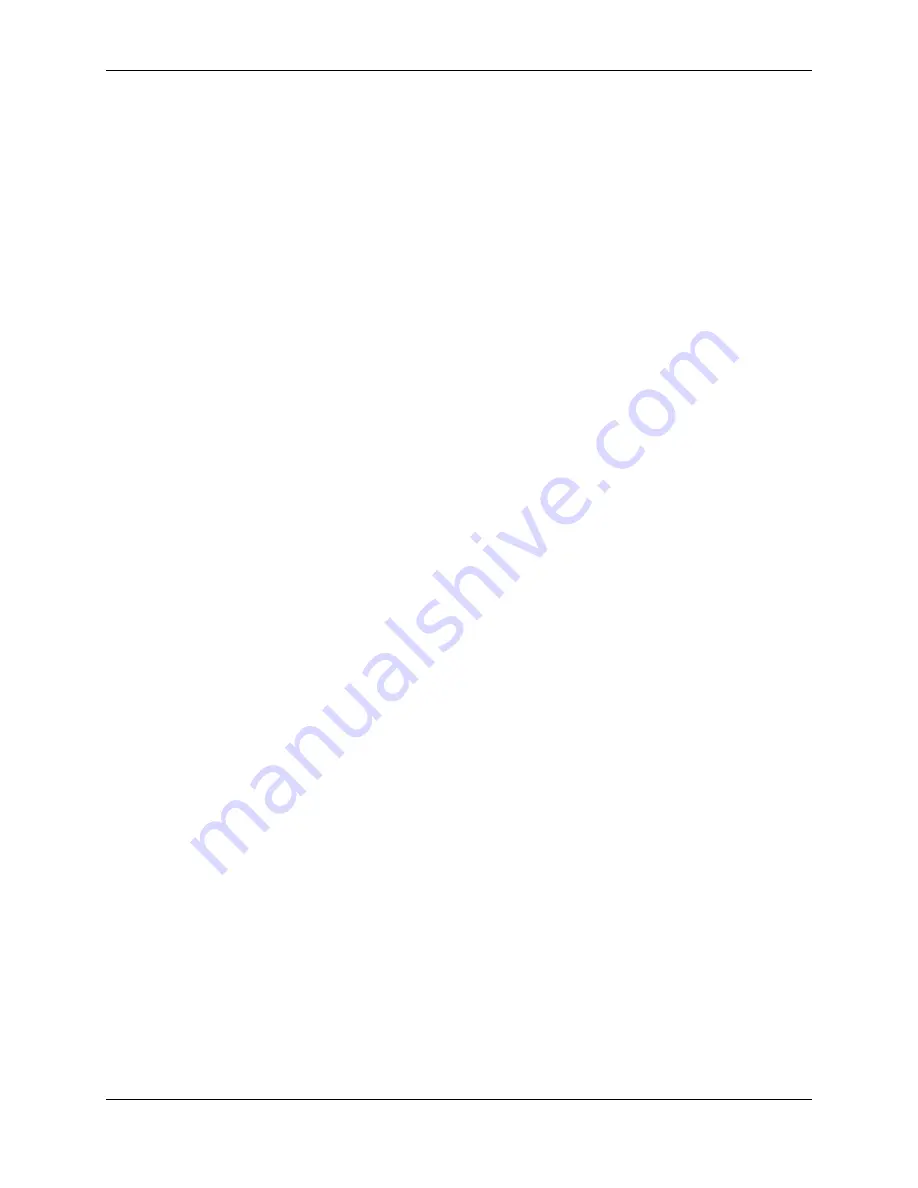
CTD-N Technical Manual
P/N 95F-6000-00 (February 2017)
page 35
EAR-Controlled Technology Subject to Restrictions Contained on the Cover Page.
8. Note: The Loop Test was partially implemented for long term stability testing of CTDs for
factory use, it is not intended as a verification of calibration and should not be used as such.
TRDI does not supply or support the resistance test device.
9. Click OK in the Diagnostics dialog box to close it.