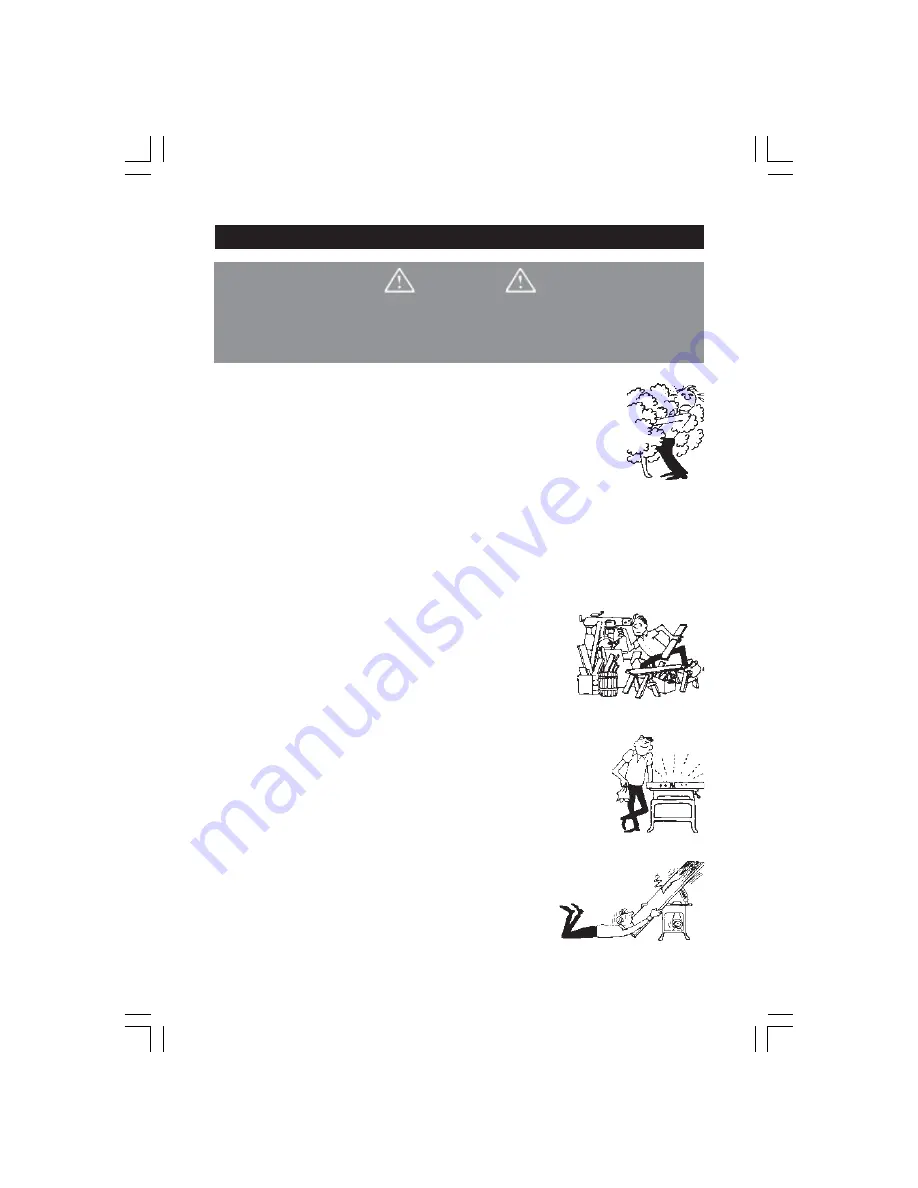
Safety Precautions
WARNING:
As with all machinery, there are certain hazards involved with their operation
and use. Exercising respect and caution will considerably lessen the risk of
personal injury. However, if normal safety precautions are overlooked or
ignored, personal injury to the operator or damage to property, may result.
1.
ALWAYS
Learn the machines applications, limitations and the
specific potential hazards peculiar to it. Read and become familiar
with the entire operating manual.
2.
ALWAYS
use a face or dust mask if operation is particularly dusty.
3.
ALWAYS
check for damage. Before using the machine, any
damaged part, should be checked to ensure that it will operate
properly and perform its intended function. Check for alignment
of moving parts, breakage of parts, mountings and any other
condition that may affect the machines operation. Any damage should be properly
repaired or the part replaced. If in doubt,
DO NOT
use the machine. Consult your
local dealer.
4.
ALWAYS
disconnect the machine from the power supply before servicing and when
changing accessories.
5.
ALWAYS
wear safety goggles, manufactured to the latest European Safety Standards.
Everyday eyeglasses do not have impact resistant lenses, they are not safety
glasses.
6.
ALWAYS
keep work area clean. Cluttered areas and
benches invite accidents.
7.
ALWAYS
ensure that adequate lighting is available. A
minimum intensity of 300 lux should be provided. Ensure
that lighting is placed so that you will not be working in
your own shadow.
8.
ALWAYS
keep children away. All visitors should be kept a safe distance from the
work area, especially whilst operating the machine.
9.
ALWAYS
maintain machine in top condition. Keep tools/machines
clean for the best and safest performance. Follow maintenance
instructions.
10.
ALWAYS
handle with extreme care do not carry the tool/machine
by its’ electric cable, or yank the cable to disconnect it from the
power supply.
11.
ALWAYS
ensure the switch is off before plugging in to mains. Avoid
accidental starting.
12.
ALWAYS
concentrate on the job in hand, no matter how
trivial it may seem. Be aware that accidents are caused
by carelessness due to familiarity.
13.
ALWAYS
keep your proper footing and balance at all
times - don’t overreach. For best footing, wear rubber
soled footwear. keep floor clear of oil, scrap wood, etc.
4
Summary of Contents for 6500403
Page 13: ...Parts Diagram 13...