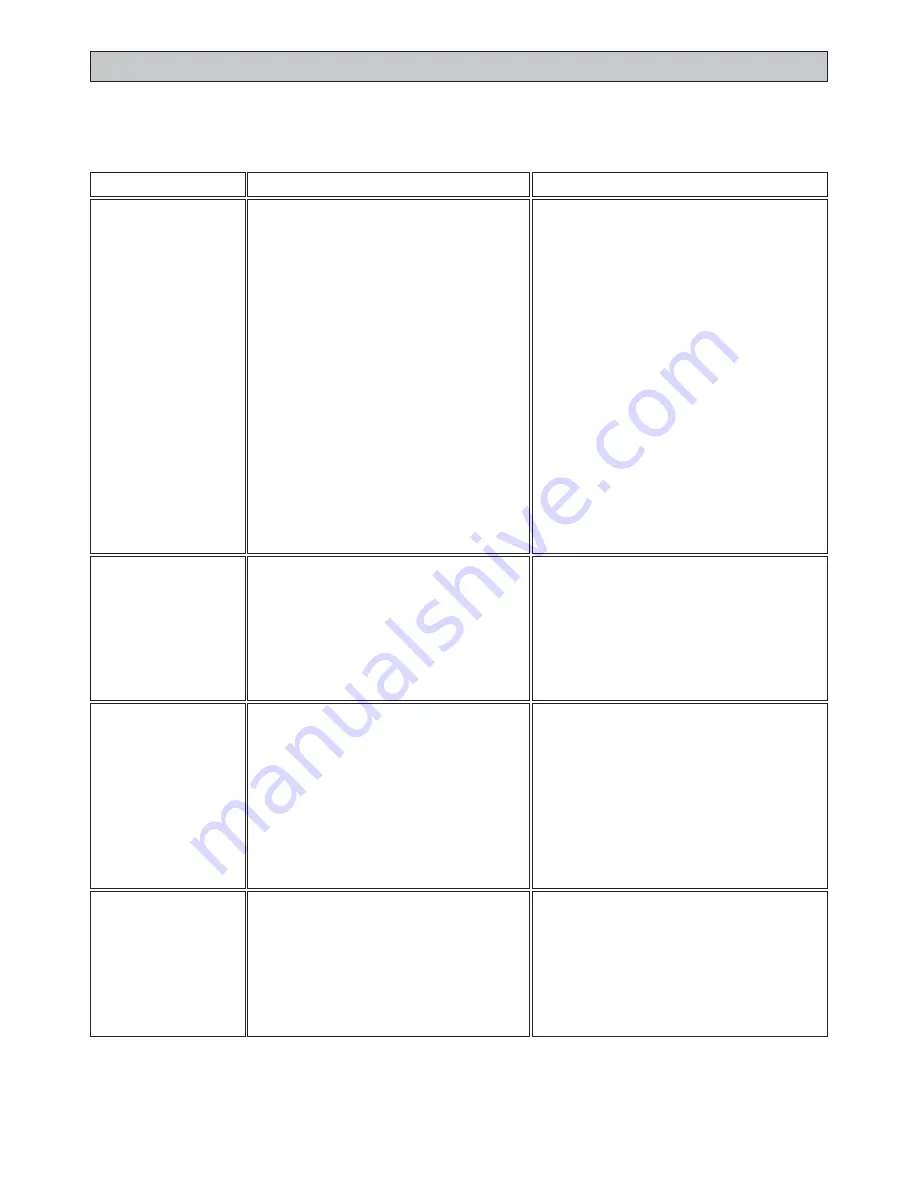
13
TROUBLE SHOOTING
ALWAYS disconnect your bandsaw from the power supply when troubleshooting, or carrying out
adjustments or maintenance.
Blades break
1. Faulty alignment (tracking)
2. Blade guides incorrectly adjusted.
3. Feeding the work too fast.
4. Forcing or twisting the blade
around a tight radius.
5. Blade too tight.
6. Dull teeth.
7. Blade is badly welded or brazed.
8. Wrong blade fitted
Blade runs off cut-
ting line
1. Blade Guides incorrectly adjusted
2. Blade tracking maladjusted
3. Blade tension too loose
4. Wrong blade fitted..too thin
1. Carry out tracking adjustments (p10)
2. Readjust Blade Guides
3. Lower the feed rate
4. For tight curves, make relief cuts,
fairly close together, at 90º to the
curve
5. Relieve blade tension
6. Renew blade
7. Renew blade
8. Fit only Quality blades supplied by
Clarke Int’l
9. ALWAYS switch machine OFF when
not in use
Motor does not run
1. Fuse blown
1. Renew fuse. If condition persists,
consult your Clarke dealer
2. Renew/Repair plug/Power
cable
3. Consult your Clarke dealer
2. Plug or Power cable defective
3. Motor defective
9. Blade left running when not in use.
Machine vibrates
1. Mountings loose
2. Table loose
3. Motor loose
4. Mounting platform is not robust
enough
1. Tighten Mountings
2. Secure table
3. Secure motor mountings
4. Ensure workbench or platform is
of strong enough construction to
fully support the machine
1. Readjust Blade Guides
2. Carry out tracking adjustment (p10)
3. Re-tension blade
4. Fit correct blade
Fault
Possible Cause
Remedy