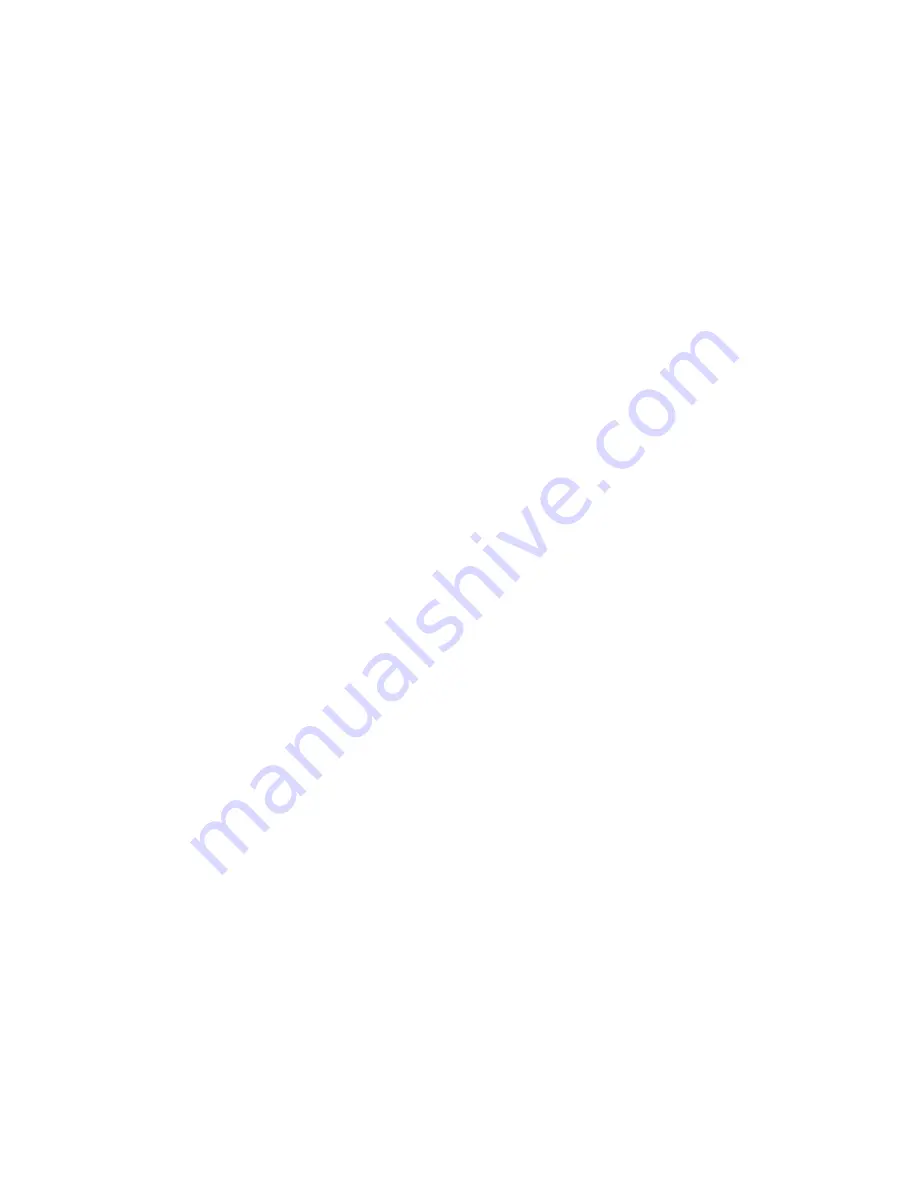
9
21. Remove strainer sub-assembly (92) from rotor housing (3).
PUMP ASSEMBLY
Prior to assembly of the pump, all parts should be cleaned and inspected for nicks and burrs. All worn or
damaged parts should be replaced. Imo Pump recommends automatic replacement of O-rings (4, 10, 12,
23, 69 or 25, 82), gasket (65), ball bearing (31), mechanical seal (27) and spiral ring (28) when these
parts are disturbed from their previous installed position. Wipe all parts with light lubricating oil prior to
assembly. Do not permit parts to stand with machined surfaces unprotected for extended periods of time.
Check all oil passages to ensure that they are clean and free of any debris. Rotate power rotor frequently
by hand during assembly to ensure freedom of rotation.
1. Install O-ring (4) in groove of discharge housing (3).
2. Install O-rings (82) in grooves of oil balance tube (87).
3. Install vent pins (8), oil balance tube (87), and strainer sub-assembly (92) in discharge housing (3).
4. Insert discharge housing (3) assembly in case (1) from the coupling end, with vent pins (8) pointed to inlet
end of case (1).
5. Assemble inlet housing (5) and discharge housing (3) together ensuring vent pins (8), oil balance tube
(87) and housing openings mesh together.
6. Install housing stop-pin (9). Install new O-ring (10) on plug (11) and thread plug into case top opening.
NOTE: Ensure slot in discharge housing (3) flange aligns with stop-pin hole in case (1).
7. Install bushing (15) into bore of inboard cover (13). Install idler stop (16) on inboard cover (13), ensuring
that spring pin engages slot in installed bushing (15). Install capscrews (18), and tighten capscrews to a
torque value of 27 lbs. ft. (± 2 lbs. ft.). Install O-rings (12) in grooves on each end of case (1).
8. Install eyebolt in ¾ - inch tapped bore in inboard cover (13) to support during assembly. Install inboard
cover (13) on case (1), using caution to avoid damage to O-ring (12) and ensuring that stop subassembly
is properly positioned with idler rotor bores of housing (3). Install capscrews (21) and lockwashers (20).
Tighten capscrews (21) to a torque value of 340 lbs. ft. (± 15 lbs. ft.).
9. Install O-ring (23) on power rotor (22). Slide balance piston (24) on power rotor (22) shaft using caution
to avoid damage to installed O-ring (23). Seat balance piston (24) against shaft shoulder.
10. Support power rotor (22) in lead lined jaws of bench vise, using extreme caution to avoid damage to
power rotor. Assemble power rotor (22) as outlined in steps 17 through 28 of Maintenance: Servicing
Mechanical Seal and/or Ball Bearing.
11. Install inlet head (37) to case (1) using capscrews (21) and lockwashers (20). Torque capscrews to 340
lbs. ft. (± 15 lbs. ft.).
12. Install idler rotors (40), tapered end first, into inlet end of housing (5). Mesh threads of idler rotors (40)
with installed power rotor (22) and rotate power rotor (22) by hand to draw idlers into proper position.
Install idler rotors (41) into inlet end of rotor housing (5). Mesh threads of idler rotors (41) with threads of
power rotor (22), and rotate power rotor (22) by hand to draw idlers into proper position.
13. Slide idler balance piston housings (44) onto end of idler rotors (41).
14. Install O-rings (82) into grooves of oil balance tube (81) and insert oil balance tube (81) into rotor housing
(5).
15. Insert capscrews (61) into plate (48). Slide spacers (88) onto capscrews (61). Mount plate (48) onto
rotor housing (5), ensuring the oil balance tube (81) is aligned with the slot in the plate (48). Torque
capscrews (61) to 73 lbs. ft. (± 5 lbs. ft.).
Summary of Contents for GLH8L-462 Series
Page 13: ......