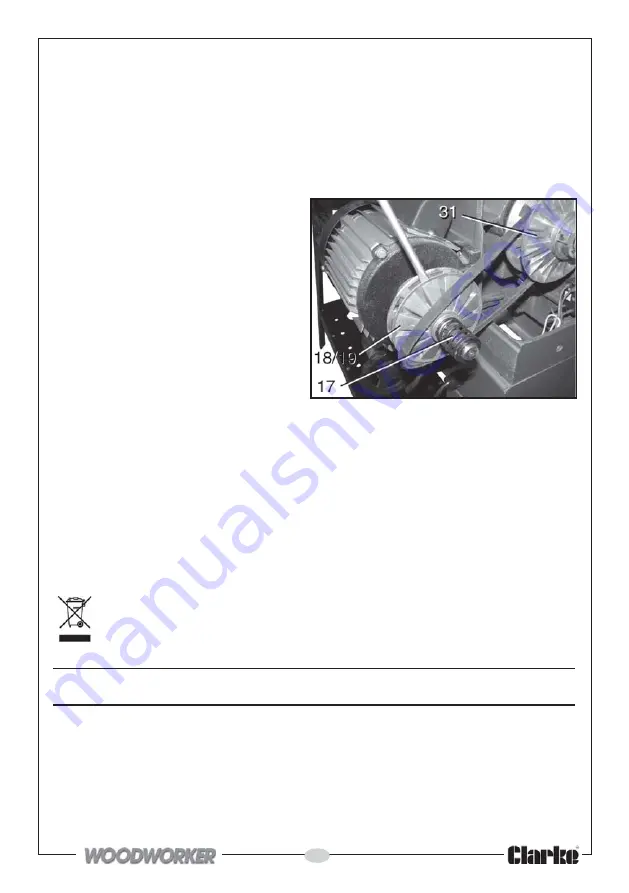
13
5. Periodically lubricate the tail-stock, copy stock and tool carrier screw
threads with engine oil such as SAE30 grade if they become stiff to use.
6. Lightly lubricate the tail-stock and tool-post locking handles with oil if they
become difficult to use.
•
The ball bearings in the headstock and tail-stock spindles and in the copy
live roller pin are greased and permanently sealed at the factory and
require no further lubrication.
REPLACING THE BELT
1. Undo the retaining screws and
remove the belt guard.
2. By pushing the speed control
lever, expand the two halves of
the driven pulley (31) allowing
the belt to adopt its smallest
diameter at this end.
3. Rotate the motor pulley (18/19)
to dismount the drive belt from it
and then lift it off the driven
pulley.
4. Replacement is a reverse of the removal procedure. A broad-bladed
screwdriver or similar will be useful to prize the two halves of the motor
pulley apart against the pressure of the spring (17). Ensure the left & right
halves of the drive pulley spring back to grip the belt and that the belt is in
tension.
In case of problems refer to TROUBLESHOOTING on page 14. If you are unable
to rectify any faults, please contact your local dealer or Clarke International
Service Department on 0208 988 7400 for assistance.
ENVIRONMENTAL PROTECTION
Do not dispose of this product or broken components with general
household waste. All tools, accessories and packaging should be
sorted, taken to a recycling centre and disposed of according to the
laws governing Waste Electrical and Electronic Equipment.
ACCESSORIES
The following range of accessories are also available from your Clarke dealer:
8-Piece Chisel Set
Part No: 6500649
4-Jaw Independent Lathe Chuck
Part No: 6500645
1/2” Cap. Tailstock Chuck
Part No: 6500643
Fig 6
Summary of Contents for 6500682
Page 19: ...19 DECLARATION OF CONFORMITY...
Page 20: ......