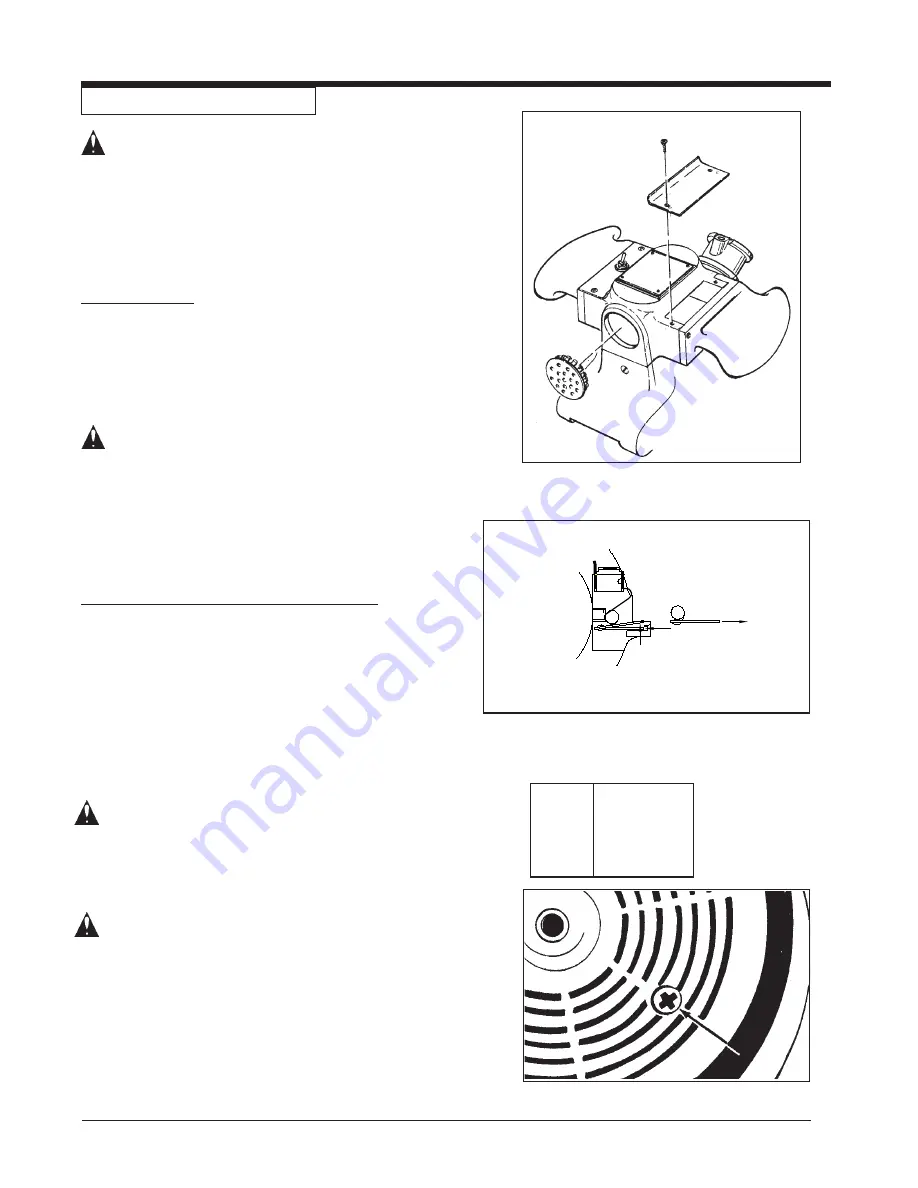
Page 10
Clarke
®
American Sanders
Super 7R Operator's Manual
MAINTENANCE
CAUTION:
Maintenance and repairs performed by
unauthorized personnel could result in
damage or injury. Maintenance and
repairs performed by unauthorized
personnel will void your warranty.
Failure to perform maintenance at
recommended intervals may void
warranty.
Carbon Brushes
Inspect all four brushes every 6 months or 250 hours.
Access to the brushes is gained through the front and
back motor vent plugs and under both motor covers (figure
6). Press tab on spring clip assembly in, rotate, then
remove (figure 7).Use needlenose pliers to disconnect the
shunt wire. If any brush has worn to 3/8" in length or
shorter, replace the entire set.
CAUTION:
Use only motor brush PN 40818A or
PN 40055A with shunt wire or motor
failure will occur.
When replacing the brushes make sure that the brush
seats against the commutator, the spring rest in the
recess of the brush, and the brush is free to travel. When
returning the switch cover, keep any wires clear of the
commutator and any pinch site.
To Change The Lubricant In The Gearbox
To change the lubricant in the gearbox, follow this proce-
dure:
1. Put the machine upside down on a bench.
2. Align one of the two holes in the rubber pad with one
of the three holes in the rotating wall guard.
3. Align both holes with one of the three screws in the
gear housing cover. Remove the screw from the gear
housing cover. (Figure 8)
4. Align the holes with each of the other two screws,
then remove screws.
CAUTION:
Make sure no dust enters the gear box.
Damage will occur to the gear box.
5. Remove the cover from the gear housing.
6. Remove the old lubricant from the gearbox.
7.Add six ounces of American SandersTechnology
lubricant to the gear box.
CAUTION:
To prevent damage to the motor, do not
add more than six ounces of lubricant to
the gearbox.
8. Using the three screws removed above, install the
cover on the gear housing.
9. Start the machine and let it run for 15 minutes. A
small amount of excess lubricant should flow out the
vent hole. If none appears it may be necessary to
add additional lubricant.
10. Wipe off excess lubricant and clear vent hole.
Figure 8
Qty
Part No.
1Qt.
16610A
1Gal.
16611A
Lubricants
Figure 6
Figure 7