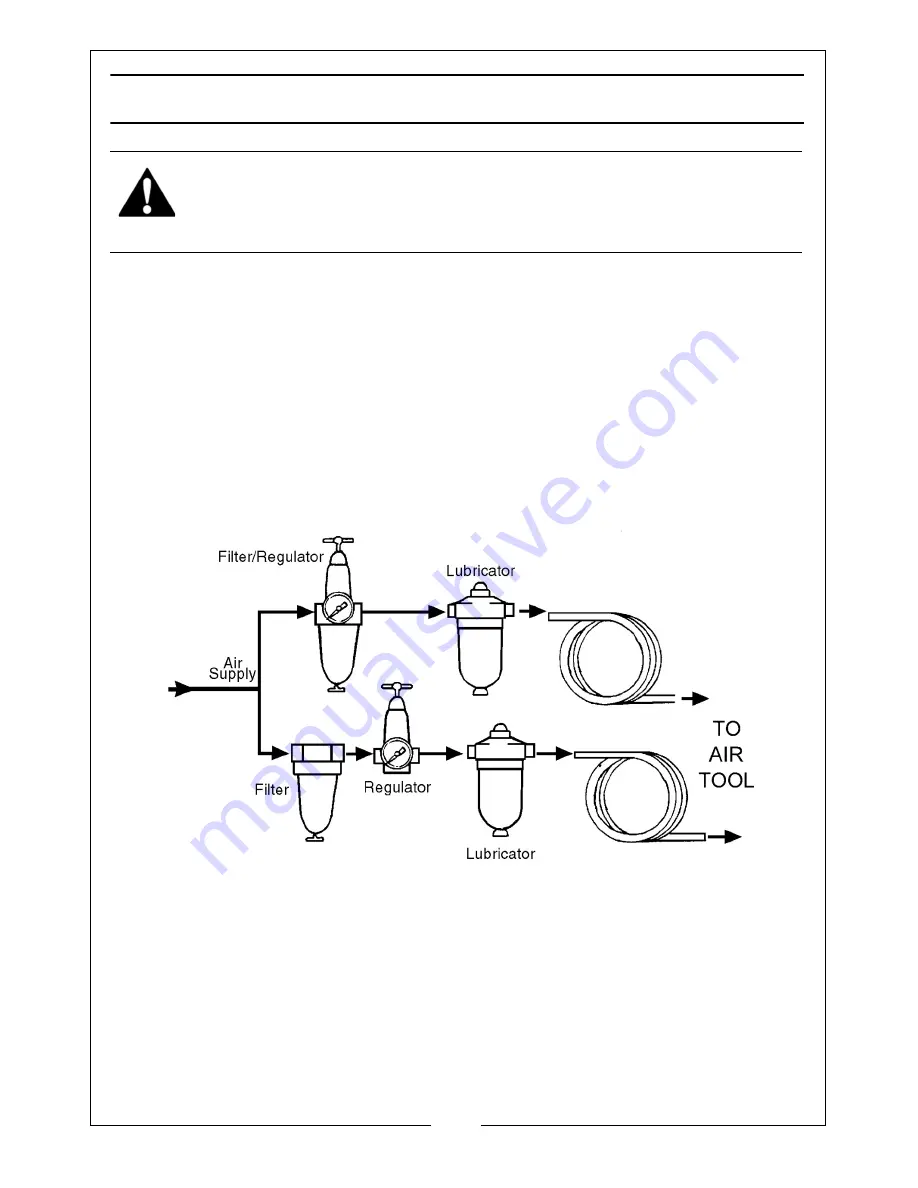
6
Parts & Service: 020 8988 7400 / E-mail: [email protected] or [email protected]
COMPRESSED AIR REQUIREMENTS
• Use only clean, dry, regulated compressed air as a power source.
• Air compressors used with the tool must comply with the appropriate
European Community Safety Directives.
• A build-up of moisture or oil in the air compressor will accelerate
wear and corrosion in the tool. ensure any moisture is drained from
the compressor daily and the inlet filter is kept clean.
• If an unusually long air hose is required, (over 8 metres), the line
pressure or the hose inside diameter may need to be increased.
• The air hose must be rated at least 150% of the maximum operating
pressure of the tool.
• A typical air line layout is shown above. If an automatic in-line filter/
regulator is used, it will keep the tool in good condition, but should
be regularly checked and topped up with oil. SAE 10 oil should be
used, and the lubricator adjusted to approx 2 drops per minute.
• Never exceed the maximum operating pressure for the tool. It is
recommended that air pressure to this tool does not exceed 90 psi
at the tool when running. Higher pressures and unclean air will
shorten the life of the tool due to faster wear and is a possible safety
hazard.
WARNING: COMPRESSED AIR CAN BE DANGEROUS. ENSURE THAT YOU
ARE FAMILIAR WITH ALL PRECAUTIONS RELATING TO THE USE OF
COMPRESSORS AND COMPRESSED AIR SUPPLY.
Summary of Contents for CAT130
Page 16: ......