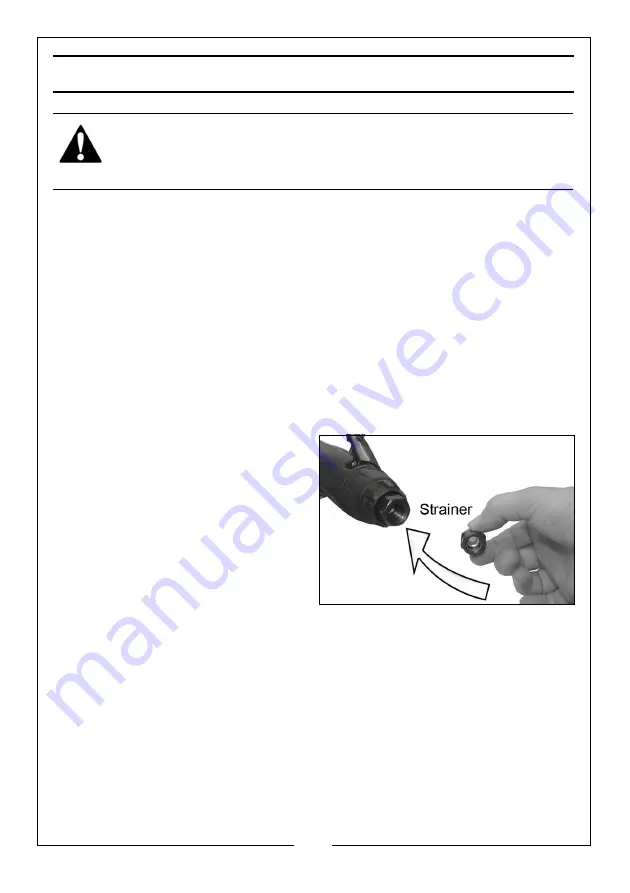
10
Parts & Service: 020 8988 7400 / E-mail: [email protected] or [email protected]
MAINTENANCE
DAILY
1. Before use, drain water from the air tank, air line and compressor.
2. Pour a few drops of CLARKE airline oil, into the air inlet. This should be
carried out regardless of whether or not an in-line mini oiler is used. If an in-
line mini oiler is not used, this procedure should be repeated after every
two to three hours of use.
WEEKLY
1. Wash the bonnets after each use by hand and use mild soap with water.
Hang them up to dry.
• Store them flat and allow them to regain shape.
2. Check the air inlet strainer for
blockage and clean if necessary.
CLEANING
1. Keep the body of the tool clean
and free from debris.
2. Grit or gum deposits inside the tool
may also reduce its efficiency. This
condition can be corrected by
cleaning out the air strainer and
flushing out the tool with gum solvent or oil, or failing this, the motor may
require dismantling. This is better left to your Clarke dealer.
WARNING: MAKE SURE THAT THE AIR TOOL IS DISCONNECTED FROM THE
AIR SUPPLY BEFORE STARTING ANY CLEANING OR MAINTENANCE
PROCEDURES.