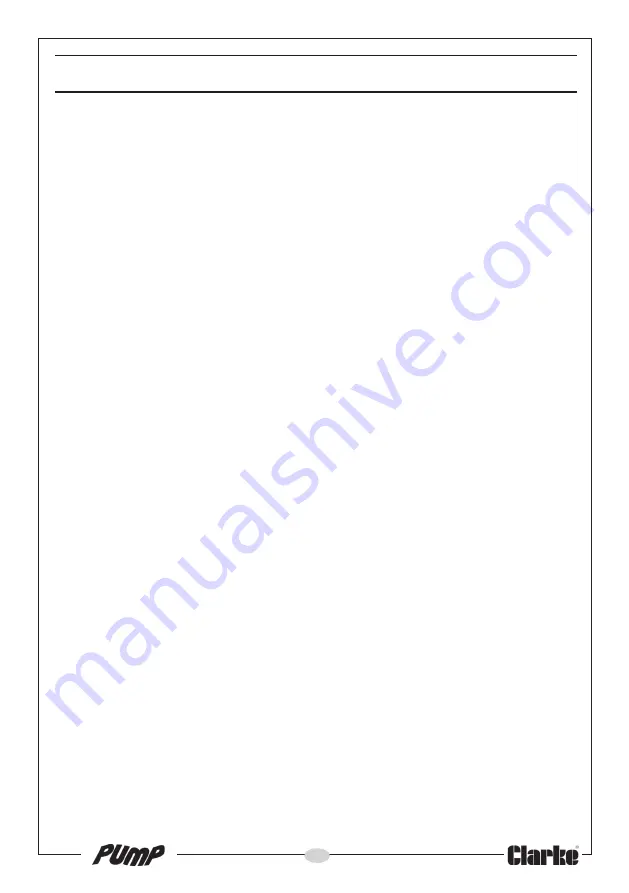
9
INSTALLATION
POSITIONING THE PUMP
1. Place the pump on a firm foundation and as near to the water source as
possible.
2. Ensure there is adequate drainage for the discharged water, and that
there is no danger of damage to property as a result of the pumping
operation.
CONNECTING THE HOSES
1. Connect the suction and discharge hoses to the pump housing using the
hose coupling adaptors, hose clamps and O-rings supplied to achieve an
air-tight seal. There must be no damage to the hoses which must be well
protected and supported.
NOTE:
Hoses or pipes should be supported independently and not carried by
the pump.
IMPORTANT:
An air leak in the suction line will inhibit priming, and reduce the
capacity of the pump.
2. Pay particular attention to the following:
a.
Always ensure the O-ring is placed between the hose
adaptor and pump casting.
b.
Always use a flexible hose at the pump body connection of at
least 1ft (300mm).
c.
Keep all pipes/hoses as short and straight as possible and
avoid sharp bends.
d.
Ensure there is adequate drainage for the discharged water.
e.
Ensure machine is on level ground or base to avoid spilling fuel.
f.
If a flexible hose must be laid across a roadway, protect it with
planking.
(Instantaneous shut off pressure, applied when a vehicle runs across an
unprotected hose, could cause “hydraulic shock”, which can damage the
pump and/or the hose).
3. If the discharge line runs vertically more than 30ft it is advisable to install a
check valve in the discharge line near the pump to stop destructive water
hammer when the pump is shut down. If a check valve is installed, it may
also be necessary to vent the top of the pump so that air can he expelled
during automatic re-priming. This air bleed may he accomplished by
providing a 1/4" line from the top of the pump back to the liquid source.
We will not assume any responsibility for damage to the pump if no check
valve is used in the discharge line.
Summary of Contents for 7140635
Page 1: ...OPERATING MAINTENANCE INSTRUCTIONS GC0410 PETROL DRIVEN WATER PUMP Model CU150 Part No 7140635...
Page 7: ...7 1 2 3 4 5 Fig 1 7 6 8 9 10 11 12 13 14 15 16 17 Fig 2...
Page 21: ...21...
Page 23: ...23...
Page 25: ...25 PARTS DIAGRAM PUMP...
Page 26: ...26 DECLARATION OF CONFORMITY...
Page 27: ...27 DECLARATION OF CONFORMITY...
Page 28: ......