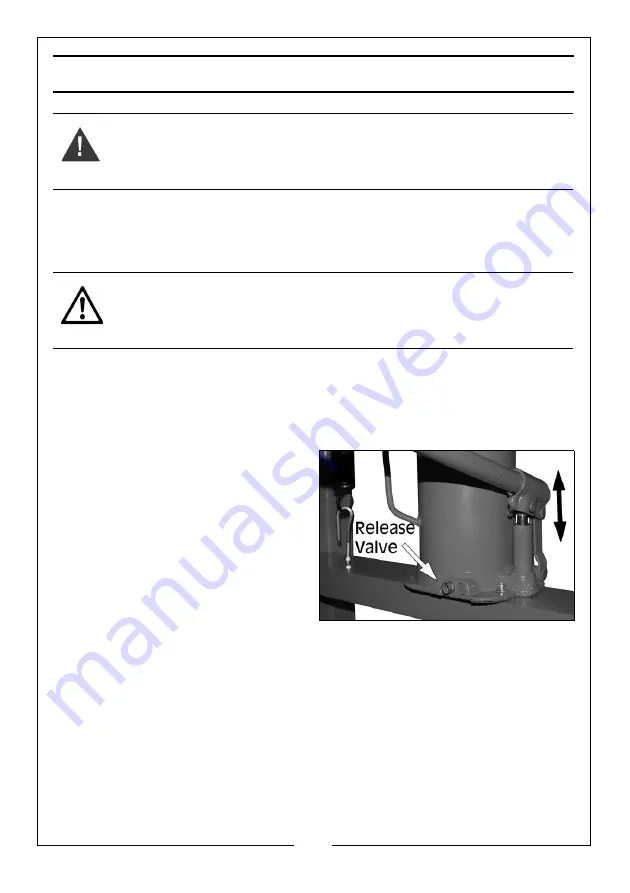
8
Parts & Service: 020 8988 7400 / E-mail: [email protected] or [email protected]
OPERATION
1. The press is now ready for use. Place the workpiece on the bed. It must be
completely stable and supported by packing or shims where required. A
pair of pressing plates are supplied, which lay flat on the bed. Place the
workpiece on these to give it stability.
NOTE:
Any packing pieces or shims used MUST be capable of
withstanding the pressure that will be brought to bear, and MUST
be of sufficient size with sufficient surface area, so as to avoid the
possibility of slipping or springing out. Mating surfaces MUST be
horizontal so that the force being exerted will NOT be at an angle.
2. Using the crimped end of the
handle, close the release valve by
turning it clockwise until tightly
closed.
3. Pump the handle to bring the ram
very lightly into contact with the
workpiece.
4. Position the workpiece so that the
desired point of contact is directly
beneath the centre of the ram.
5. When satisfied that the workpiece is correctly aligned and is completely
stable in that position, slowly pump the handle so that the ram begins to
exert pressure on the workpiece.
6. Continue to pump the handle and constantly monitor the process,
ensuring the ram and work remain completely in line and there is no risk of
slipping.
7. When the task is complete, turn the release valve anticlockwise in small
increments to release ram pressure and allow removal of the workpiece.
WARNING: FAILURE TO HEED THE WARNINGS ON PAGE 3 MAY RESULT IN
DAMAGE TO THE EQUIPMENT OR COMPONENT FAILURE RESULTING IN
PROPERTY DAMAGE, PERSONAL, OR EVEN INJURY.
NEVER USE EXTENSIONS TO THE RAM PUMPING HANDLE
CAUTION: DO NOT POINT LOAD THESE ACCESSORIES AS THEY ARE NOT
DESIGNED TO TAKE THE FULL FORCE OF THE RAM IN ONE SPOT. ENSURE
THEY ARE ADEQUATELY SUPPORTED.
Summary of Contents for 7614052
Page 16: ......