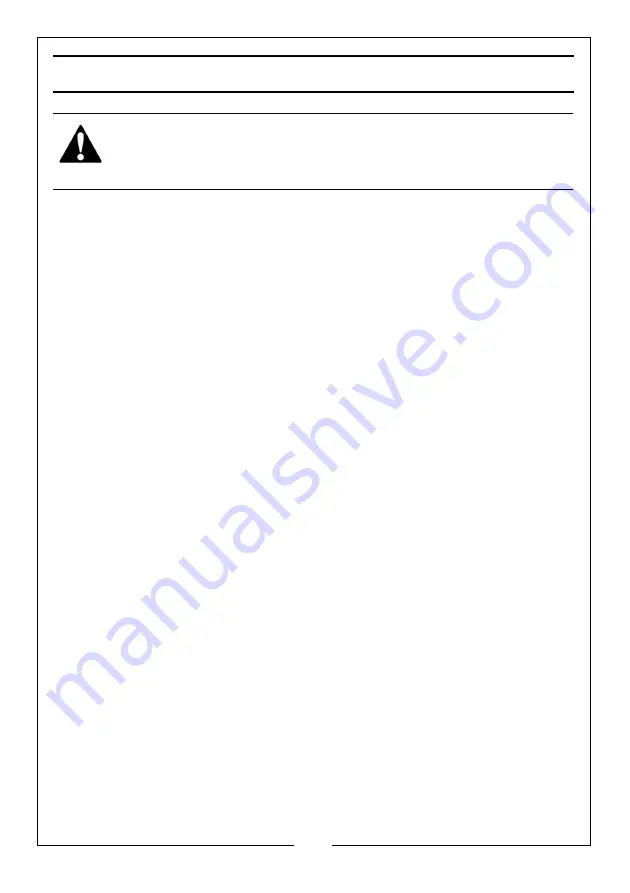
10
Parts & Service: 020 8988 7400 / E-mail: [email protected] or [email protected]
MAINTENANCE
Please note that factors other than the tool may effect its operation and
efficiency such as reduced compressor output, excessive drain on the airline,
moisture or restrictions in the air-line, or the use of connectors of improper size
or poor condition which will reduce air supply.
DAILY
1. Before use, drain water from the air-line and compressor.
2. Lubricate the air tool daily for optimum performance, using a high quality
airline oil either via a lubricator in the air supply system or by placing a few
drops into the air inlet immediately before use. This should be carried out
regardless of whether or not an in-line lubricator is used.
CLEANING & OVERHAUL
1. Keep the tool clean and free from debris.
2. Grit or gum deposits in the mechanism may eventually reduce efficiency.
This condition can be corrected by cleaning the air inlet strainer and
flushing out the tool with gum solvent oil or an equal mixture of SAE No10 oil
and paraffin.
3. Failing this, the tool should be disassembled, thoroughly cleaned, dried
and reassembled. You may prefer to take the tool to your CLARKE dealer if
internal maintenance is required.
4. If the tool becomes sluggish and the air supply is of good quality, it may be
necessary to replace worn or damaged parts. You may prefer to take the
tool to your Clarke dealer if internal maintenance is required.
5. Replacement needles can be fitted if required as described on page 7.
STORAGE
If the tool is to be stored, or is idle for longer than 24 hours, run a few drops of
Clarke air-line oil into the air inlet and depress the trigger in order to lubricate
the internal parts.
When not in use, the tool should be disconnected from the air supply and
stored in a dry place out of the reach of children. Avoid storing in a damp
environment or where the temperature is below 0
o
C.
WARNING: MAKE SURE THAT THE AIR TOOL IS DISCONNECTED FROM THE
AIR SUPPLY BEFORE STARTING ANY CLEANING OR MAINTENANCE
PROCEDURES.
Summary of Contents for 3120178
Page 16: ......