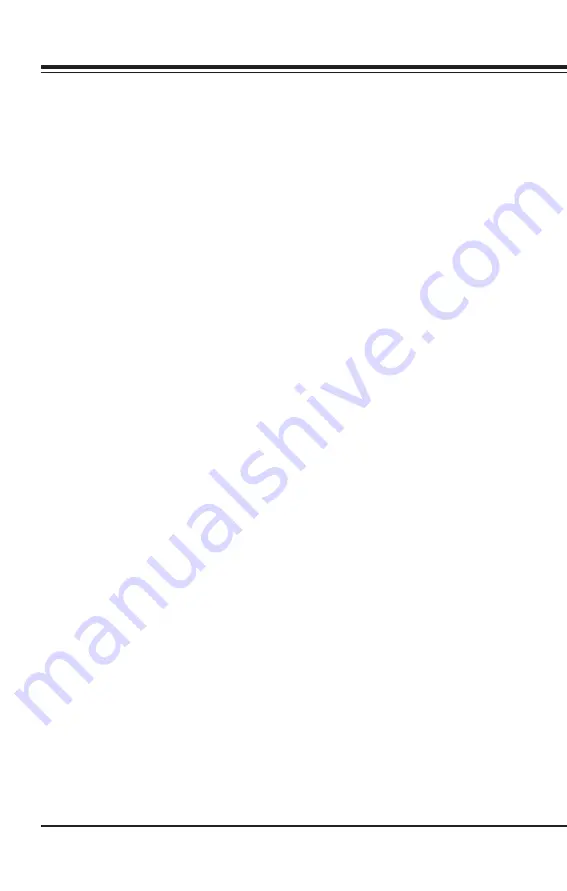
Planned Maintenance and Lubrication
6.2
Daily Inspection Points
The following should be done at the start of every shift:
• Check truck for obvious damage and leaks.
• Check / clean battery terminals.
• Check battery electrolyte level and specific gravity (except on AGM
type batteries).
• Check capacity plate, warning plates & decals.
• Check condition of tires and wheels and remove embedded objects.
• Check drive wheel nut.
• Check hour meter and battery discharge indicator.
• Check brake operation.
• Check horn operation.
• Check emergency reversal switch operation.
• Check directional and speed control operation.
• Check lift and lower operation.
• Check emergency disconnect switch.
Typical Operating Conditions
Time intervals between maintenance are largely determined by op-
erating conditions. The intervals specified in the following table are
for normal operation. For more severe operation, the maintenance
intervals should be shortened accordingly. Contact you CLARK dealer
for recommendations.
Normal Operation:
Basically, eight hour material handling in clean buildings with smooth
clean and level floors.
Severe Operation:
Prolonged operating hours or constant usage, with ramps and/or bumpy
floors.
Extreme Operation:
• Sandy or dusty locations.
• High temperature locations.
• Sudden temperature changes such as refrigeration facilities.
Summary of Contents for WSTX22
Page 6: ...iv...
Page 30: ...2 8...
Page 44: ...4 6 Operator Maintenance and Care...
Page 60: ...5 16...
Page 74: ...Planned Maintenance and Lubrication 6 14...
Page 76: ...7 2...
Page 78: ...8 2...