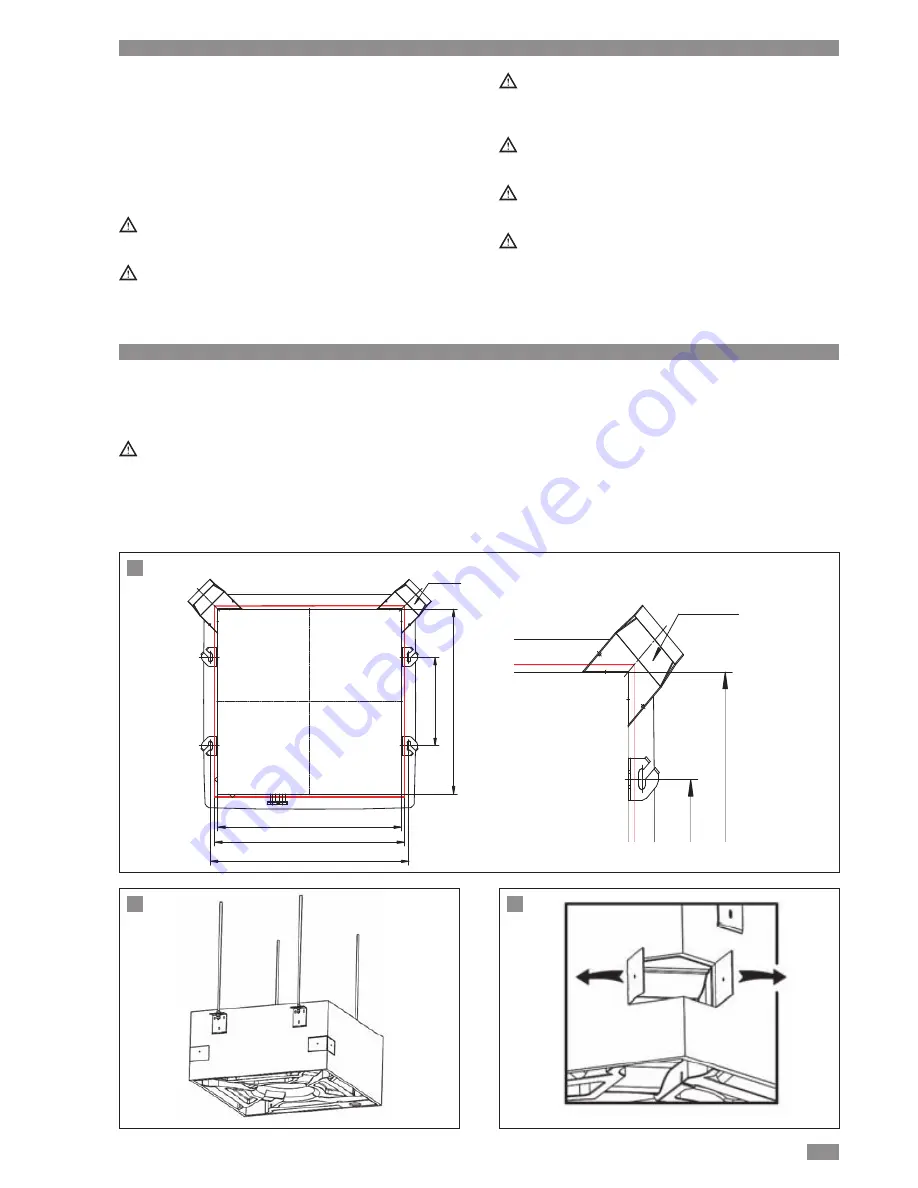
15
EN
Fresh air flange
(optional)
Fresh air flange
(optional)
580 mm
280 mm
580 mm
600x600 mm
632 mm
1
2
3
• To install the valves, see the instructions shown on the
valve kit instruction sheet. To make the connection to the
Cassette, please make reference to the unit drawings.
• In cold water installation, to avoid that the condensate
drops on the ceiling, it is necessary to insulate the piping,
the valves, and the coil’s connections.
• For valves electric connection refer to wiring diagram relat-
ed to selected control.
The cables must pass through the apposite fairleads and
flexible couplings.
The valves must be connected according to the suggest-
ed electric wiring diagrams.
If the proposed connections are not respected, there will
be the risk that the water overflows from the condensate
collection tray.
It is important that the valves open only when the fan is
working at one of the three speeds.
Check the seal in the most critical points of the plant
when it is filled of liquid for the first time.
The manufacturer cannot be consider responsible in
case of bad working or damages due to the drop of
valves sets purchased directly by the installer from other
suppliers.
Fresh air change
CHD – cassette units have primary air flow connection. This
air is mixed with the untreated room air inside the appliance.
The pressure at the treated air inlets is slightly below
atmospheric pressure. The low pressure should be dis-
regarded in the design of the treated air system.
Fresh Air Renewal Connection
The fresh air system for cassette unit allows up to 15% of
unit airflow as fresh air intake (per connection). Maximum 2
fresh air connections per unit are allowed.
1. The corners of the cassette allow separate ductwork to
be installed for outside air intake (Figure
1
).
2. Cut and remove thermal insulating material.
3. Open the mounting plate (Figure
2
and Figure
3
)
4. Install the flanges to casing and fix it with 2 screws.
Flange is rectangular duct with dimension 110 x 55mm.
INSTALLATION OF VALVE UNIT
Installation
DUCT INSTALLATION
Installation