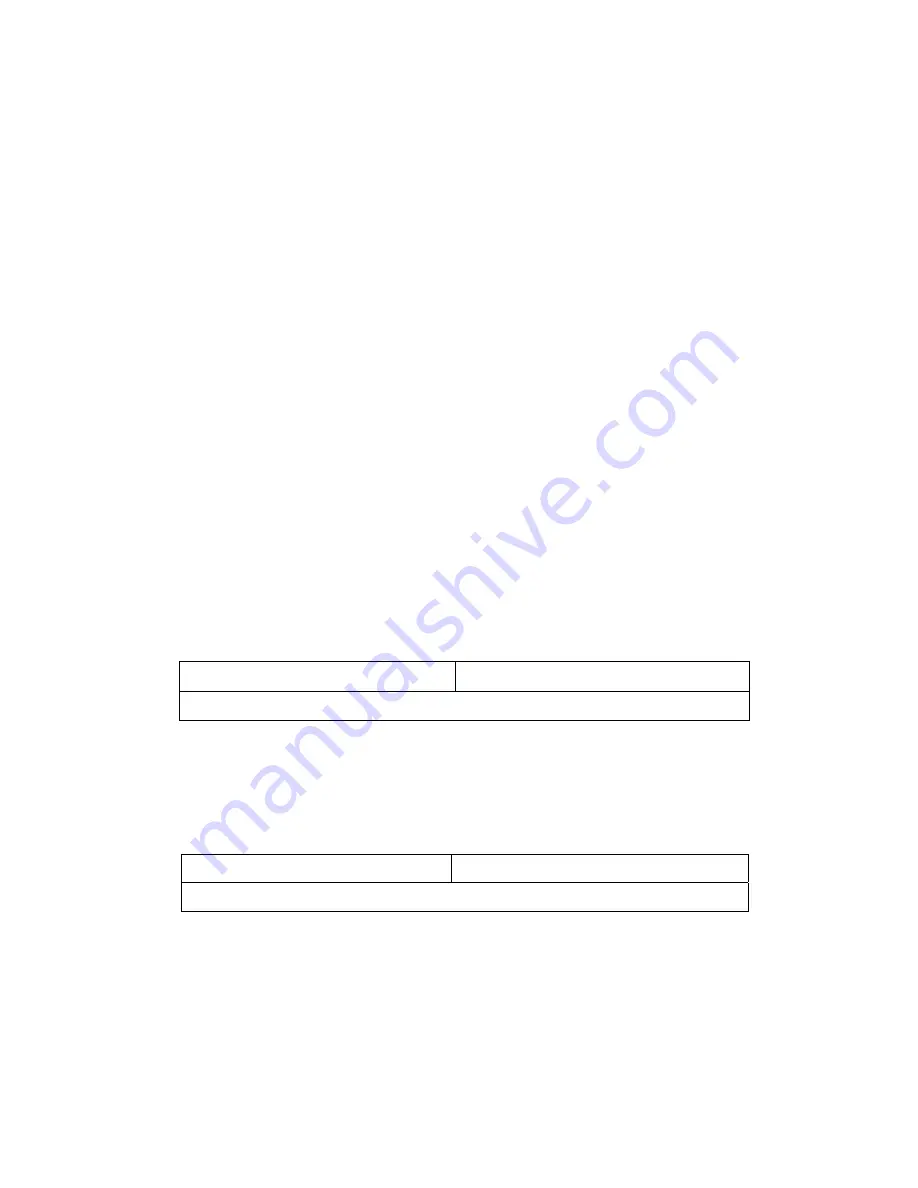
9
b. Sealed ball bearing is assembled to power rotor (63) with a light press fit. Ball bearing (49)
may be removed by using a bearing puller or a vertical arbor press. When using press, two
pieces of key stock are to be placed through openings of mechanical seal seat adapter (48)
underneath ball bearing (49) on both sides of power rotor shaft. Key stock should be long
enough to support power rotor (63) as it is placed in press. Press ram is to be positioned
against power rotor (63) coupling end face. Gently press power rotor (63) through ball
bearing (49). Ensure power rotor (63) does not fall to floor once ball bearing (49) is off of its
diameter.
c. Remove seal seat adapter (48) from power rotor (63), (See seal insert Figure 4) then remove
stationary seat from seal seat adapter (48). Loosen set screws on mechanical seal rotating
assembly body and remove rotating seal seat from power rotor (63). Remove spacer (38)
from the power rotor (63).
10. Remove O-ring (80) from inboard end cover (46).
11. Remove bolts (4) and inboard cover (46) from case (1).
12. Remove O-ring (28) from inboard cover (46).
13. Remove tube (26) from idler stop (22).
14. Remove idler stop (22) from inboard cover (46) by removing bolts (81).
15. Remove floating balance piston (79) from inboard cover (46).
16. Remove stop pin (6) and Dyna seal (7) from case (1).
17. Remove housing (24) from case (1) and O-ring (28) from housing (24).
18. Remove Orifice Plug (102) from discharge housing (24).
CAUTION
ATTENTION
Do not permit housing (24) to drop as it is removed from pump.
19. Remove tube (26) from housing (24 or 73), and O-rings (27) from tube (26).
20. Remove aligning vent pins (3) from housing (24 or 73).
21. Remove housing (73) from case (1).
CAUTION
ATTENTION
Do not permit housing (73) to drop as it is removed from pump.
H.4 PUMP ASSEMBLY PROCEDURE
Note:
Prior to reassembly of pump, all parts should be cleaned and inspected for nicks and
burrs. Replace all worn or damaged parts. Imo Pump recommends replacement of all O-
rings (9, 27, 28, and 80), Dyna Seal (7), mechanical seal (25) and ball bearing (49) when
these parts are disturbed from their previously installed positions. Coat all parts with light
lubricating oil to assist in assembly.
Note:
Bolts (81) have Nylok threads. Torque stated on assembly drawing for bolt (81) does not
include additional torque to install fasteners containing Nylok inserts. Torque required for
Summary of Contents for IMO 3220/523
Page 13: ......