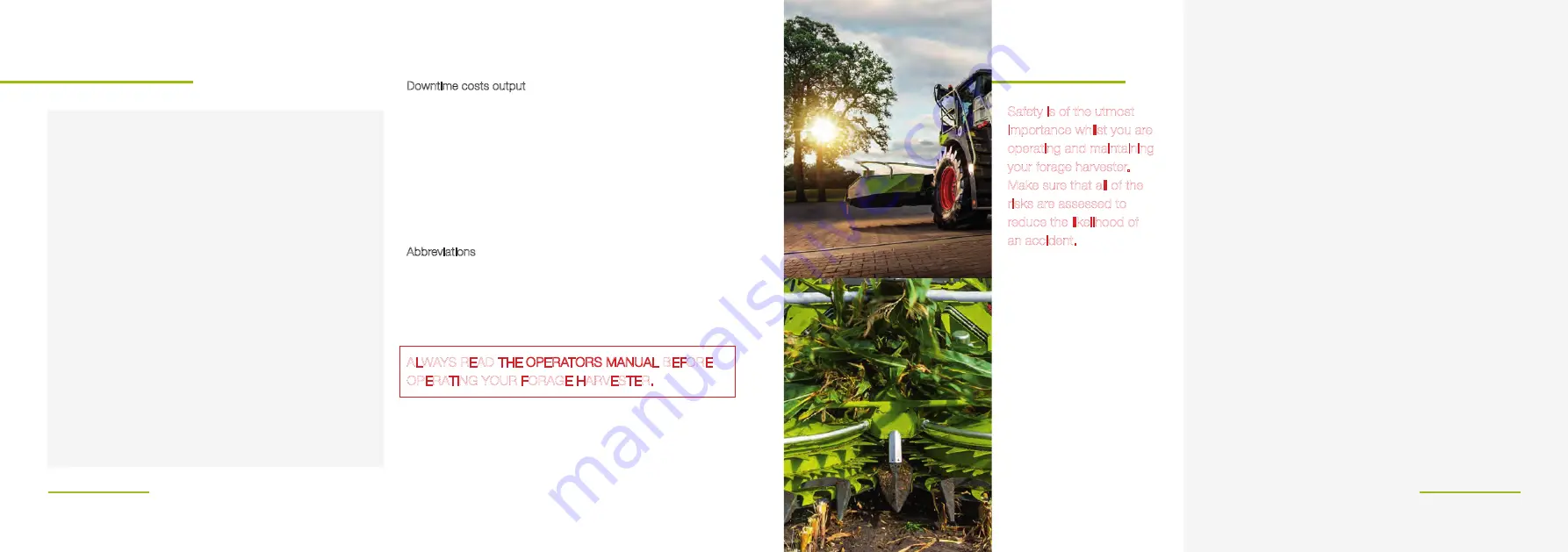
03
04
Introduction
This quick reference guide has
been produced to aid operator’s with
familiarisation and settings of CLAAS JAGUAR
forage harvesters.
CLAAS forage harvesters are designed for output
and efficiency but this can only be achieved
with correct operation and maintenance of the
machine.
This guide is not designed to replace
the Operator’s Manual but purely as
a reference document.
More in depth information is available
in the Operators Manual.
Downtime costs output
To get the most from the machine, the wheels must be turning.
In order to keep downtime to a minimum, it’s vital that routine
maintenance is not neglected.
As well as servicing the machine according to the operator’s
manual, a good check of the machine is essential. It is false
economy to put off the replacement of worn parts until they
break.
Abbreviations
Throughout this guide the following abbreviations are used:
‘LHS’ and ‘RHS’ refer to the Left Hand Side and Right Hand
Side of the machine respectively, taken from the rear of the
machine facing in the direction of travel.
• Make sure you are familiar with the controls and operation
of the machine and have read the Operator’s Manual.
• The forage harvester has many moving parts, guards are
designed to keep you safe, please ensure that all guards are
kept in place and in good condition when operating
the machine.
• When doing any maintenance work or making
adjustments outside of the machine make sure that the
engine is switched off and the battery isolator key is
removed.
• Some of the maintenance has to be carried out at height,
please asses the risks that this poses and ensure that the
task is carried out safely.
• When operating the machine be aware of the presence
of people particularly in farmyards, always get someone to
help you when reversing in confined areas.
• Be aware of the size of your machine, particularly the
height, you may be at risk from contact with overhead
power lines and overhead obstructions particularly but not
exclusively when the spout is in the working position and if
extra aerials have been fitted to your machine.
ALWAYS READ THE OPERATORS MANUAL BEFORE
OPERATING YOUR FORAGE HARVESTER.
The information is therefore not complete for the purpose of
working on the machine. This document does not replace the
relevant operators manual and repair documentation! Subject to
changes due to continued technical developments.
Safety is of the utmost
importance whilst you are
operating and maintaining
your forage harvester.
Make sure that all of the
risks are assessed to
reduce the likelihood of
an accident.
For more in depth safety
information please consult
your operators manual.
Always read the Operator’s
Manual before using any new
machine.
Safety
Summary of Contents for JAGUAR 830
Page 1: ...JAGUAR 830 880 500 Information and Basic Field Settings...
Page 12: ......
Page 27: ......
Page 29: ...Notes...
Page 30: ...Notes Notes...
Page 31: ...Jaguar 830 880 500 Information and Basic Field Settings www claas co uk...