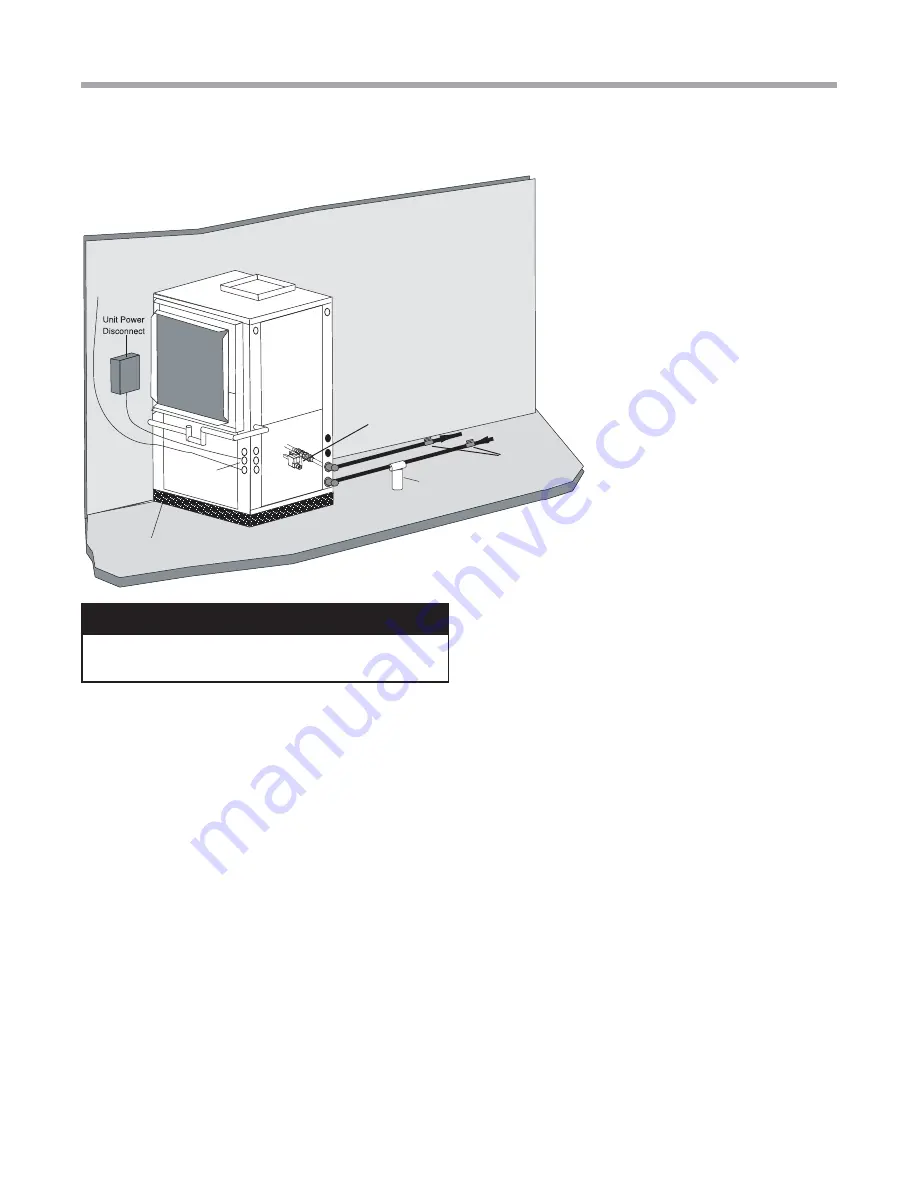
23
R e s i d e n t i a l D i g i t a l H & V - Tr a n q u i l i t y
®
2 2 D i g i t a l ( T Z ) S e r i e s - 6 0 H z H F C - 4 1 0 A
C r e a t e d : 2 6 O c t . , 2 0 1 1 B
c l i m a t e m a s t e r. c o m
High and
Low Voltage
Knockouts
Vibration Isolation Pad
To Thermostat
Internal Motorized
Modulating Valve
Water In
Water Out
Optional
Filter
Shut Off
Ball Valves
for Isolation
Ground-Water Heat Pump Applications
With industry-leading ‘plug and play options, for a ground
water (open) loop, a TZ unit with a motorized modulating
valve for the water circuit would be used.
Open Loop - Ground Water Systems
Typical open loop piping is shown in Figure 17. Shut off valves
should be included for ease of servicing. Boiler drains or other
valves should be “tee’d” into the lines to allow acid
fl
ushing
of the heat exchanger. Shut off valves should be positioned
to allow
fl
ow through the coax via the boiler drains without
allowing
fl
ow into the piping system. Pressure plugs built
into unit should be used to measure pressure drop. Water
temperature can be viewed on the communicating thermostat.
Piping materials should be limited to copper or PVC SCH80.
Note: Due to the pressure and temperature extremes, PVC
SCH40 is not recommended.
Water quantity should be plentiful and of good quality.
Consult table 3 for water quality requirements. The unit
can be ordered with either a copper or cupro-nickel water
heat exchanger. Consult table 3 to determine which heat
exchanger to use. Copper is recommended for closed loop
systems and open loop ground water systems that are not
high in mineral content or corrosiveness. In installations
anticipating heavy scale formation or in brackish water, a
cupro-nickel heat exchanger is recommended. In ground
water situations where scaling could be heavy or where
Figure 17: Typical Open Loop/Well Application
CAUTION!
CAUTION!
Refrigerant pressure activated water regulating
valves should never be used with this equipment.
biological growth such as iron bacteria will be present, an
open loop system is not recommended. Heat exchanger
coils may over time lose heat exchange capabilities due to
build up of mineral deposits. Heat exchangers must only
be serviced by a quali
fi
ed technician, as acid and special
pumping equipment is required. Desuperheater coils can
likewise become scaled and possibly plugged. In areas with
extremely hard water, the owner should be informed that the
heat exchanger may require occasional acid
fl
ushing. In some
cases, the desuperheater option should not be recommended
due to hard water conditions and additional maintenance
required.
Water Quality Standards
Table 3 should be consulted for water quality requirements.
Scaling potential should be assessed using the pH/
Calcium hardness method. If the pH <7.5 and the Calcium
hardness is less than 100 ppm, scaling potential is low. If
this method yields numbers out of range of those listed, the
Ryznar Stability and Langelier Saturation indecies should be
calculated. Use the appropriate scaling surface temperature
for the application, 150°F [66°C] for direct use (well water/
open loop) and DHW (desuperheater); 90°F [32°F] for
indirect use. A monitoring plan should be implemented in
these probable scaling situations. Other water quality issues
such as iron fouling, corrosion prevention and erosion and
clogging should be referenced in Table 3.
Pressure Tank and Pump
Use a closed, bladder-type pressure tank to minimize
mineral formation due to air exposure. The pressure tank
should be sized to provide at least one minute continuous
run time of the pump using its drawdown capacity rating to
prevent pump short cycling. Discharge water from the unit
is not contaminated in any manner and can be disposed
of in various ways, depending on local building codes (e.g.