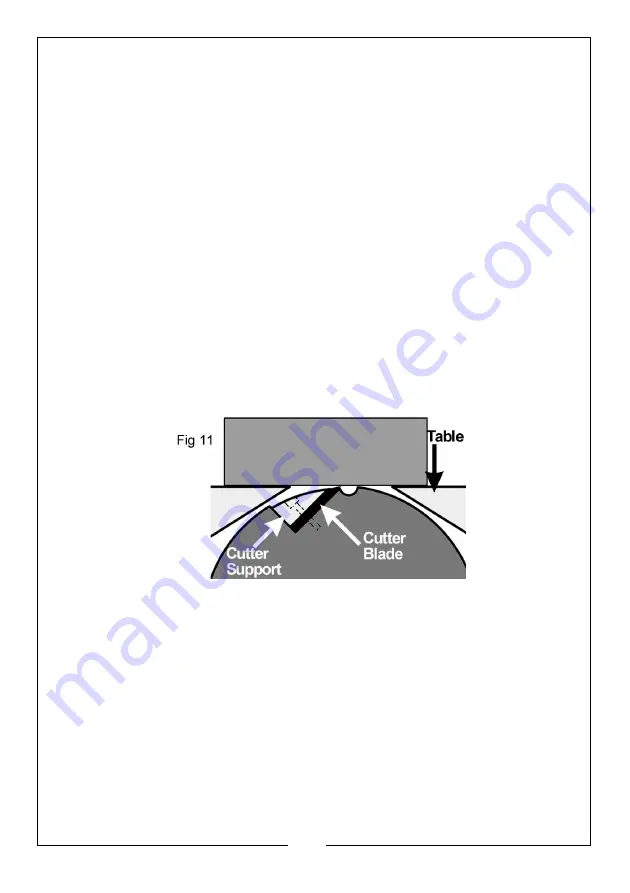
13
Parts & Service: 020 8988 7400 / E-mail: [email protected] or [email protected]
First, ensure the machine is switched OFF and isolated from the mains supply.
1. Turn the cutter height adjuster so that it registers zero. i.e. turn the knob
clockwise so that the depth of cut, registered on the scale, is zero.
2. Remove the angle fence.
3. Raise the Cutter Guard arm.
4. Turn the cutter block to reveal the four hex. socket head screws securing
the cutter blade, then carefully remove them.
5. Turn the cutter block by 180 degrees and repeat the process.
NOTE:
ALWAYS hone/replace cutter blades as a pair.
6. Replace in reverse order, and, using a straight edge, ensure the cutting
edges are level and in line with the table when they are at 12 o’clock - see
Fig.10. Tighten the securing screws taking care not to over-tighten or
damage the hex. sockets.
NOTE:
It is recommended that sharpening is done professionally, using a
jig, as blades must be sharpened as a pair to ensure they are
correctly balanced. This avoids the possibility of vibration due to
imbalanced cutters rotating at speed.
PERIODICALLY
• Wipe both the infeed and outfeed rollers with a damp cloth to remove
all traces of contaminants.
• Wax the thicknesser table frequently to ensure a smooth and reliable
feed.
• Inspect the kickback pawls before each operation to ensure they are
intact and working properly. They should hang normally and loosely.
• Remove the front cover - 3 dome head nuts, and lightly oil all pivots,
linkages and bearings with good quality machine oil. Ensure the
enclosure and all components are perfectly clean before replacing the
cover.
Summary of Contents for 6462135
Page 20: ......