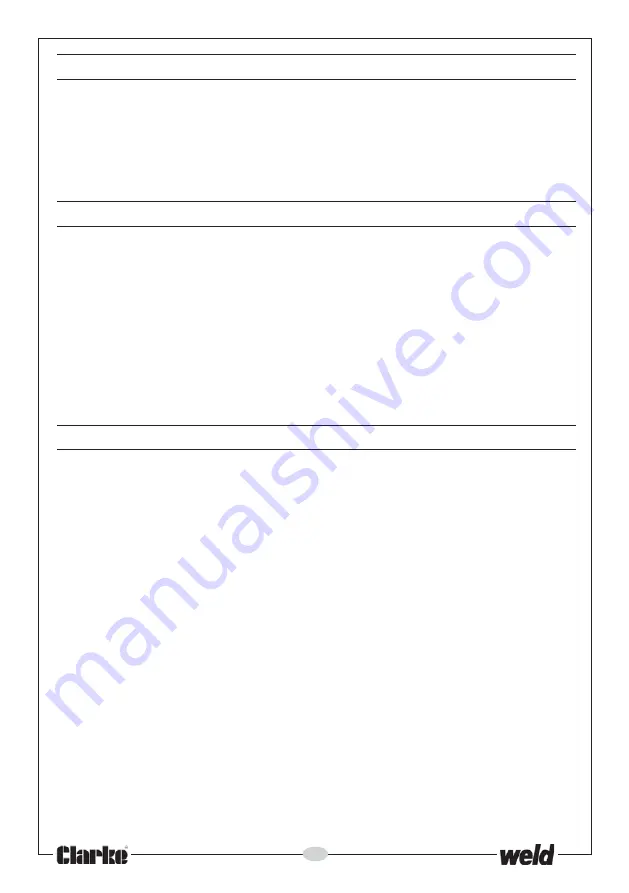
2
INTRODUCTION
Thank you for purchasing this CLARKE Arc/Tig welder.
Before attempting to use the machine, please read this manual thoroughly and follow the
instructions carefully. In doing so you will ensure the safety of yourself and that of others around
you, and you can look forward to the welder giving you long and satisfactory service.
GUARANTEE
This product is guaranteed against faulty manufacture for a period of 12 months from the date of
purchase. Please keep your receipt which will be required as proof of purchase.
This guarantee is invalid if the product is found to have been abused or tampered with in any
way, or not used for the purpose for which it was intended.
Faulty goods should be returned to their place of purchase, no product can be returned to us
without prior permission.
This guarantee does not effect your statutory rights.
TABLE OF CONTENTS
...................................................................................................... Page
List of Equipment ......................................................................... 3
Specifications ............................................................................... 3
Principles of Operation ................................................................. 4
General Safety Precautions ......................................................... 6
EMC in the Workplace ................................................................. 8
Safe Operation of Electric Arc Welders ...................................... 10
Preparation of the Welding Area ................................................. 14
Features of the ARC/TIG135 ....................................................... 15
The ARC/TIG135 Components .................................................... 17
Welding Techniques .................................................................. 18
Maintenance ................................................................................. 23
Fault Finding ................................................................................. 23
Parts Lists & Diagrams ................................................................ 24
Declarations of Conformity .......................................................... 27
Please note that the details and specifications contained herein, are correct at the time of going
to print. However, CLARKE International reserve the right to change specifications at any time
without prior notice. Always consult the machine’s data plate.
Summary of Contents for Arc/Tig135
Page 1: ...OPERATING MAINTENANCE INSTRUCTIONS Model No Arc Tig135 PART NO 6010790 0612 ARC TIG WELDER...
Page 24: ...24 PARTS DIAGRAM...
Page 26: ...26 WIRING DIAGRAM...
Page 28: ......