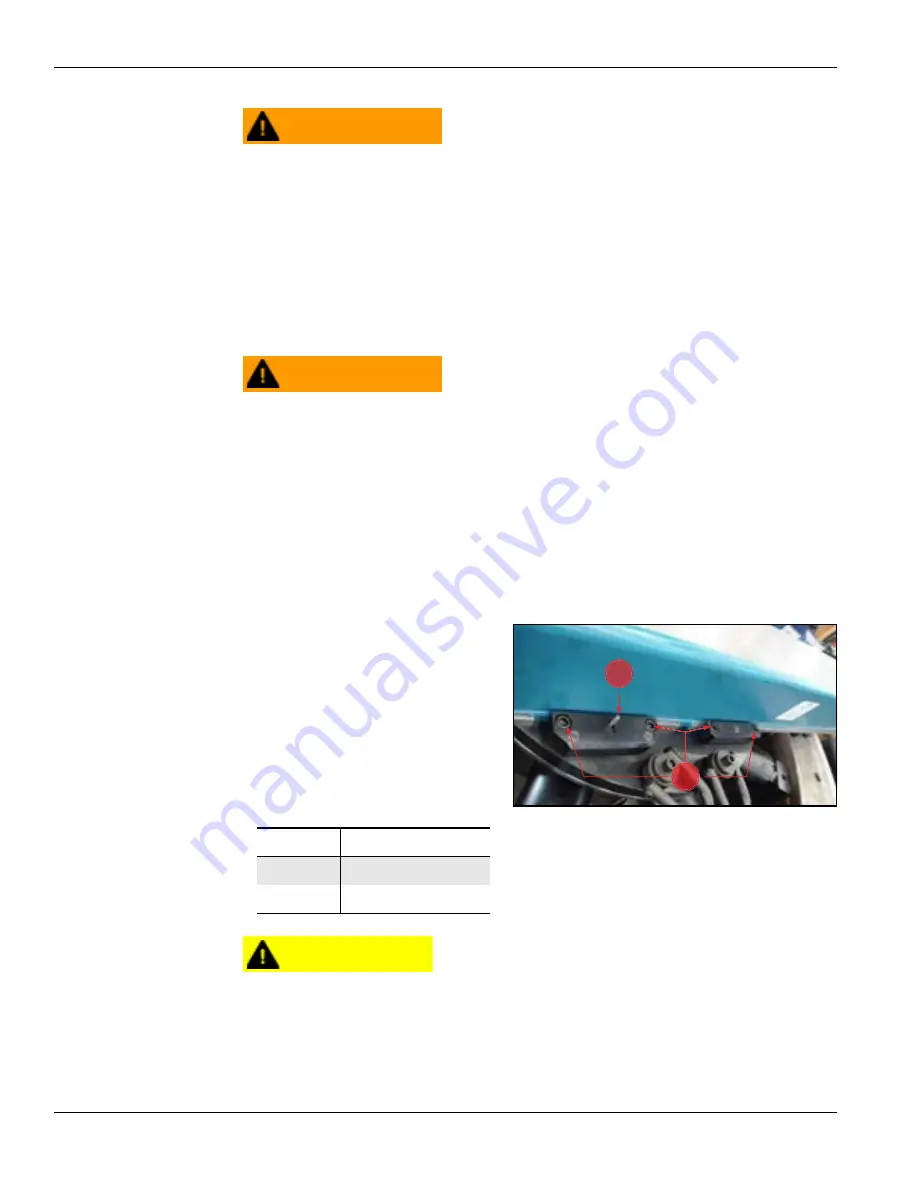
Mounting the machining arm
Page 36
CM6200 Operating Manual
WARNING
Tighten the clamp bolts to 110 ft-lb (150 Nm) to prevent unexpected
movement that could cause serious injury or death.
T
IP
:
The selector pin does not need to be engaged in a notch after the
turning arm adjustment. It is intended just to limit the turning arm’s
maximum amount of travel in the event that the turning arm comes
loose during operation.
WARNING
Do not disable the safety stop pin. The safety stop pin is intended to
prevent unwanted shifting of the machining arm, which could result in
serious injury or death.
3.6.2
Repositioning the machining arm
The machining arm is incrementally adjustable for versatile positioning and to
clear obstructions.
Do the following to reposition the machining arm:
1. Loosen the screws holding the four clamps.
2. Hold the safety stop pin
3. Slide the arm to the neces-
sary position.
4. Release the safety stop pin.
5. Re-tighten the clamps.
CAUTION
After adjusting the machining arm, make sure that the counterweight is
set to the corresponding bolt location increment.
For precise machining and to avoid damage to the machine, the
counterweight and machining arm should always be equally spaced
from the center of the machine.
T
ABLE
3-7. C
LAMP
SCREWS
AND
STOP
PIN
IDENTIFICATION
Number
Component
1
Stop pin
2
Clamp screws
F
IGURE
3-19. C
LAMP
SCREWS
AND
STOP
PIN
1
2
Summary of Contents for CM6200
Page 2: ......
Page 4: ...Page B CM6200 Operating Manual CLIMAX GLOBAL LOCATIONS...
Page 5: ...P N 63674 Rev 9 Page C CE DOCUMENTATION...
Page 8: ...Page F CM6200 Operating Manual This page intentionally left blank...
Page 18: ...Page x CM6200 Operating Manual This page intentionally left blank...
Page 70: ...Installing cables Page 52 CM6200 Operating Manual This page intentionally left blank...
Page 90: ...Control pendant Page 72 CM6200 Operating Manual 4 2 9 Pop up screens...
Page 91: ...Control pendant P N 63674 Rev 9 Page 73 4 2 10 Alarm history screens...
Page 126: ...MR J3 servo amplifier error codes Page 108 CM6200 Operating Manual...
Page 127: ...MR J3 servo amplifier error codes P N 63674 Rev 9 Page 109...
Page 128: ...MR J3 servo amplifier error codes Page 110 CM6200 Operating Manual...
Page 129: ...MR J3 servo amplifier error codes P N 63674 Rev 9 Page 111...
Page 130: ...MR J3 servo amplifier error codes Page 112 CM6200 Operating Manual...
Page 131: ...MR J3 servo amplifier error codes P N 63674 Rev 9 Page 113...
Page 132: ...MR J3 servo amplifier error codes Page 114 CM6200 Operating Manual...
Page 178: ...Page 160 CM6200 Operating Manual FIGURE B 1 MR J3 AND MR J4 PENDANT CABLE SCHEMATIC P N E00009...
Page 179: ...P N 63674 Rev 9 Page 161 FIGURE B 2 MR J3 SYSTEM LAYOUT P N A00033...
Page 180: ...Page 162 CM6200 Operating Manual FIGURE B 3 MR J3 AND MR J4 MILL TETHER SCHEMATIC P N B00070...
Page 181: ...P N 63674 Rev 9 Page 163 FIGURE B 4 MR J3 AND MR J4 JUNCTION BOX ASSEMBLY P N B00083...
Page 183: ...P N 63674 Rev 9 Page 165 FIGURE B 6 MR J3 CONTROL PANEL EXTERIOR ASSEMBLY SHEET 1 P N B00116...
Page 185: ...P N 63674 Rev 9 Page 167 FIGURE B 8 MR J3 SCHEMATIC SHEET 1 P N C00088...
Page 186: ...Page 168 CM6200 Operating Manual FIGURE B 9 MR J3 SCHEMATIC SHEET 2 P N C00088...
Page 187: ...P N 63674 Rev 9 Page 169 FIGURE B 10 MR J3 SCHEMATIC SHEET 3 P N C00088...
Page 188: ...Page 170 CM6200 Operating Manual FIGURE B 11 MR J4 LAYOUT P N A00093...
Page 189: ...P N 63674 Rev 9 Page 171 FIGURE B 12 MR J4 CONTROL PANEL ASSEMBLY EXTERIOR P N B000394...
Page 190: ...Page 172 CM6200 Operating Manual FIGURE B 13 MR J4 CONTROL PANEL ASSEMBLY INTERIOR P N B00394...
Page 194: ...Page 176 CM6200 Operating Manual This page intentionally left blank...
Page 196: ...Page 178 CM6200 Operating Manual This page intentionally left blank...
Page 198: ...Page 180 CM6200 Operating Manual This page intentionally left blank...
Page 199: ......
Page 200: ......
Page 201: ......
Page 202: ......
Page 203: ......
Page 204: ......
Page 205: ......
Page 206: ......
Page 207: ......
Page 208: ......
Page 209: ......
Page 210: ......
Page 211: ......
Page 212: ......
Page 213: ......
Page 214: ......
Page 215: ......
Page 216: ......
Page 217: ......
Page 218: ......
Page 219: ......
Page 220: ......
Page 221: ......
Page 222: ......
Page 223: ......
Page 224: ......
Page 225: ......
Page 226: ......
Page 227: ......
Page 228: ......
Page 229: ......
Page 230: ......
Page 231: ......
Page 232: ......
Page 233: ......
Page 234: ......
Page 235: ......
Page 236: ......
Page 237: ......
Page 238: ......
Page 239: ......
Page 240: ......
Page 241: ......
Page 242: ......
Page 243: ......
Page 244: ......
Page 245: ......
Page 246: ......
Page 247: ......
Page 248: ......
Page 249: ......
Page 250: ......
Page 251: ......
Page 252: ......
Page 253: ......
Page 254: ......
Page 255: ......
Page 256: ......
Page 257: ......
Page 258: ......
Page 259: ......
Page 260: ......
Page 261: ......
Page 262: ......
Page 263: ......
Page 264: ......
Page 265: ......
Page 266: ......
Page 267: ......
Page 268: ......
Page 269: ......
Page 270: ......
Page 271: ......
Page 272: ......
Page 273: ......
Page 274: ......
Page 275: ......
Page 276: ......
Page 277: ......
Page 278: ......
Page 279: ......
Page 280: ......
Page 281: ......
Page 282: ......
Page 283: ......
Page 284: ......
Page 285: ......
Page 286: ......
Page 287: ......
Page 288: ......
Page 289: ......
Page 290: ......
Page 291: ......
Page 292: ......
Page 293: ......
Page 294: ......
Page 295: ......
Page 296: ......
Page 297: ......
Page 298: ......
Page 299: ......
Page 300: ......
Page 301: ......
Page 302: ......
Page 303: ......
Page 304: ......
Page 305: ......
Page 306: ......
Page 307: ......
Page 308: ......
Page 309: ......
Page 310: ......
Page 311: ......
Page 312: ......
Page 313: ......
Page 314: ......
Page 315: ......
Page 316: ......
Page 317: ......
Page 318: ......
Page 319: ......
Page 320: ......
Page 321: ......
Page 322: ......
Page 323: ......
Page 324: ......
Page 325: ......
Page 326: ......
Page 327: ......
Page 328: ......
Page 329: ......
Page 330: ......
Page 331: ......
Page 332: ......
Page 333: ......
Page 334: ......