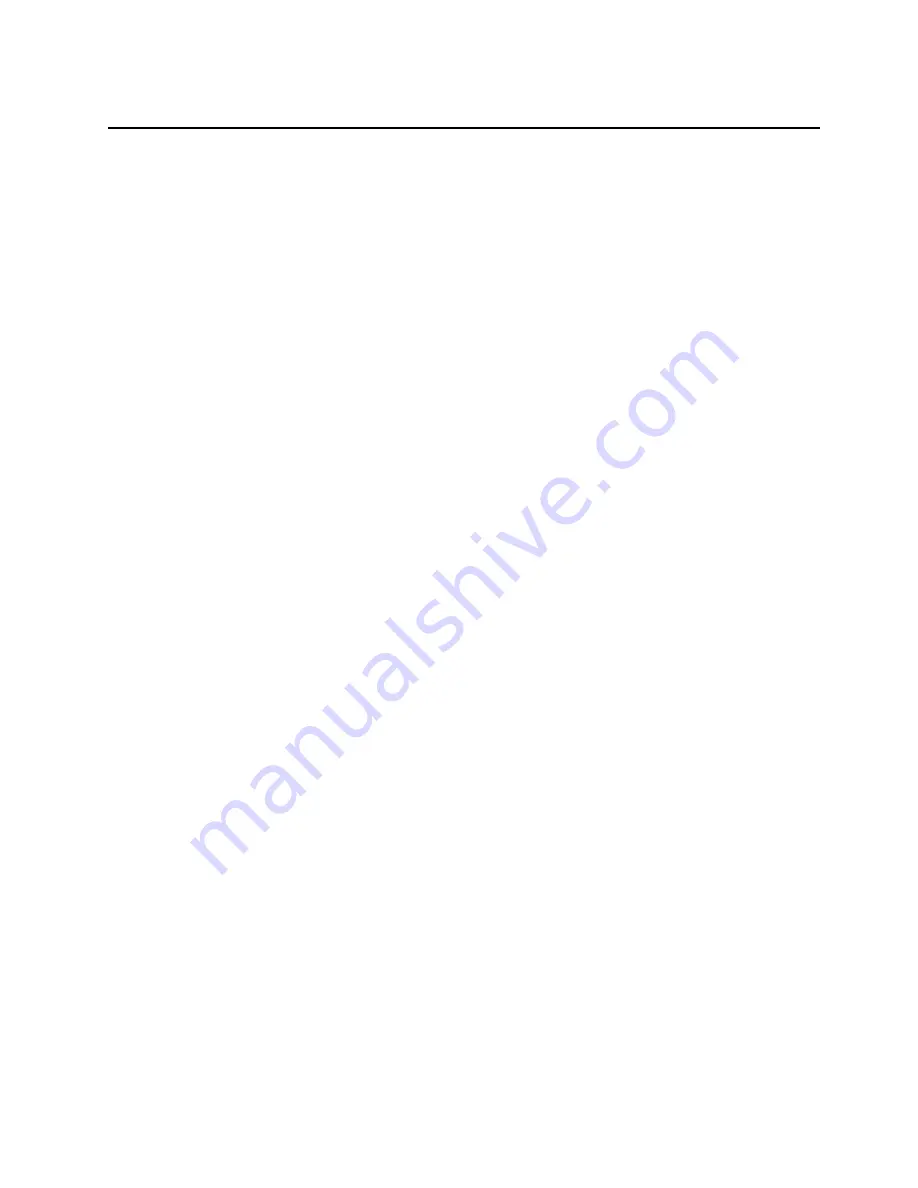
Operator’s Manual
P/N-260APC-A
______________________________________________________________________________
5
Install a sediment trap (drip leg) in the gas supply line,
and then connect gas supply piping to the boiler gas valve
piping. GAS-FIRED EQUIPMENT IS DESIGNED FOR
INSTALLATION ONLY IN NONCOMBUSJJBLE
LOCATIONS. THIS INCLUDES THE FLOOR-INC THAT
WILL BE DIRECTLY UNDER THE EQUIPMENT Location,
plumbing size, and pressure data are shown on the
specification sheet. Boilers rated at less than 225,000 Btu
require 3/4-inch 'PS gas supply piping, and boilers rated
at 225,000 Btu or more require 1-inch II'S gas supply
piping. Natural gas pressure must be between 4" -14"
water column and LP gas supply pressure must be
between 12" - 14" water column. NEVER EXCEED 14"
WATER COLUMN (1/2 psi) GAS PRESSURE. If the gas
supply pressure exceeds 14" water column, a pressure-
regulating valve must be installed in the gas plumbing to
reduce the gas pressure to less than 14" water column.
Installation must be in accordance with local codes, or in
the absence of local codes, with the National Fuel Gas
Code, ANSI Z223.1-1984. Installation in Canada must be
in accordance with Installation codes for Gas Burning
Appliances and Equipment B149.1 and B149.2. Use a gas
pipe joint compound, which is resistant to LP gas. Turn
the gas valve control knob to ON (the word "on" the knob
will be opposite the index on the valve's body). Test all
pipe joints for leaks with soap and water solutions. Never
obstruct the flow of combustion and ventilation air
Observe all clearance requirements to provide adequate
air openings into the combustion chamber. The appliance
and it's individual shutoff valve must be disconnected from
the gas supply piping system during any pressure testing
of that system at test pressures in excess of 14" water
column (1/2 psi or 3.45 k}'a). The appliance must be
isolated from the gas supply piping system at test
pressures equal to or less than 14" water column (1/2 psi
or 3.45 kpa). A permanent 115-volt electrical connection is
required at the junction box. The junction box location is
shown on the specification sheet. The installer must
electrically ground the unit.
For Electric-Powered Steam Generators:
Connect
electric power: location and data are shown on the
specification sheet. Provide connection as required by the
unit, either directly to the single contactor, or to the
terminal block (when equipped with multiple contactors).
Electric supply must match power requirements specified
on the data plate inside the base cabinet. The copper
wiring size must be adequate to carry the required current
at the rated voltage. A separate fused disconnect switch
must be supplied and installed. The installer must
electrically ground the unit
For Steam Coil Steam Generators:
Connect steam
supply piping to the input side of the steam coil. Location
and pressure data are shown on the specification sheet.
Incoming steam pressure must be regulated between 35
and 45 psi. A 3 /4inch strainer, equipped with a 20 mesh
stainless steel screen, must be supplied and installed at
the incoming steam connection
point. Flush the steam
line thoroughly before connecting it to the boiler. To
ensure an adequate volume of steam, the branch steam
supply line must be 3/~inch 'PS minimum. Connect the
inverted bucket trap to the outlet end of the steam coil. Pill
the trap with water before installing it. A permanent 115-
volt electrical connection is required at the junction box.
The junction box location is shown on the specification
sheet. The installer must electrically ground the unit.
For Direct-Steam Connected Steamers and Kettles:
Connect steam supply piping to the input side of the line
strainer. Location and pressure data are shown on the
specification sheet. Flush the steam line thoroughly
before connecting it to the steamer. To ensure an
adequate volume of steam, the branch steam supply line
must be 3/4 inch 'PSI 'minimum. Direct-steam-connected
kettles require 1 /2-inch 'PS pipe if the kettle total capacity
is 20 gallons or less, and 3/4-inch 'PS pipe if the total
capacity exceeds 20 gallons.) A permanent 115-volt
electrical connection is required at the junction box. The
junction box location is shown on the specification sheet.
The installer must electrically ground the unit
INSTALLATION CHECKS
Proper operation of the Cleveland Convection Steamer is
dependent upon proper installation. After the steamer has
been installed, a few quick checks could save
unnecessary service calls.
1. The unit must be level.
2.
The Convection Steamer requires a cold water
connection for proper efficient operation. DO NOT
USE HOT WATER. The cold water must be
connected to the line strainer, located at the front
lower right of the steamer base.
3.
Check that the manual water supply valve is open.
4. Check all water supply lines and valves for leaks.
5.
Check that the water supply pressure and water
quality meets the requirements of installation
paragraphs.
6.
On electrical units, verify that the supply voltage
meets the voltage requirements on the rating plate
inside the base cabinet and the voltage shown on the
packing slip. Verify that the unit is protected with a
separate fused disconnect and is properly grounded
in accordance with the National Electric Code.
On gas, steam coil and dir'cct4team-connected units
7. On all gas, steam-coil, and direct steam connected
units, verify that there is a 115-Volt connection at the
handy-box located on the left side of the base.