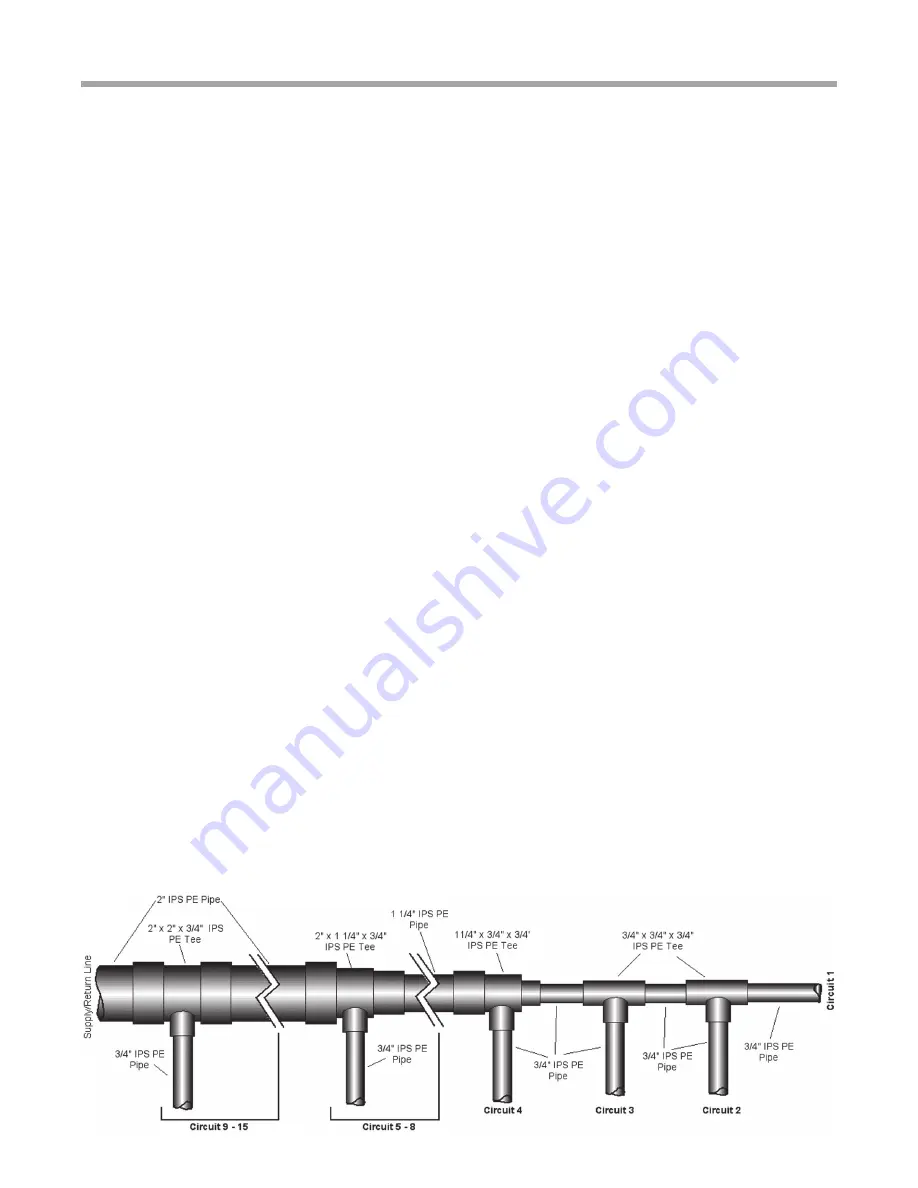
Flow Controller 3
R e v. : F e b u r a r y 9 , 2 0 1 6
20
G e o t h e r m a l H e a t P u m p S y s t e m s
Geothermal Closed Loop Design
In smaller loops of two tons [7 kW] or less, the reasons for
using parallel loops as listed above may be less obvious.
In these cases, series loops can have some additional
advantages:
• No header - fittings tend to be more expensive and
require extra labor and skill to install.
• Simple design - no confusing piping arrangement for
easier installation by less experienced installers.
Parallel Loop Design
Loop Configuration - Determining the style of loop primarily
depends on lot (yard) size and excavation costs. For instance,
a horizontal 1 pipe loop will have significantly (400%) more
trench than a horizontal 6 pipe loop. However, the 6 pipe will
have about 75% more feet of pipe. Therefore, if trenching
costs are higher than the extra pipe costs, the 6 pipe loop
is the best choice. Remember that labor is also a factor in
loop costs. The 6 pipe loop could also be chosen because
of the small available space. Generally a contractor will know
after a few installations which configuration is the most cost
effective. This information can be applied to later installations
for a more overall cost effective installation for the particular
area. Depth of the loop in horizontal systems generally does
not exceed 5 feet [1.5 meters] because of trench safety issues
and the sheer amount of soil required to move. In vertical
systems economic depth due to escalating drilling costs in
rock can sometimes require what is referred to as a parallel-
series loop. That is, a circuit will loop down and up through
two consecutive bores (series) to total the required circuit
length. Moisture content and soil types also effect the earth
loop heat exchanger design. Damp or saturated soil types will
result in shorter loop circuits than dry soil or sand.
Loop Circuiting - Loops should be designed with a
compromise between pressure drop and turbulent flow
(Reynold’s Number) in the heat exchange pipe for heat
transfer. Therefore the following rules should be observed
when designing a loop:
• 3 gpm per ton [3.23 l/m per kW] flow rate (2.25 gpm per
ton [2.41 l/m per kW] minimum). In larger systems 2.5 to
2.7 gpm per ton [2.41 to 2.90 l/m per kW] is adequate in
most cases. Selecting pumps to attain exactly 3 gpm per
ton [3.23 l/m per kW] is generally not cost effective from
an operating cost standpoint.
• One circuit per nominal equipment ton [3.5 kW] with
3/4” IPS and 1” IPS circuit per ton [3.5 kW]. This rule can
be deviated by one circuit or so for different
loop configurations.
Header Design - Headers for parallel loops should be
designed with two factors in mind, the first is pressure
drop, and the second is ability to purge all of the air from
the system (“flushability”). The header shown in Figure 13A
is a standard header design through 15 tons [52.8 kW] for
polyethylene pipe with 2” supply and return runouts. The
header shown in Figure 13B is a standard header design
through 5 tons [17.6 kW] for polyethylene pipe using 1-1/4”
supply and return runouts. Notice the reduction of pipe from
2” IPS supply/return circuits 15 to 8 to 1-1/4” IPS pipe for
circuits 7 to 4 to 3/4” IPS to supply circuits 3, 2, and 1. This
allows minimum pressure drop while still maintaining 2 fps
[0.6 m/s] velocity throughout the header under normal flow
conditions (3 gpm/ton [3.23 l/m per kW]), thus the header
as shown is self-flushing under normal flow conditions. This
leaves the circuits themselves (3/4” IPS) as the only section
of the loop not attaining 2 fps [0.6 m/s] flush velocity under
normal flow conditions (3 gpm per ton [3.23 l/m per kW],
normally 3 gpm [11.4 l/m] per circuit). Pipe diameter 3/4” IPS
requires 3.8 gpm [14.4 l/m] to attain 2 fps [0.6 m/s] velocity.
Therefore, to calculate flushing requirements for any PE loop
using the header styles shown, simply multiply the number
of circuits by the flushing flow rate of each circuit (3.8 gpm
for 2 fps velocity [14.4 l/m for 0.6 m/s]). For instance, on a 5
circuit loop, the flush flow rate is 5 circuits x 3.8 gpm/circuit
= 19 gpm [5 circuits x 14.4 l/m per circuit = 72 l/m or 1.2 l/s].
NOTICE
: Whenever designing an earth loop heat exchanger,
always assume the worst case, soil and moisture conditions
at the job site in the final design. In other words, if part of the
loop field is saturated clay, and the remainder is damp clay,
assume damp clay for design criteria.
Headers that utilize large diameter pipe feeding the last
circuits should not be used. PE 1-1/4” IPS pipe requires 9.5