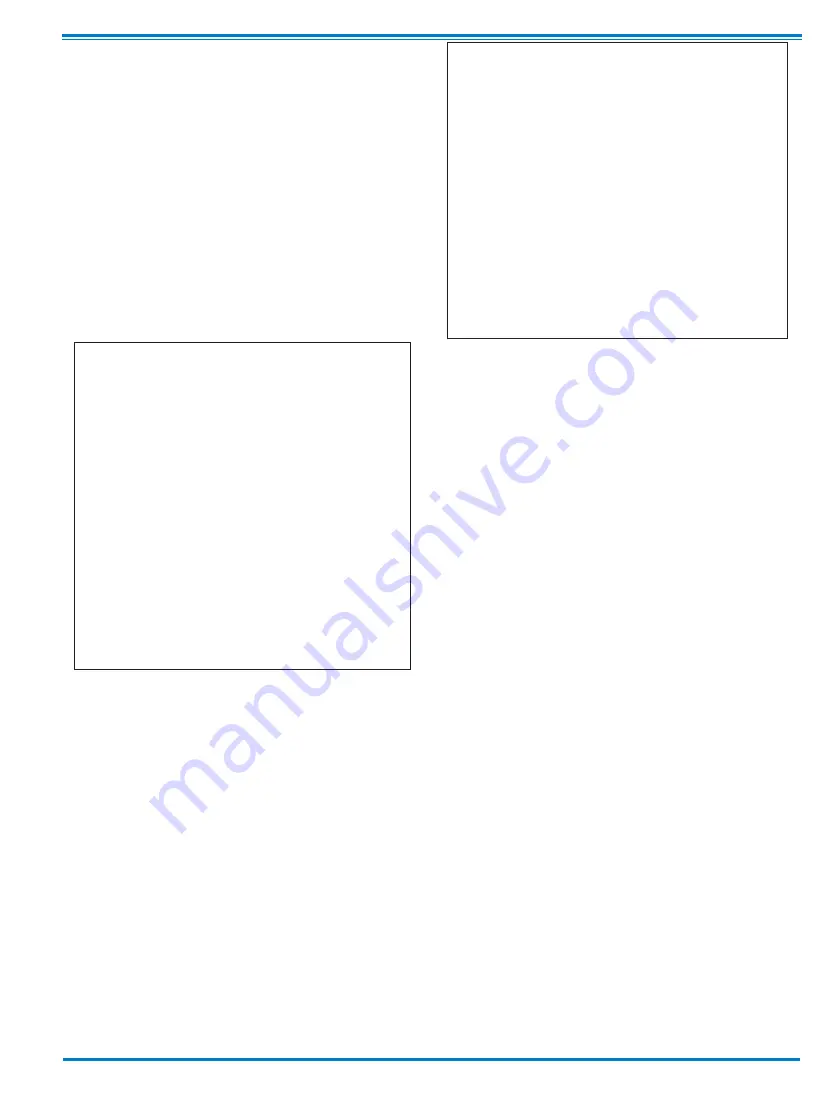
Diaphragm Check (#1 )
1.
Shut off pressure to the Hytrol Valve by slowly closing upstream
and downstream isolation valves.
SEE CAUTION
.
2.
Disconnect or close all pilot control lines to the valve cover and
leave only one fitting in highest point of cover open to atmosphere.
3.
With the cover vented to atmosphere, slowly open upstream
isolation valve to allow some pressure into the Hytrol Valve body.
Observe the open cover tapping for signs of continuous flow. It is
not necessary to fully open isolating valve. Volume in cover cham-
ber capacity chart will be displaced as valve moves to open posi-
tion. Allow sufficient time for diaphragm assembly to shift posi-
tions. If there is no continuous flow, you can be quite certain the
diaphragm is sound and the diaphragm assembly is tight. If the
fluid appears to flow continuously this is a good reason to believe
the diaphragm is either damaged or it is loose on the stem. In
either case, this is sufficient cause to remove the valve cover and
investigate the leakage. (See “Maintenance” Section for procedure.)
Freedom of Movement Check (#2)
4.
Determining the Hytrol Valve’s freedom of movement can be
done by one of two methods.
5.
For most valves it can be done after completing Diaphragm
Check (Steps 1, 2, and 3).
SEE CAUTION
. At the end of step 3
the valve should be fully open.
6.
If the valve has a Cla-Val X101 Position Indicator, observe the
indicator to see that the valve opens wide. Mark the point of max-
imum opening.
7
. Re-connect enough of the control system to permit the appli-
cation of inlet pressure to the cover. Open pilot system cock so
pressure flows from the inlet into the cover.
8
. While pressure is building up in the cover, the valve should
close smoothly. There is a hesitation in every Hytrol Valve closure,
which can be mistaken for a mechanical bind. The stem will
appear to stop moving very briefly before going to the closed posi-
tion. This slight pause is caused by the diaphragm flexing at a
particular point in the valve’s travel and is not caused by a
mechanical bind.
9.
When closed, a mark should be made on the X101 Valve posi-
tion indicator corresponding to the “closed” position. The distance
between the two marks should be approximately the stem travel
shown in chart.
10.
If the stroke is different than that shown in stem travel chart
this is a good reason to believe something is mechanically restrict-
ing the stroke of the valve at one end of its travel. If the flow does
not stop through the valve when in the indicated “closed” position,
the obstruction probably is between the disc and the seat. If the
flow does stop, then the obstruction is more likely in the cover. In
either case, the cover must be removed, and the obstruction locat-
ed and removed. The stem should also be checked for scale build-
up. (See “Maintenance, section for procedure.)
11.
For valves 6” and smaller, the Hytrol Valve’s freedom of move-
ment check can also be done after all pressure is removed from
the valve.
SEE CAUTION
. After closing inlet and outlet isolation
valves and bleeding pressure from the valve, check that the cover
chamber and the body are temporarily vented to atmosphere.
Insert fabricated tool into threaded hole in top of valve stem, and
lift the diaphragm assembly manually. Note any roughness. The
diaphragm assembly should move smoothly throughout entire
valve stroke. The tool is fabricated from rod that is threaded on
one end to fit valve stem and has a “T” bar handle of some kind
on the other end for easy gripping. (See chart in Step 4 of
“Disassembly” Section.)
12.
Place marks on this diaphragm assembly lifting tool when the
valve is closed and when manually positioned open. The distance
between the two marks should be approximately the stem travel
shown in stem travel chart. If the stroke is different than that
shown, there is a good reason to believe something is mechani-
cally restricting the stroke of the valve. The cover must be
removed, and the obstruction located and removed. The stem
should also be checked for scale build-up. (See “Maintenance”
Section for procedure.)
Tight Sealing Check (#3)
13
. Test for seat leakage after completing checks #1 & #2 (Steps
1 to 12).
SEE CAUTION.
Close the isolation valve downstream of
the Hytrol Valve. Apply inlet pressure to the cover of the valve, wait
until it closes. Install a pressure gauge between the two closed
valves using one of the two ports in the outlet side of the Hytrol.
Watch the pressure gauge. If the pressure begins to climb, then
either the downstream isolation valve is permitting pressure to
creep back, or the Hytrol is allowing pressure to go through it.
Usually the pressure at the Hytrol inlet will be higher than on the
isolation valve discharge, so if the pressure goes up to the inlet
pressure, you can be sure the Hytrol is leaking. Install another
gauge downstream of isolating valve. If the pressure between the
valves only goes up to the pressure on the isolation valve
discharge, the Hytrol Valve is holding tight, and it was just the iso-
lation valve leaking.
STEM TRAVEL
(Fully Open to Fully Closed)
Valve Size (inches)
Travel (inches)
Inches
MM
Inches
MM
1 1/4
32
0.4
10
1 1/2
40
0.4
10
2
50
0.6
15
2 1/2
65
0.7
18
3
80
0.8
20
4
100
1.1
28
6
150
1.7
43
8
200
2.3
58
10
250
2.8
71
12
300
3.4
86
14
350
4.0
100
16
400
4.5
114
20
500
5.6
143
24
600
6.7
165
30
800
7.5
190
36
900
8.5
216
COVER CHAMBER CAPACITY
(Liquid Volume displaced when valve opens)
Valve size (inches)
Displacement
Gallons
Liters
1 1/4
.020
.07
1 1/2
.020
.07
2
.032
.12
2 1/2
.043
.16
3
.080
.30
4
.169
.64
6
.531
2.0
8
1.26
4.8
10
2.51
9.5
12
4.00
15.1
14
6.50
24.6
16
9.57
36.2
20
12.00
45.4
24
29.00
109.8
30
42.00
197.0
36
90.00
340.0
3