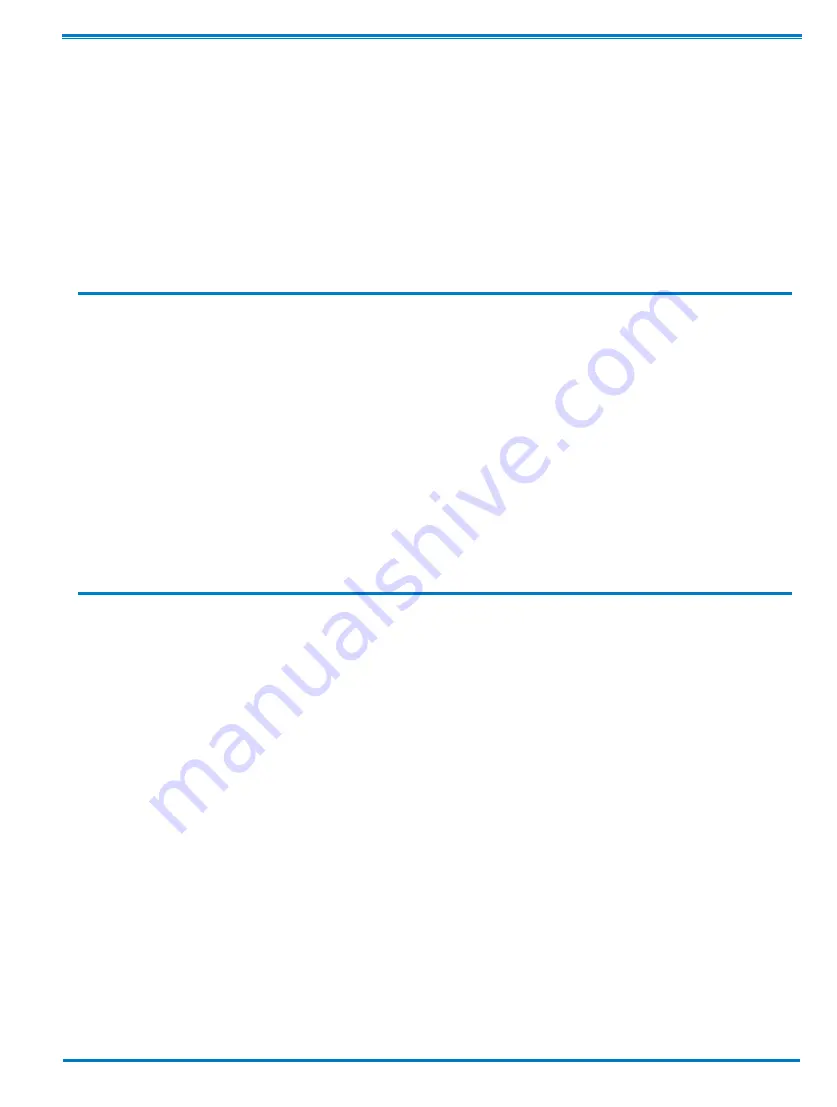
Lime Deposits
One of the easiest ways to remove lime deposits from the valve
stem or other metal parts is to dip them in a 5-percent muriatic
acid solution just long enough for the deposit to dissolve. This
will remove most of the common types of deposits.
CAUTlON:
USE EXTREME CARE WHEN HANDLING ACID.
Rinse parts in
water before handling. If the deposit is not removed by acid, then
a fine grit (400) wet or dry sandpaper can be used with water.
Reassembly
1.
Reassembly is the reverse of the disassembly procedure. If a
new disc has been installed, it may require a different number of
spacer washers to obtain the right amount of “grip” on the disc.
When the diaphragm assembly has been tightened to a point
where the diaphragm cannot be twisted, the disc should be com-
pressed very slightly by the disc guide. Excessive compression
should be avoided. Use just enough spacer washers to hold the
disc firmly without noticeable compression.
2. MAKE SURE THE STEM NUT IS VERY TIGHT.
Attach a good
fitting wrench to the nut and give it a sharp “rap” rather than a
steady pull. Usually several blows are sufficient to tighten the
stem nut for final tightening. Failure to do so could allow the
diaphragm to pull loose and tear when subjected to pressure.
Test Procedure After Valve Assembly
There are a few simple tests which can be made in the field to
make sure the Hytrol Valve has been assembled properly. Do
these before installing pilot system and returning valve to
service. These are similar to the three troubleshooting tests.
1.
Check the diaphragm assembly for freedom of movement
after all pressure is removed from the valve.
SEE CAUTlON.
Insert fabricated tool into threaded hole in top of valve stem, and
lift the diaphragm assembly manually. Note any roughness,
sticking or grabbing. The diaphragm assembly should move
smoothly throughout entire valve stroke. The tool is fabricated
from rod that is threaded on one end to fit valve stem (See chart
in Step 4 of “Disassembly” section.) and has a “T” Bar handle of
some kind on the other end for easy gripping.
Place marks on this diaphragm assembly lifting tool when the
valve is closed and when manually positioned open. The dis-
tance between the two marks should be approximately the stem
travel shown in stem travel chart. (See “Freedom of Movement
Check” section.) If the stroke is different than that shown, there
is a good reason to believe something is mechanically restricting
the stroke of the valve. The cover must be removed, the obstruc-
tion located and removed. (See “Maintenance” Section for
procedure.)
Inspection of Parts
After the valve has been disassembled, each part should be
examined carefully for signs of wear, corrosion, or any other
abnormal condition. Usually, it is a good idea to replace the rub-
ber parts (diaphragm and disc) unless they are free of signs of
wear. These are available in a repair kit. Any other parts which
appear doubtful should be replaced. WHEN ORDERlNG
PARTS, BE SURE TO GIVE COMPLETE NAMEPLATE DATA,
ITEM NUMBER AND DESCRlPTlON.
NOTE: If a new disc isn’t available, the existing disc can be
turned over, exposing the unused surface for contact with the
seat. The disc should be replaced as soon as practical.
3.
Carefully install the diaphragm assembly by lowering the stem
through the seat bearing. Take care not to damage the stem or
bearing. Line up the diaphragm holes with the stud or bolt holes
on the body. on larger valves with studs, it may be necessary to
hold the diaphragm assembly up part way while putting the
diaphragm over the studs.
4.
Put spring in place and replace cover. Make sure diaphragm
is Iying smooth under the cover.
5.
Tighten cover nuts firmly using a cross-over pattern until all
nuts are tight.
6
. Test Hytrol Valve before re-installing pilot valve system.
Due to the weight of the diaphragm assembly this procedure is
not possible on valves 8” and larger. on these valves, the same
determination can be made by carefully introducing a low
pressure-less than five psi) into the valve body with the cover
vented.
SEE CAUTION
. Looking in cover center hole see the
diaphragm assembly lift easily without hesitation, and then
settle back easily when the pressure is removed.
2.
To check the valve for drip-tight closure, a line should be
connected from the inlet to the cover, and pressure applied at the
inlet of the valve. If properly assembled, the valve should hold
tight with as low as ten PSI at the inlet. See “Tight Sealing
Check” section.)
3
. With the line connected from the inlet to the cover, apply full
working pressure to the inlet. Check all around the cover for any
leaks. Re-tighten cover nuts if necessary to stop leaks past the
diaphragm.
4.
Remove pressure, then re-install the pilot system and tubing
exactly as it was prior to removal.
Bleed air from all high
points.
5.
Follow steps under “Start-Up and Adjustment” Section in
Technical Manual for returning complete valve back to service
.
5
Distributed By: M&M Control Service, Inc.
www.mmcontrol.com/claval-index.php
800-876-0036 847-356-0566