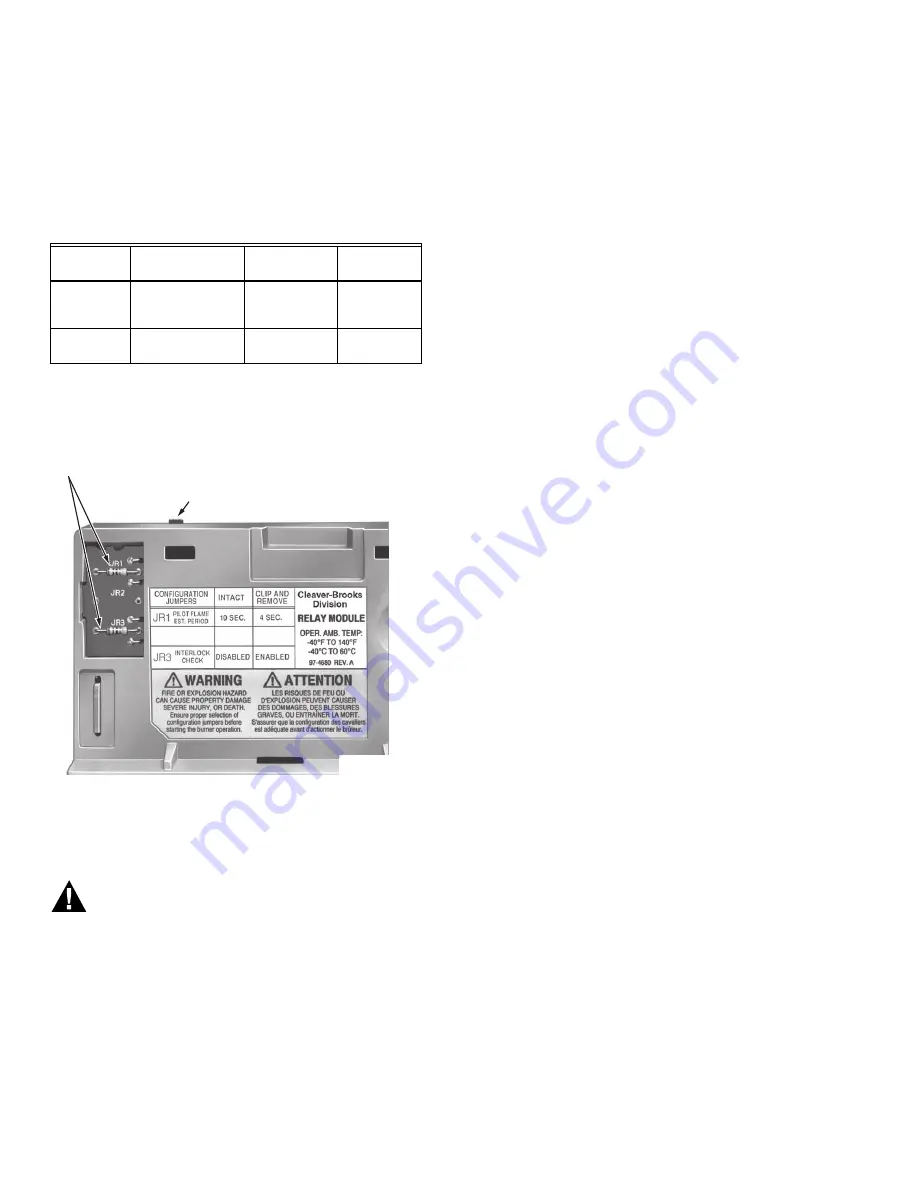
CB780/CB784 RELAY MODULES
32-00207—01
26
Selectable Site-Configurable
Jumpers
The CB780/CB784 has two site-configurable jumper
options; see Fig. 24 and Table 7. The site-configurable
jumpers should be clipped with side cutters and the
resistors removed from the Relay Module.
Table 7. Site Configurable Jumper Options.
NOTE:
For all standard installations, these jumpers
should be left intact, unless otherwise indicated
on wiring diagram. Removal after 200 hours of
operation will result in a hard lockout, Code 110.
Fig. 23. Selectable site-configurable jumpers.
STATIC CHECKOUT
WARNING
Electrical Shock Hazard and Explosion Hazard.
Can cause severe injury, death or property
damage.
1. Use extreme care while testing the system. Line
voltage is present on most terminal connections
when power is on.
2. Open the master switch before installing or
removing a jumper on the subbase.
3. Before continuing to the next test, be sure to
remove test jumper(s) used in the previous test.
4. Replace all limits and interlocks that are not
operating properly. Do not bypass limits and
interlocks.
5. Close all manual fuel shutoff valve(s) before
starting these tests.
After checking all wiring, perform this checkout before
installing the CB780/CB784 on the subbase. These tests
verify the Wiring Subbase is wired correctly, and the
external controllers, limits, interlocks, actuators, valves,
transformers, motors and other devices are operating
properly.
NOTE:
Do not perform a dielectric test with
theCB780/CB784 installed. Internal surge pro-
tectors will break down and conduct a current.
This could cause the CB780/CB784 to fail the
dielectric test or possibly destroy the internal
lightning and high current protection.
Equipment Recommended
1.
Voltmeter (1 megohm/volt minimum sensitivity) set
on the 0-300 Vac scale.
2.
Two jumper wires; no. 14 wire, insulated, 12 inches
(304.8 mm) long with insulated alligator clips at
both ends.
General Instructions
1.
Perform all applicable tests listed in Static Checkout,
Table 8, in the order listed.
2.
Make sure all manual fuel shutoff valve(s) are closed.
3.
Raise the setpoint of the operating controller to sim-
ulate a
call for heat
.
4.
For each test, open the master switch and install the
jumper wire(s) between the subbase wiring termi-
nals listed in the Test Jumpers column.
5.
Close the master switch before observing operation.
6.
Read the voltage between the subbase wiring termi-
nals listed in the Voltmeter column.
7.
If there is no voltage or the operation is abnormal,
check the circuits and external devices as described
in the last column.
8.
Check all wiring for correct connections, tight termi-
nal screws, correct wire, and proper wiring tech-
niques. Replace all damaged or incorrectly sized
wires.
9.
Replace faulty controllers, limits, interlocks, actua-
tors, valves, transformers, motors and other devices
as required.
10.
Ensure normal operation is obtained for each
required test before continuing the checkout.
11.
After completing each test, be sure to remove the
test jumper(s).
Jumper
Number
Description
Intact
Clipped
JR1
Pilot Flame
Establishing
Period (PFEP)
10 seconds
4 seconds
JR3
Start-up
Interlock Check
Disabled
Enabled
RUN/TEST SWITCH
SELECTABLE CONFIGURATION JUMPERS
M7397A