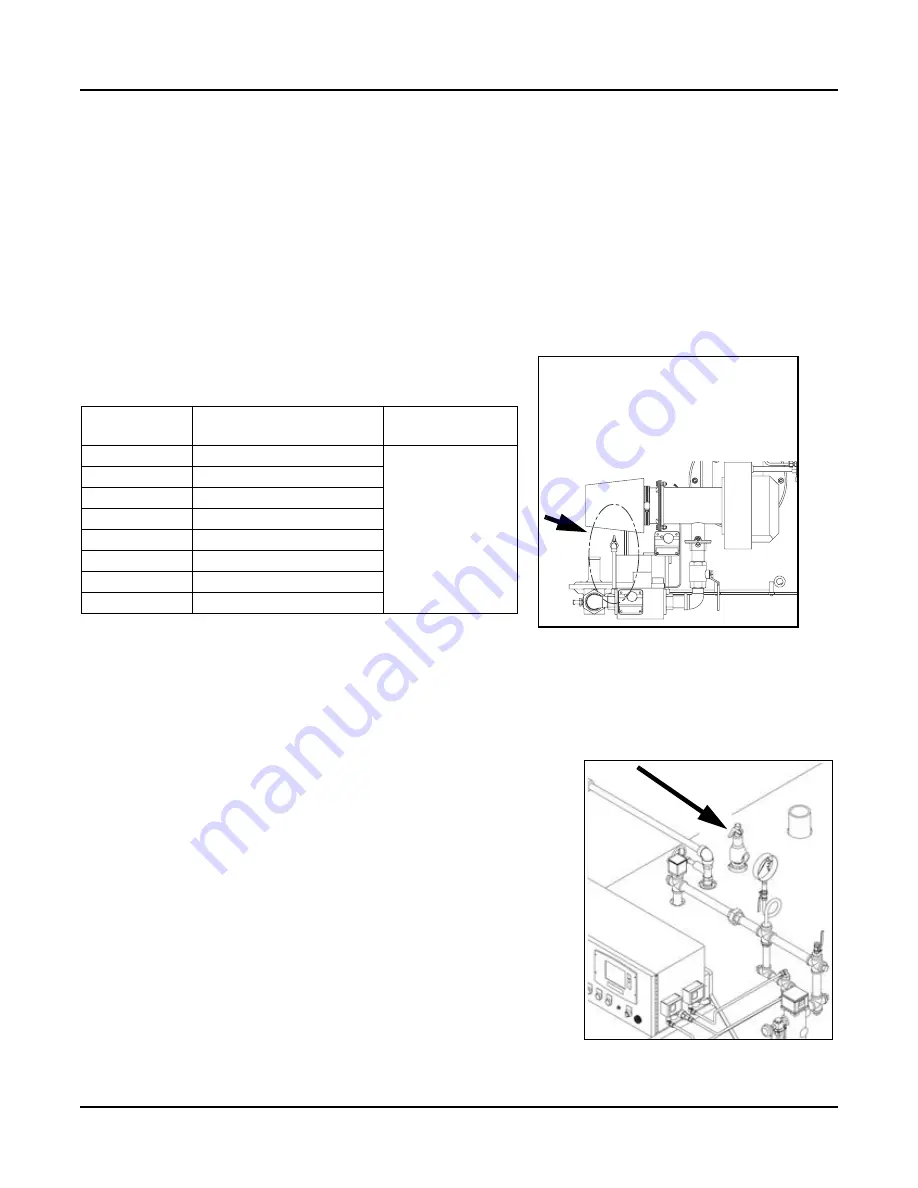
CFH Startup Guide
4
Part No. 750-293
1.2 Gas Piping
A manually operated shut-off valve and pressure regulator are provided as standard on the Model CFH boiler.
It is recommended to install an approved gas filter or strainer in the gas supply line to the boiler. Please inquire
with the local gas supply company.
The boiler shall be installed such that the gas ignition system components are protected from water (dripping,
spraying, etc.) during appliance operation and service.
If building supply gas pressure is greater than 1 psig (27.8” WC), an upstream regulator with overpressure
protection and proper gas venting will be required and must be piped to a safe point of discharge.
All gas piping and components to the boiler gas train connection must comply with NFPA 54, local codes,
and utility requirements as a minimum. Only gas approved fittings, valves, or pipe should be used. Standard
industry practice for gas piping is normally Schedule 40 black iron pipe and fittings.
See Table 1 for CFH gas pressure requirements.
1.3 Flue Gas Connection
The flue gases from the ClearFire boiler are removed via a gas-tight, temperature and corrosion resistant flue
gas pipeline. Only flue gas systems approved and tested by the relevant region or province are to be connected
to the ClearFire boiler. Refer to flue piping manufacturer for proper installation and sealing instructions.
See also Chapter 3 in the CFH Operation and Maintenance manual.
1.4 Boiler Water-Side Connections
A pressure relief valve (safety valve;
Figure 2
), provided with the boiler,
must be installed in the mounting provided and piped to a safe point
of discharge. Use pipe sealing compound and a flat sided wrench when
securing the safety relief valve. Do not use a pipe wrench and do not
over tighten the relief valve. The safety valve must be mounted in a
vertical position so that discharge piping and code-required drains can
be prop erly piped to prevent buildup of back pressure an d
accumulation of foreign material around the valve seat area.
Connection to the main steam header is made at the nozzle projecting
upward from the boiler shell.
Feedwater is introduced through the piping assembly installed on the
side of the boiler vessel.
Connections are provided for optional chemical feed, surface blowoff,
and overflow.
Table 1 CFH gas pressure requirements
Boiler HP
Minimum pressure required
at gas train connection
Max. pressure
10
7.2" w.c.
28” w.c.
15
7.3" w.c.
20
7.5" w.c.
25
7.7" w.c.
30
8.5" w.c.
40
11.0" w.c.
50
10.0" w.c.
60
10.0" w.c.
Note: To measure supply pressure
at the CFH gas valve, use the
test port on the valve inlet
flange (see below). Do not
use the leak test cocks to
measure gas pressure.
Figure 2 Pressure Relief Valve