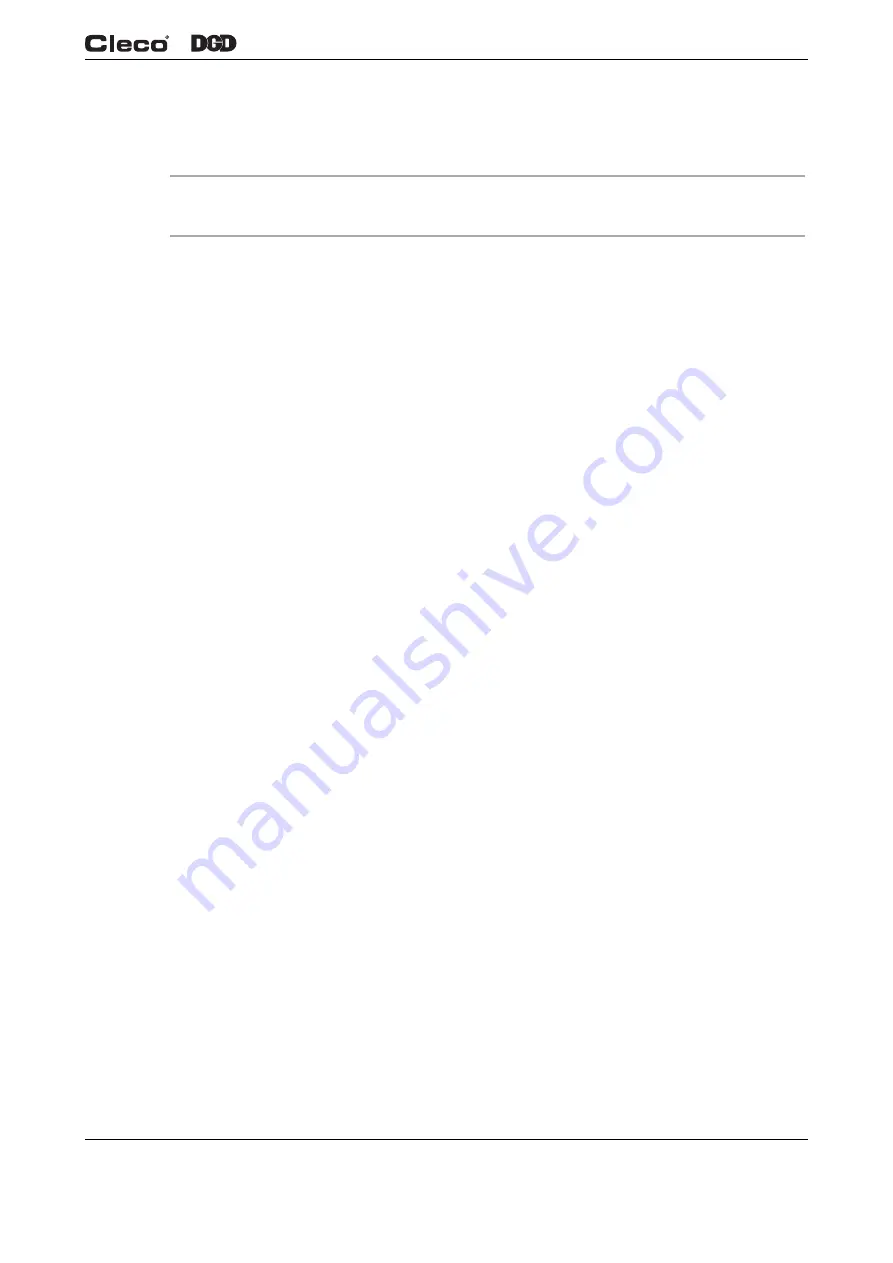
en01d441_bedingt.fm, 12.01.2017
P2174HW-EN 2017-01
5
Set-Up Guide
1
1.2
General Information
It is mandatory that national, state and local safety and wiring standards be followed during installation.
These standards take precedence over any information presented in this section.
•
Do not energize the unit until all connections have been properly made.
•
Equipment must be properly grounded before applying power. Units energized by cord and plug must be
connected to an approved and properly grounded receptacle.
•
All units must be energized by an isolated line.
•
The unit must always be closed and secured prior to energizing the unit.
•
Ensure the power switch is in the „off“ position prior to connecting the power cord.
Though it is not mandatory, the following instructions are highly recommended for the protected operation of
your unit.
•
Use oversized feeder lines to reduce electrical noise and voltage drop.
1.3
Checking your unit
Take time to ensure you have the required peripheral equipment and cables necessary to set-up and run
your unit. If you do not have all the necessary items, contact your distributor. Refer to Abb. 1-2: for an illus-
tration of your unit.
1.4
Software
Your unit has been preloaded with software and requires no additional software to begin your fastening pro-
cess. If you are interfacing your unit with an external computer, mPro-Remote interfacing software is
required.
1.5
Installing the Unit
1.5.1
Assembly
Each unit is used primarily as a single or multiple tool process/controller/monitor installed in a work station
or work area. It may be wall mounted, beam mounted, suspended overhead or pedestal mounted. Always
choose a stable location to avoid the possibility of unit damage and/or operator injury through hitting, falling,
vibration or inconvenient mounting. All cables attached to the unit should be located and secured so that
they cannot cause injury to the operator or to passersby. Like all electrical devices, the control system emit
some heat. It should therefore be positioned where air can circulate freely around the housing.
Refer to Abb. 1-3: for mounting hole dimensions.
1.5.2
Location considerations
Your unit should be located to allow access to the front panel and connectors. The unit should be installed
for unrestricted and comfortable viewing of the LCD screen by the operator. The LCD menu screen, key pad
and connectors must be readily accessible for the set-up. Dependent on the peripheral equipment pur-
chased, the unit may be located in a remote position but should still be accessible.
Attachment of accessories and tools should also be considered with the installation locations. Items to be
considered are:
CAUTION!
To avoid the hazard of electrical shock or burn, the following instructions must be adhered to. Failure to fol-
low these instructions may also cause damage to your unit and void existing warranties.