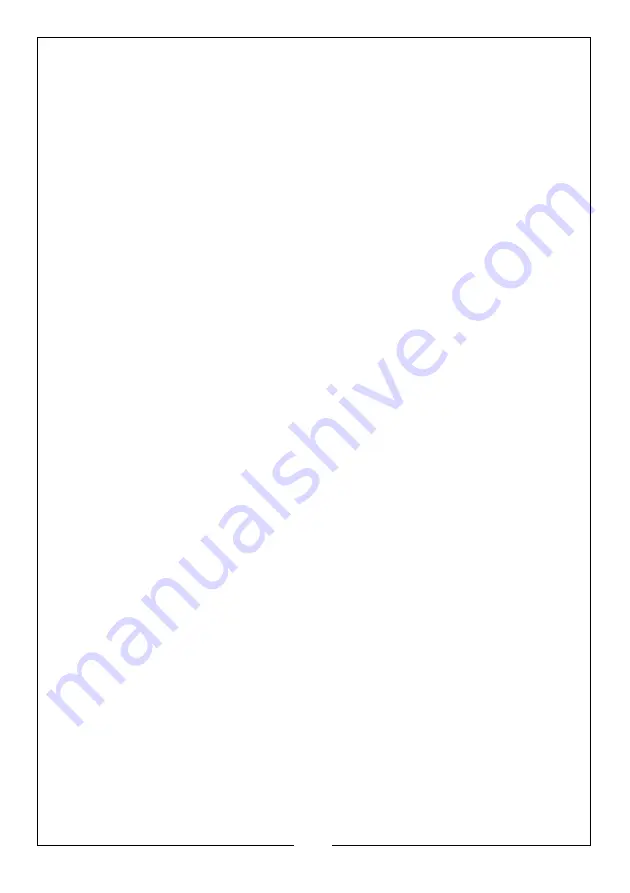
6
Parts & Service: 020 8988 7400 / E-mail: [email protected] or [email protected]
intensity gas-shielded arc) can cause a retinal burn thatmay leave a
permanent dark area in the field of vision. Before welding whilst wearing
contact lenses, seek advice from your optician.
PROTECTION OF NEARBY PERSONNEL
For production welding, a separate, well vented room or enclosed bay is best.
In open areas,surround the operation with low reflective, non- combustible
screens or panels. Allow for free air circulation, particularly at floor level.
Provide face shields for all persons who will be looking directly at the weld.
Others working in the area should wear flash goggles. Before starting to weld,
make sure that screen or bay doors are closed.
B) TOXIC FUME PREVENTION
Comply with all precautions in 1B.
C) FIRE AND EXPLOSION PREVENTION
Do not overload arc welding equipment. It may overheat cables and cause a
fire. Loose cable connections may overheat or flash and cause a fire. Never
strike an arc on a cylinder or other pressure vessel. It creates a brittle area that
can cause a violent rupture or lead to such a rupture later under rough
handling.
D) SHOCK PREVENTION
Exposed live conductors or other bare metal in the welding circuit, or in
unearthed, electrically-LIVE equipment can fatally shock a person whose
body becomes a conductor. DO NOT STAND, SIT, LIE, LEAN ON, OR TOUCH a
wet surface when welding, without suitable protection.
PROTECTION FOR WEARERS OF ELECTRONIC LIFE SUPPORT DEVICES
(PACEMAKERS).
Magnetic fields from high currents can affect pacemaker operation. Persons
wearing pacemakers should consult with their doctor before going near arc
welding or spot welding operations.
E) PROTECTION AGAINST SHOCK
Keep body and clothing dry. Never work in damp area without adequate
insulation against electric shock. Stay on a dry duckboard or rubber mat when
dampness or sweat can not be avoided. Sweat, sea water, or moisture
between body and an electrically LIVE part - or earthed metal - reduces the
body surface electrical resistance, enabling dangerous and possibly lethal
currents to flow through the body.
1) EARTHING THE EQUIPMENT
When arc welding equipment is earthed according to the National Electrical
Code, and the workpiece is earthed, a voltage may exist between the
electrode and any conducting object.
Summary of Contents for 6014011
Page 32: ......