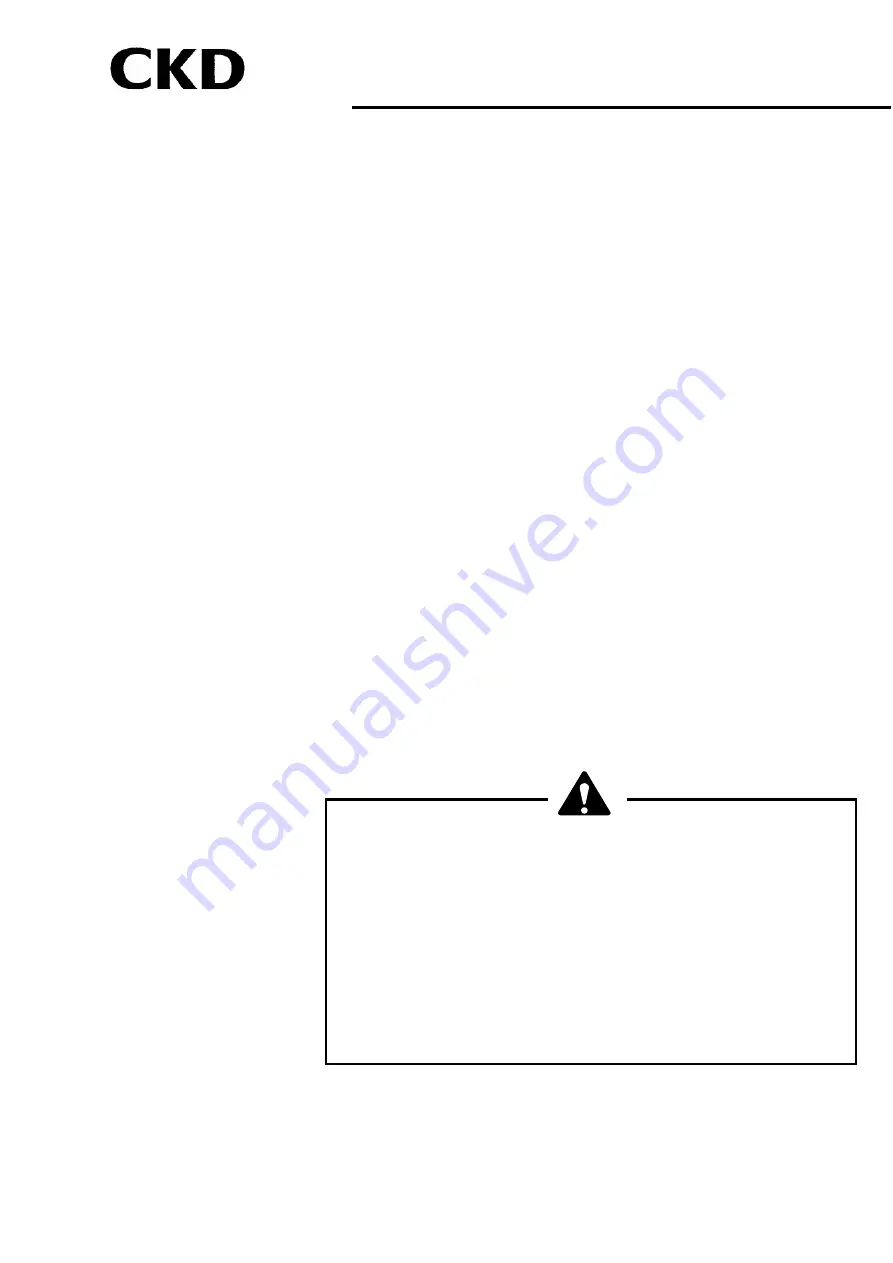
SM-450541
取 扱 説 明 書
取 扱 説 明 書
取 扱 説 明 書
取 扱 説 明 書
INSTRUCTION MANUAL
INSTRUCTION MANUAL
INSTRUCTION MANUAL
INSTRUCTION MANUAL
冷凍式エアドライヤ
GT9000WVシリ-ズ
REFRIGERATED COMPRESSED AIR DRYER
REFRIGERATED COMPRESSED AIR DRYER
REFRIGERATED COMPRESSED AIR DRYER
REFRIGERATED COMPRESSED AIR DRYER
GT
GT
GT
GT9000
9000
9000
9000WV
WV
WV
WV Series
Series
Series
Series
GT
GT
GT
GT9710
9710
9710
9710WV-AC
WV-AC
WV-AC
WV-AC200
200
200
200V
V
V
V
FEB.
FEB.
FEB.
FEB. 201
201
201
2011
11
1
CKD
CKD
CKD
CKD Corporation
Corporation
Corporation
Corporation
●
この製品は「産業用」です。取り扱いには十分注意してください。
This product is "industrial use." Be careful of handling enough.
●
据付・操作の前には必ずこの取扱説明書をお読みいただき、正しく
お使いください。
Be sure to read this manual before installing and operating your dryer.
●
巻末が保証書となっています。大切に保存してください。
The end of a book serves as WARRANTY. Please save carefully.
Discontinue
Summary of Contents for GT9000WV Series
Page 2: ...1 SM 450541 Discontinue...
Page 4: ...SM 450541 3 Discontinue...
Page 47: ...SM 450541 46 Discontinue...
Page 54: ...SM 450541 53 E03 U1 U1 1 U1 2 U1 EEPROM EEPROM CPU CPU Discontinue...
Page 74: ...SM 450541 73 10 10 10 10 Dimensions Dimensions Dimensions Dimensions Discontinue...
Page 76: ...SM 450541 75 485 8551 250 0568 77 1111 Discontinue...
Page 78: ...Discontinue...
Page 79: ...Discontinue...
Page 80: ...Discontinue...