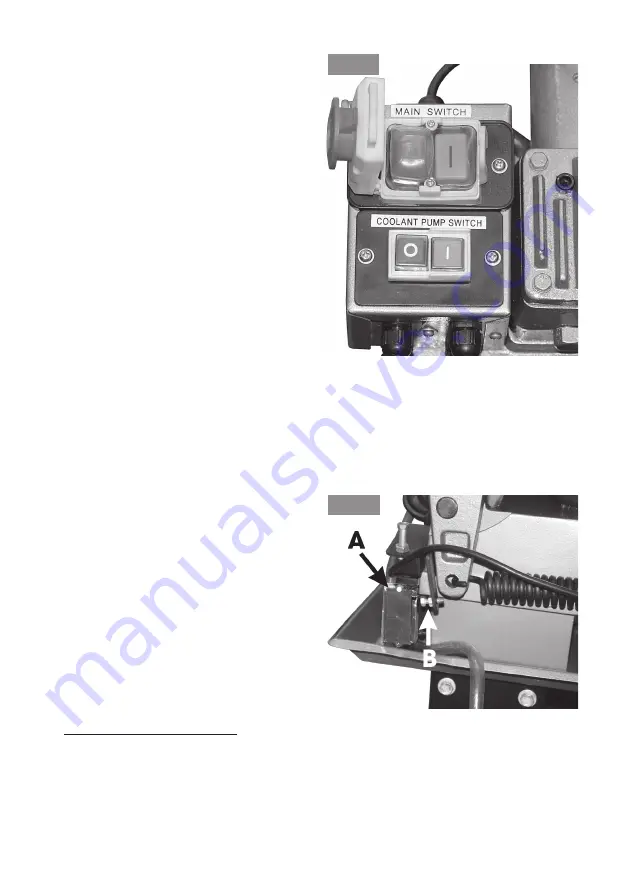
When the Arm reaches the bottom of
its travel, a bracket, attached to the
Arm and carrying an adjuster, shown at
‘B’ Fig.15, activates a microswitch, ‘A’
switching Off the machine. ALWAYS
ensure the adjuster is set so that the
microswitch operates correctly.
‘Running In’ the Blade
To gain the maximum working life from your blade it is also essential for a new
blade to be ‘RUN IN’ for a short period of time. This is done by applying a lighter
cutting pressure on the first few cuts made by the blade. As a guide the ‘Running
In’ cutting pressure should be half the normal cutting pressure. The cut will therefore
take longer to complete.
14
To switch OFF press the RED button
marked ‘O’,
NOTE: If this is the first time you have
operated your machine, or if a new
blade has been installed, allow the
blade to run completely off load for a
few minutes to allow the blade to settle.
With the blade running at full speed,
turn the Lever ‘B’Fig 3a, to the 6 o’clock
position again, then gently turn knob ‘A’
anticlockwise
so that the blade slowly
lowers at the desired rate, until it
contacts the workpiece and cutting
begins. Remember, do not start to cut
on a sharp edge.
At this point, switch ON the coolant
pump by pressing the GREEN button
marked ‘I’ (see Fig.14).
The rate of descent of the Arm determines the cutting rate and is therefore
controlled by the knob ‘A’, Fig 3a.
The cutting rate is dependant upon two main factors.......the type of material and
the thickness of cut, (which may not be constant). It therefore becomes a matter of
‘feel’. Ideally, blade pressure should be not so light so that it simply ‘rubs’ the work,
and not so heavy as to cause the blade to wander off line or ‘grab’ the work.
Fig. 14
Fig. 15
Summary of Contents for CBS7MB
Page 22: ...Spare Parts Diagram 22...
Page 24: ......