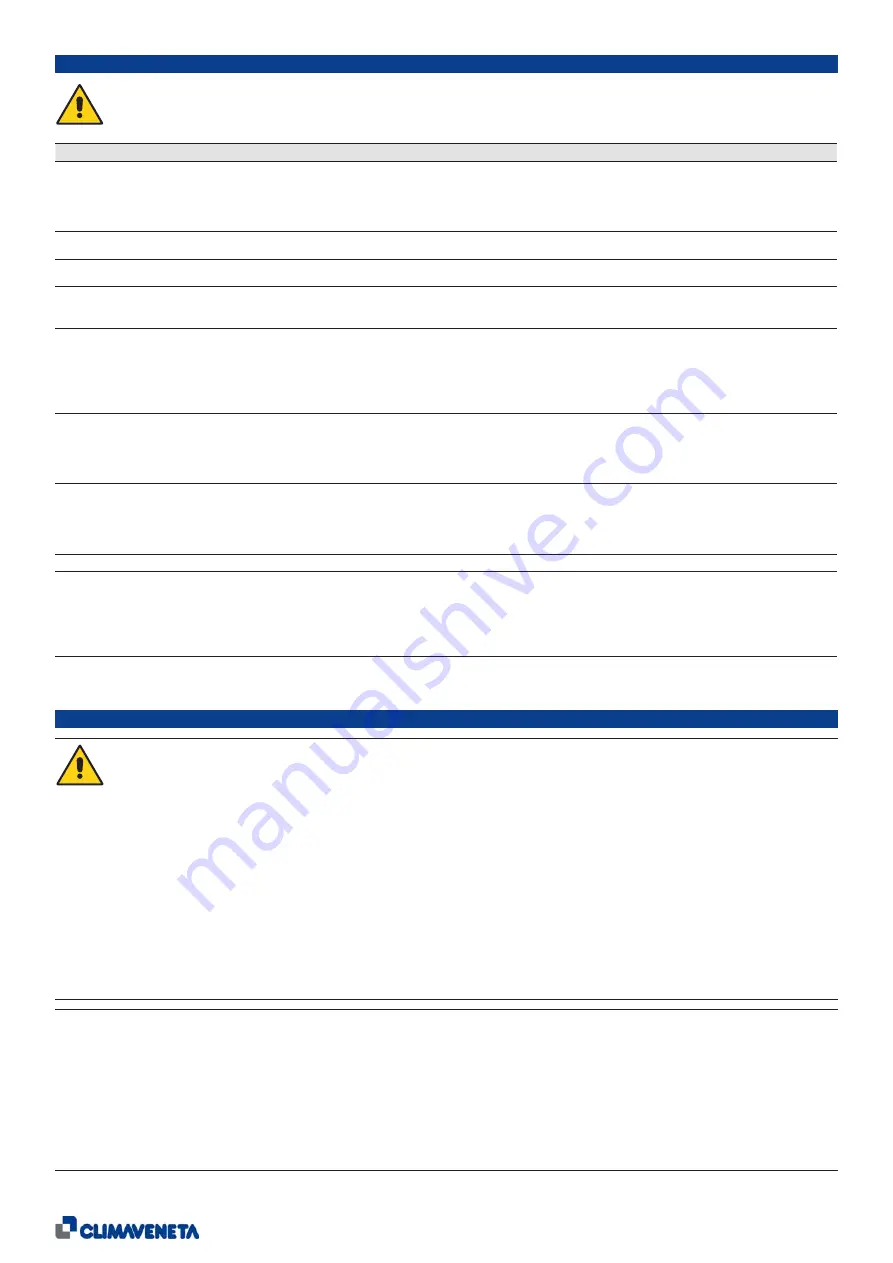
EN
29
ATTENTION ! Before accessing the unit, DISCONNECT IT FROM THE MAINS POWER SUPPLy using the upline multi-pole
switch.
In case any unexpected problems arise, promptly call in the Technical Assistance Service.
FAULT
POSSIBLE REASONS - CONTROL - REMEDIES
1 Insufficient outlet air
▪ Incorrect speed setting on the control panel: Select the correct speed on the control panel
▪ Air filter clogged: Clean the air filter
▪ Air flow obstructed (inlet and/or outlet): Remove the obstruction
▪ Pressure drop in the distribution system underestimated: Increase the speed of rotation of the fan
▪ Direction of rotation reversed: Check the wiring diagram and the electrical connections
2 Excessive air flow
▪ Pressure drop in the distribution system overestimated: Reduce the speed of rotation of the fan and/or insert
a pressure drop in the channel
3 Insufficient static pressure
▪ Speed of rotation too low: Increase the speed of rotation of the fan
▪ Direction of rotation reversed: Check the wiring diagram and the electrical connections
4 Excessive noise
▪ Excessive air flow: Reduce the air flow
▪ Sheet metal assemblies broken: Check the components are intact and replace any damaged parts
▪ Rotating parts unbalanced: Rebalance the fan impeller
5 The motor/fan doesn’t turn
▪ No power: Check the unit is powered
▪ The minimum water temperature thermostat “TM”, if present, tripped because the water temperature fell below
40°C (in the winter mode): Check the boiler
▪ Check that:
The mains power supply is connected - The switches and/or thermostats are in the exact operat-
ing position
▪ Check that:
There are no foreign bodies preventing the fan from rotating
6 The unit does not heat as
well as before
▪ No hot water: Check the hot water source (the boiler and the hot water pump)
▪ Control panel incorrectly set: Set the control panel correctly
▪ Check that: The air filter and the coil are clean
▪ Check that: No air has entered the hydraulic circuit by venting it through the relative vent valve
▪ Check that: The system is correctly balanced - The boiler works - The hot water pump works
7 The unit does not cool as
well as before
▪ No cold water: Check the chiller and the water pump
▪ Control panel incorrectly set: Set the control panel correctly
▪ Check that: The air filter and the coil are clean
▪ Check that: No air has entered the hydraulic circuit by venting it through the relative vent valve
▪ Check that: The system is correctly balanced - The chiller works - The cold water pump works
8 Overflowing water
▪ Trap clogged: Clean the trap - No trap: Fit a trap
9 Condensation on the exter-
nal structure of the unit
▪ The limit temperature and humidity conditions described in the Technical Bulletin (Operating limits) have been
reached: Raise the water temperature over the minimum limits described in the Technical Bulletin
▪ Problems with draining the condensate: check the condensate drip tray and drain
▪ Once the required ambient temperature has been reached, the fan stops while cold water continues to cir-
culate through the coil: Preset the plant adjustment system so that when the temperature is reached, the fan
stops and the water stops flowing through the coil (3-way valve, 2-way valve, pump OFF, chiller OFF, etc.)
TROUBLESHOOTING
GENERAL INFORMATION
After removing the packaging, make sure the contents are undamaged and complete. If this is not the case, contact the Technical Assist-
ance Service the unit was purchased from.
The equipment must be installed by an authorised company which must also give the owner a declaration of conformity of installation
performed according to the rules of good workmanship, that is, in compliance with current regulations and the instructions given by the
company in this booklet.
These units were designed and built to cool and/or heat rooms and must be used for that purpose consistently with their performance
characteristics.
The company declines all contractual and non-contractual liability for injury to persons or animals or damage to property deriving from
errors made during installation, adjustment and servicing and from improper use.
If water starts overflowing, turn the general system switch to “off” and close the water taps.
Built-in fancoil units are supplied without grilles and cabinet. Fit safety guards and air delivery/return grilles in order to prevent accidental
contact with the unit.
This instructions booklet is an integral part of the appliance and must always be kept with care. Make sure it ALWAYS remains with
the appliance, even if it is transferred to another owner or user or moved to another heating system. In case of loss or damage, please
contact your local Technical Assistance Service for a new copy.
Repair or maintenance work must be performed by the Technical Assistance Service or qualified staff as indicated in this booklet. Do not
modify or tamper with the appliance as this could generate hazardous situations. The manufacturer declines all liability for any damage
caused.
Children and unassisted adults with disabilities may not use the fancoil unit.
Do not touch the unit barefoot and if any parts of your body are wet or damp.
Before cleaning, always disconnect the electricity supply by turning off the main switch.
Do not modify the safety or adjustment devices without the manufacturer's permission and instructions.
Do not pull, detach or twist the wires from the unit even if it is disconnected from the mains power supply
Do not sit or stand on the unit or place anything on it.
Do not spray or throw water onto the unit.
Do not push sharp objects through the intake or outlet grills.
Do not open the covers on the unit or remove the safety elements without first turning off the general switch.
Do not disperse or dump packaging (cardboard, staples, plastic bags, etc.) and keep it out of reach of children as it is a potential source
of danger.
Summary of Contents for a-LIFE3
Page 30: ...REV01 2018 07 04 ...