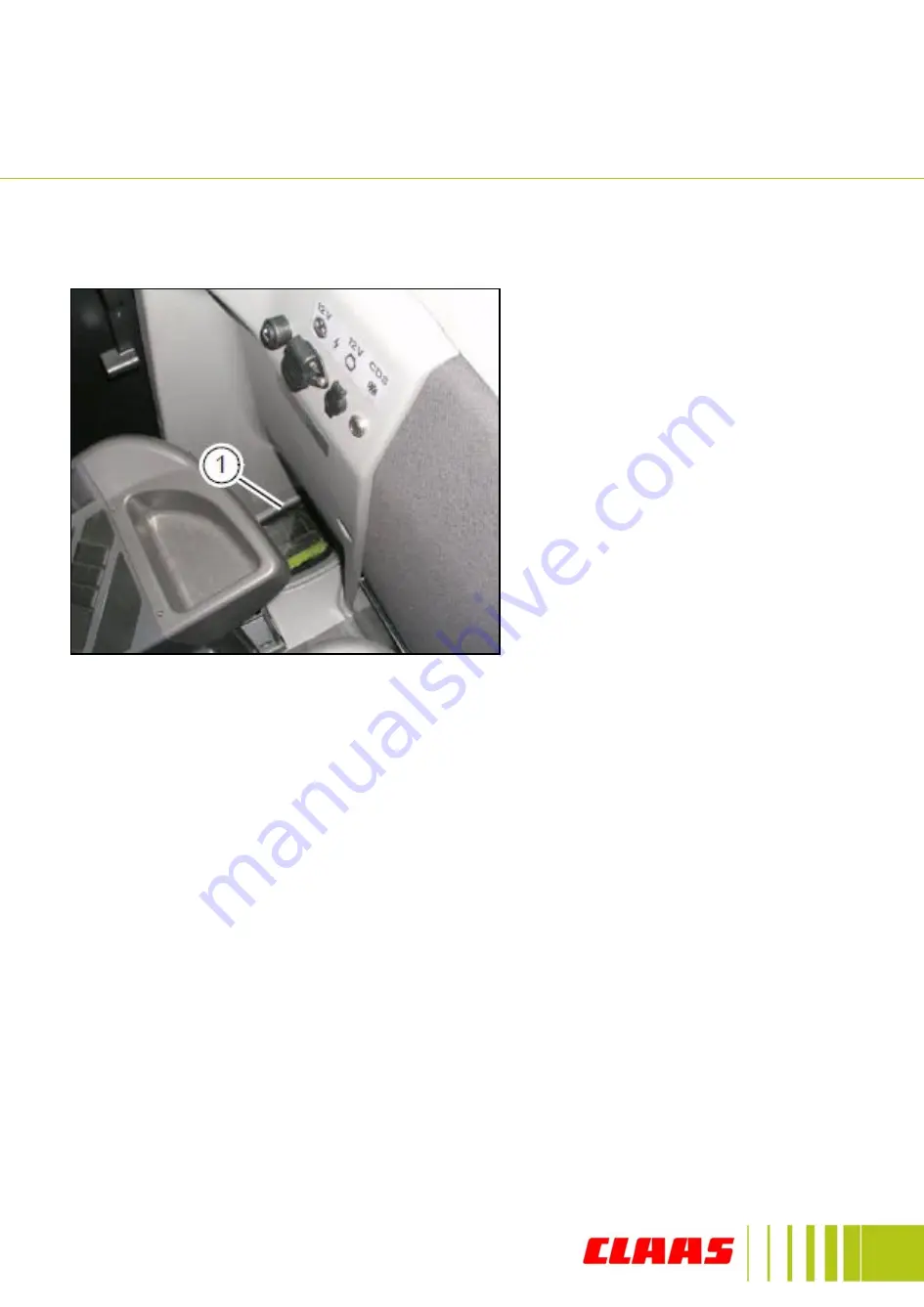
24
Returns
The returns should be monitored
regularly both in terms of volume
and composition. By looking
through the window (1) on the
lower RHS of the drivers seat, the
returns can be seen. The centre
tube of the auger should always
be visible.
If too much clean grain is present,
open the bottom sieve one step at
a time.
If too much chaff is present reduce
threshing.
If un-threshed heads are present
increase threshing.
In crops such as oilseed rape
where excessive trash is a
problem, it may be beneficial to
close the back section of the top
sieve to reduce re-circulation
through the returns.
Cleaning
Summary of Contents for AVERO
Page 1: ...Information and Basic Field Settings for AVEROVERSION 14...
Page 14: ...13 Notes...
Page 15: ...14 Notes...
Page 26: ...25 Settings aid...
Page 27: ...26...
Page 34: ...33 Notes...
Page 35: ...34 Notes...