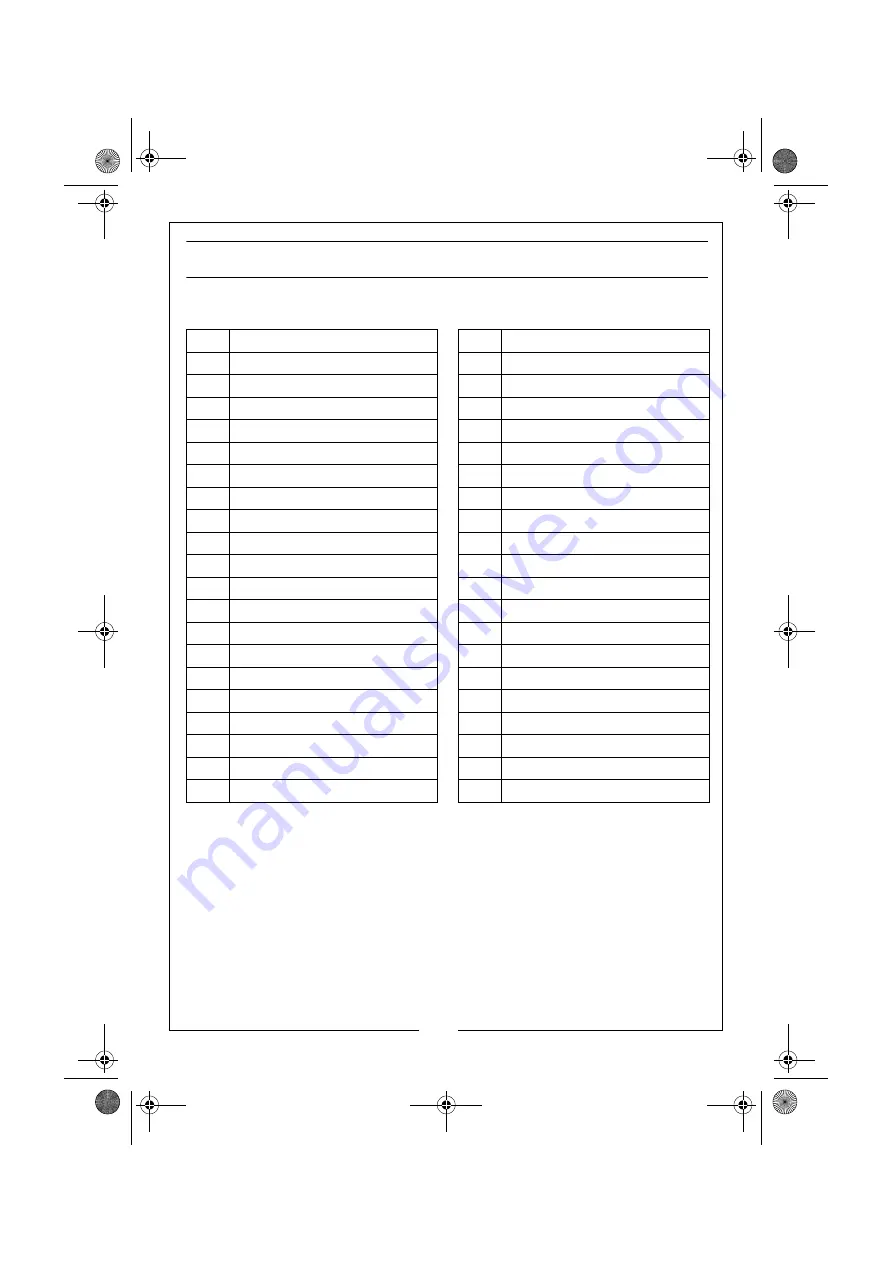
13
Parts & Service: 020 8988 7400 / E-mail: [email protected] or [email protected]
COMPONENT PARTS LIST
When ordering spare parts please quote the reference WG/CHD850 followed
by the number above.
No
Description
No
Description
1
Power Cable
21
Loose Rib 12mm
2
Cable Sleeve
22
Bearing
3
X-head Screw
23
Impact Spring
4
Cable Clamp
24
Drive Spindle
5
Capacitor
25
Woodruff Key
6
Trigger Assembly
26
Key Holder
7
Carbon Brush Holder
27
Spring
8
Spring
28
Impact Selector
9
Carbon Brush
29
Casing (LH)
10
Inductor
30
Air Vent
11
X-head Screw
31
Casing (RH)
12
Motor Stator
32
Casing Screw (top)
13
Motor Bearing
33
Casing Screw (rear)
14
Motor Armature
34
Casing Screw (front)
15
Motor Drive Bearing
35
Chuck
16
Drive Support Block
36
Chuck Retaining Screw
17
Oilite Bush
37
Auxiliary Handle
18
Steel Ball
38
Depth Stop Rod
19
Loose Rib 9mm
39
n/a
20
Spur Gear
40
Chuck Key
CHD850 Hammer Drill rev 4.fm Page 13 Monday, February 9, 2015 10:47 AM