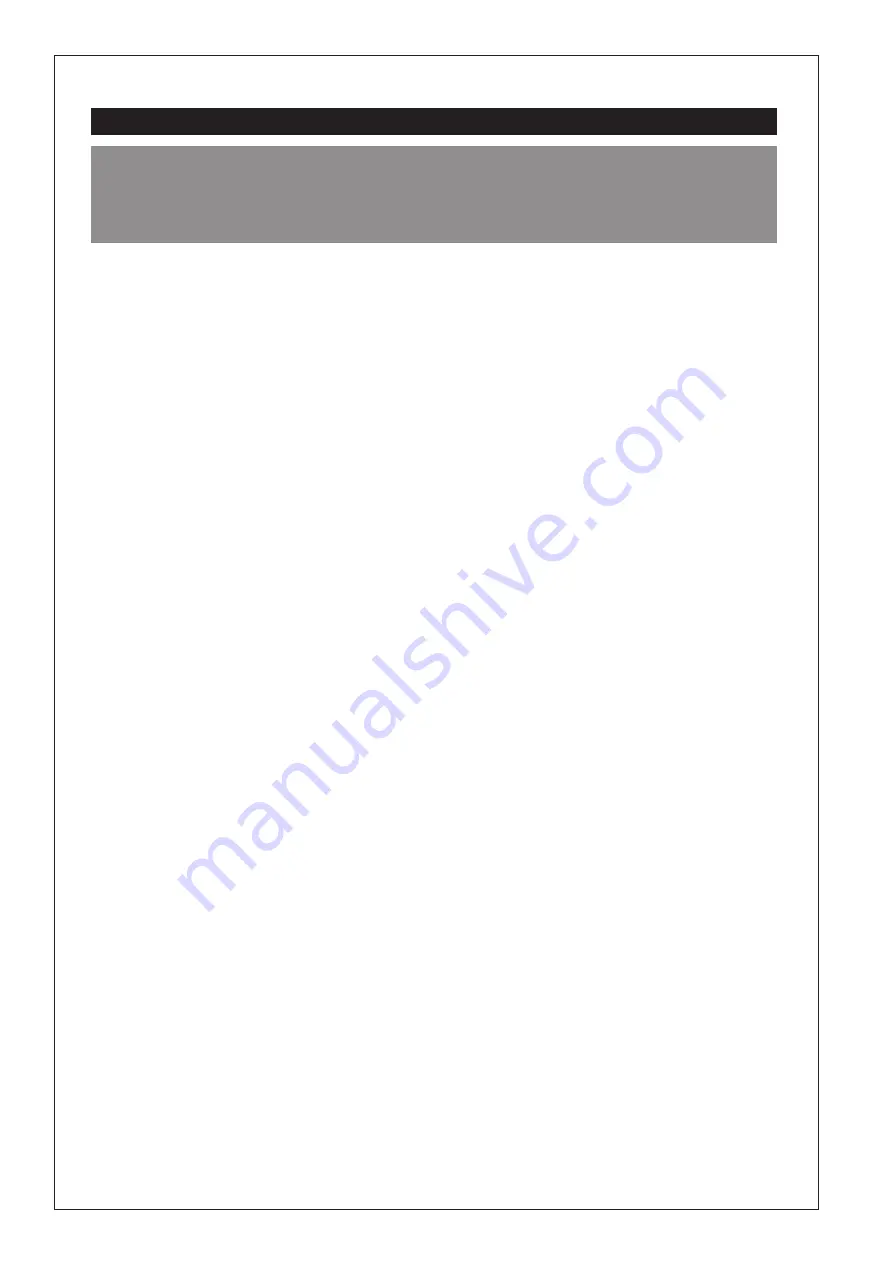
4
SAFETY PRECAUTIONS
WARNING!
As with all machinery, there are certain hazards involved with their operation and use. Exercising respect and
caution will considerably lessen the risk of personal injury. However, if normal safety precautions are
overlooked or ignored, personal injury to the operator or damage to property may result.
•
Ensure the site selected is large enough to accommodate the lift, including a safety area,
and with adequate height clearance, taking into account the size of vehicles expected to
be worked on. (see Assembly & Installation, p6).
•
Ensure the area on which the base is mounted is flat and level, and of sufficient strength to
adequately support the weight of the lift and vehicle, and is capable of recieving and
securing the foundation fittings. (see Assembly & Installation, p6).
•
Ensure adequate lighting is provided throughout the entire area.
•
ALWAYS wear shoes with non-skid soles and metal or reinforced toe-caps.
•
ALWAYS wear protective head cover, and protective eye shield.
•
DO NOT wear jewellery which may get caught in moving parts. Long hair should be contained.
•
NEVER exceed the load for which the machine was designed. If the load capacity and
other warning labels become defaced or illegible, have them replaced. (Contact your Clarke
dealer for replacements).
•
Before operating,ensure that all bolts, pins and securing devices are correctly in place and
in good condition. Check for signs of cracked welds, bent or loose pins or other signs of
structural damage. Do not use if any of these conditions exsist. Ensure repairs are carried out
by qualified persons only, or contact your nearest Clarke dealer.
•
Use ONLY those fittings and fixtures supplied. NEVER substitute bolts or pins or other
components, unless they are direct replacements from Clarke International.
•
DO NOT allow any person to operate the machine unless they are completely familiar with
all aspects of operation and have read this manual thoroughly.
•
DO NOT use the machine for lifting people or for any other use other than that for which it
was designed.
•
Ensure the machine is properly maintained at all times (see Maintenance).
•
If the machine has been subjected to an abnormal load or shock, remove it from service
immediately and have it fully inspected by a qualified person. If necessary, refer to your
Clarke dealer.
•
Before loading the machine, adjusting the arms etc., ensure the ON/OFF switch is set to
the ‘O’ (OFF) position.
•
Do not reverse a vehicle into position on the lift, unless it is rear engine drive, as the Short,
Hinged Arms, at the rear of the lift, must always support the engine.
•
Before locating the lifting arm pads on the lifting points, check to ensure the rubber pads
are free from oil or grease which could cause the pad to slip during operation. Never raise a
vehicle without the rubber pads in place. Replace them if they become damaged
•
Ensure the vehicle being lifted is completely stable and the lifting arms are located on the
recommended lifting points ONLY. If in doubt, ALWAYS consult the vehicle handbook to
determine where the lifting points are located.
•
NEVER operate the machine with any guard or cover removed.
•
Ensure that no equipment is connected to the vehicle when raising or lowering.