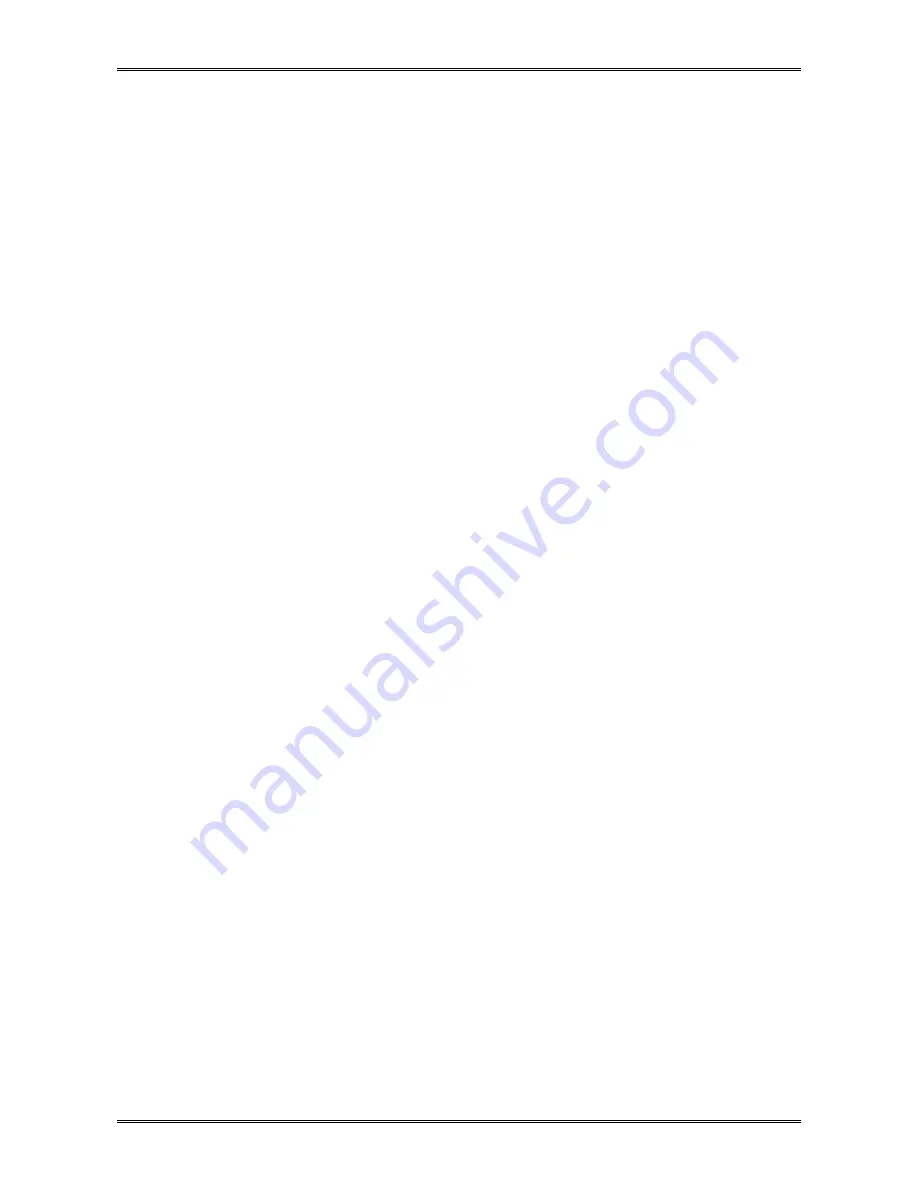
CT-292/293 Series Service Manual
INTRODUCTION
This manual describes the disassembly, reassembly, and maintenance procedures of CT-P292/293 Series.
1. DISASSEMBLY
AND
REASSEMBLY
Note the following items when performing maintenance of the printer.
•
Do not disassemble, reassemble, or adjust the printer unnecessarily when the printer operation is
satisfactory.
•
Do not loosen the screws that fasten the components unless it is absolutely necessary.
•
After finishing inspection, perform a check to ensure that there is no irregularity before turning on the
printer.
•
Use caution not to leave any part or screw used for maintenance inside the printer.
•
When handling the print head and electronic components, care must be taken to avoid static electricity.
•
When disassembling or reassembling the printer, check the wires and cords for damage. Do not draw
any wire or cord by force.
•
Lubricate the components as necessary when reassembling them.
1-1. Tools
Used
•
Phillips screwdriver #0, #1, and #2
•
Precision flat head screwdriver (2.0 mm)
•
Tweezers
•
Long-nose
pliers
•
Brush
- 4 -
Summary of Contents for CT-P292
Page 1: ...Service Manual COMPACT LINE THERMAL PRINTER CT P292 293 Series Revision 1 00 2010 2 15...
Page 27: ...CT 292 293 Series Service Manual 3 1 Mechanical Exploded Diagrams Overall exploded diagram 26...
Page 31: ...CT 292 293 Series Service Manual Exploded diagram configuration of No 207 30...
Page 33: ...CT 292 293 Series Service Manual 4 1 2 Main Control Board RAM ROM 32...
Page 34: ...CT 292 293 Series Service Manual 4 1 3 Main Control Board EXTEND PORT 33...
Page 35: ...CT 292 293 Series Service Manual 4 1 4 Main Control Board HEAD 34...
Page 36: ...CT 292 293 Series Service Manual 4 1 5 Main Control Board FEED MOTOR CUTTER 35...
Page 37: ...CT 292 293 Series Service Manual 4 1 6 Main Control Board SENSOR 36...
Page 38: ...CT 292 293 Series Service Manual 4 1 7 Main Control Board PARALLEL I F 37...
Page 39: ...CT 292 293 Series Service Manual 4 1 8 Main Control Board USB I F 38...
Page 40: ...CT 292 293 Series Service Manual 4 1 9 Main Control Board SERIAL I F POWER 39...