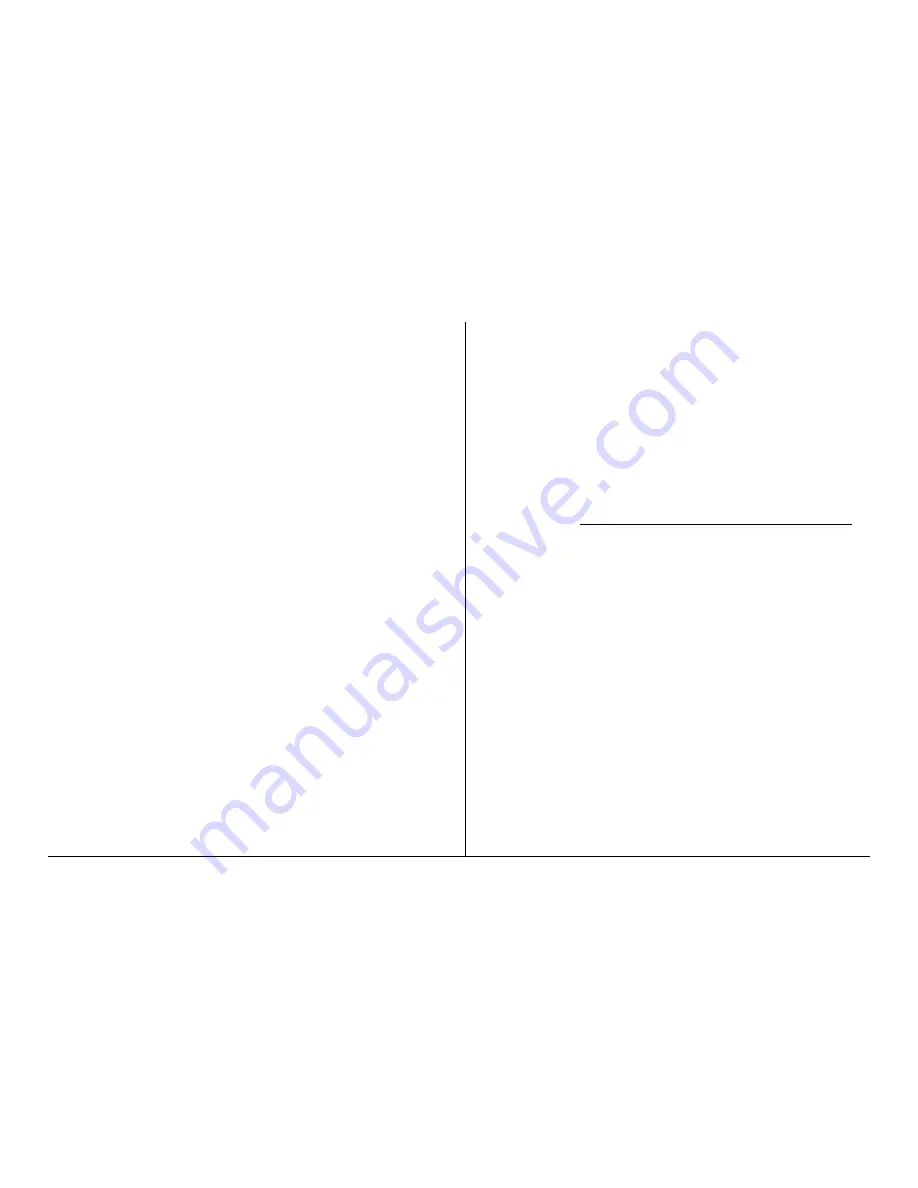
4. Trouble Shooting Guide
Problem
Probable Cause Solution
Excessive Blade 1 Material loose in vise
1 Clamp work securely
2 Teeth too course for
2 Check Machinist Handbook
material. for recommended
blade type.
3 Incorrect blade tension
3 Adjust to where blade just
does not slip on wheel.
4 Teeth in contact with work
4 Place blade in contact with
before saw is started.
work after motor is started.
5 Blade rubs on wheel flange.
5 Adjust wheel alignment
6 Misaligned guides
6 Adjust
7 Blade too thick for wheel
7 Use thinner blade
8 Cracking at weld
8 Make longer annealing cycle.
Premature
1 Teeth too course 1 Use finer tooth blade
Blade
2 Inadequate feed pressure 2 Decrease spring tension on
side of saw
3 Hard spots or scale in/on 3 Reduce speed, increase feed
material.
pressure (Scale). Increase feed
pressure (Hard Spots).
4 Work hardening of material 4 Increase feed pressure by
(especially stainless steel)
reducing spring tension.
5 Blade installed backwards 5 Remove blade, twist inside out
and reinstall blade.
6 Insufficient blade tension 6 Increase tension to proper level.
Bad Cuts
I Blade is too coarse 1 Replace with finer blade.
2 Work not square
2 Adjust vise to be square with
blade. Always clamp work
tightly in vise.
3 Feed pressure too great
3 Reduce pressure by increasing
spring tension side of saw.
Problem
Probable Cause Solution
Bad
5 Guide bearings not adjusted
5 Adjust guide bearings to .002
Cuts properly. greater than max. thickness,
including weld, of the saw.
6 Inadequate blade tension
6 Increase blade tension a little
at a time.
7 Blade guides spaced out too
7 Move guides as close to work as
much.
possible.
8 Dull Blade
8 Replace blade
9 Blade guide assembly loose
9 Tighten
10 Blade guide bearing
10 Tighten
assembly loose
11 Blade tracks too far away
11 Retract blade according to
from wheel flanges
operating instructions.
Blade is
1 Cut is binding blade 1 Decrease feed pressure
Twisting
2 Too much blade tension 2 Decrease blade tension
Unusual Wear
1 Blade guides worn 1 Replace
on Side/Back
2 Blade guide bearing
2 Tighten
of Blade
bracket is loose
Teeth Ripping 1 Tooth too coarse for work
1 Use finer tooth blade
from Blade 2 Too heavy feed; too slow
2 Increase feed pressure and/or
feed
speed
3 Vibrating work piece
3 Clamp work securely
4 Gullets loading
4 Use coarse tooth blade or
brush to remove chips.
Motor Running 1 Blade tension too high
1 Reduce tension on blade
Too Hot
2 Drive belt tension too high
2 Reduce tension on drive belt
3 Blade is too coarse for
3 Use finer blade
work (Pipes especially)
4 Blade is too fine for work
4 Use coarser blade
(Heavier, soft material)
5 Gears not aligned properly
5 Adjust gears so that worm is in
center of gear
6 Gears need lubrication
6 Check oil bath
7 Idler wheel needs
7 Oil bearing/shaft on idler
lubrication
wheel
-19-
-18-