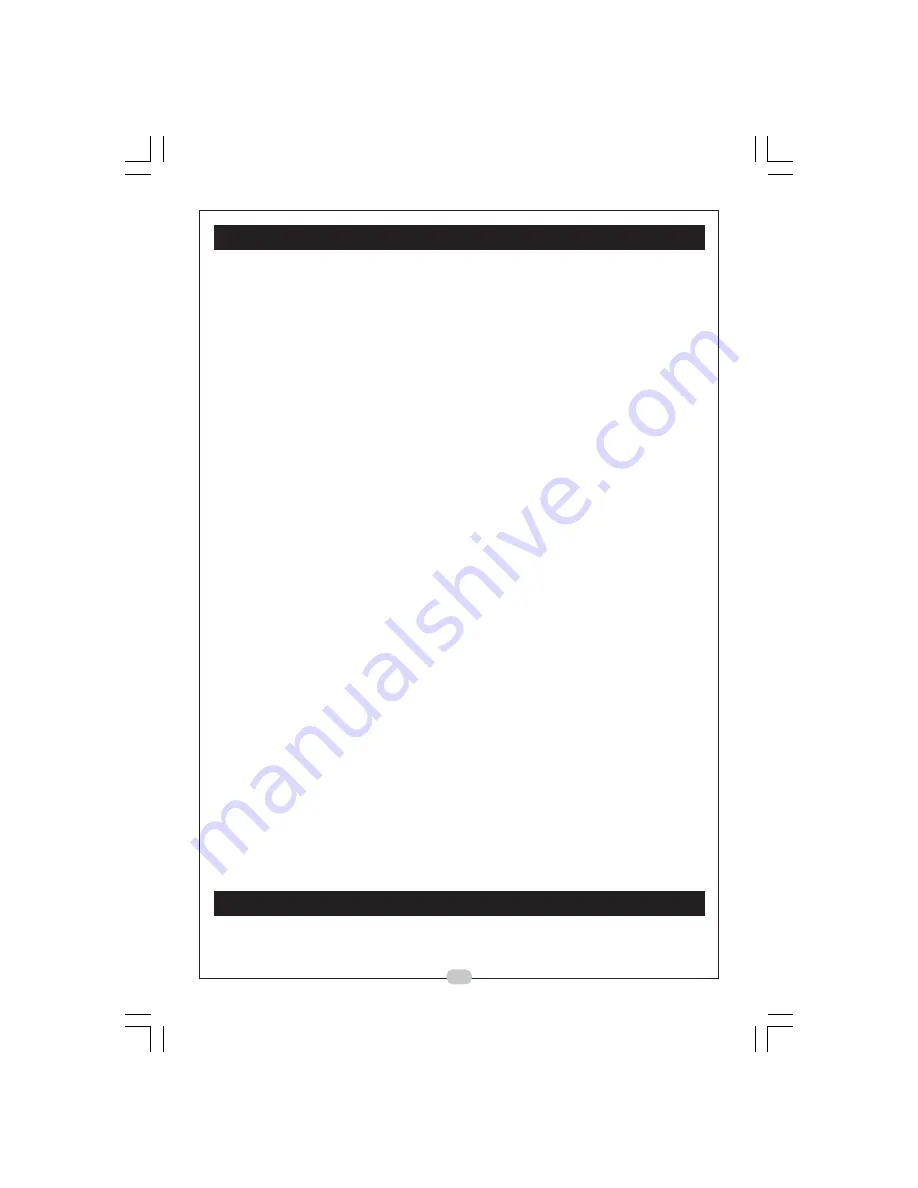
SAFETY PRECAUTIONS
Before using your compressor it is in your own interest to read and pay attention to
the following safety rules:
♦
COMPRESSED AIR IS DANGEROUS
- Never direct a jet of air at people or animals.
♦
Do not operate your air compressor with any guards removed.
♦
Electrical or mechanical repairs should only be carried out by a qualified
electrician/engineer. If you have a problem, contact your local dealer, or
our Service Department on
020 8988 7400
♦
Before attempting any repair ensure pressure is expelled from the air receiver
and disconnect from electrical supply.
♦
Do not leave pressure in air receiver overnight or when transporting.
♦
Do not adjust or tamper with any safety valves. The maximum working pressure
of the compressor is clearly stated on the machine.
♦
Exercise caution when transporting the machine to avoid tipping the machine over.
♦
Do not operate in a wet/damp environment.
♦
Locate your air compressor on a firm flat surface and ensure an adequate
supply of clean air is available to the pump unit.
♦
Do not exert any strain on electrical cables and ensure that air hoses are not
tangled or wrapped around machinery etc.
♦
The cylinder head and delivery pipes of your compressor become quite hot
during operation. Do not touch. After switching off remember to leave an
adequate cool-down period before touching.
♦
Ensure that any equipment/tool used in conjunction with your compressor
has a safe working pressure exceeding the output pressure of the machine.
♦
When disconnecting air hoses or other equipment from your compressor ensure
that the air supply is turned off at the machine outlet and expel all pressurised
air from within the air hose and other equipment attached to it.
♦
If using your compressor for paint spraying:
a)
Never spray close to any source of flame or heat.
b)
Always ensure that the spraying area has adequate fresh air ventilation.
c)
Hazardous paints require special apparatus (see paint manufacturers
recommendations).
♦
Never let anyone operate the compressor unless they have had the necessary
instructions.
♦
Permanently installed pipework systems should be designed and installed by
a competent engineer.
NOISE LEVELS
These machines produce noise levels in excess of 70dB(A). Persons working in the
vicinity of the machine must be provided with suitable ear protection.
4