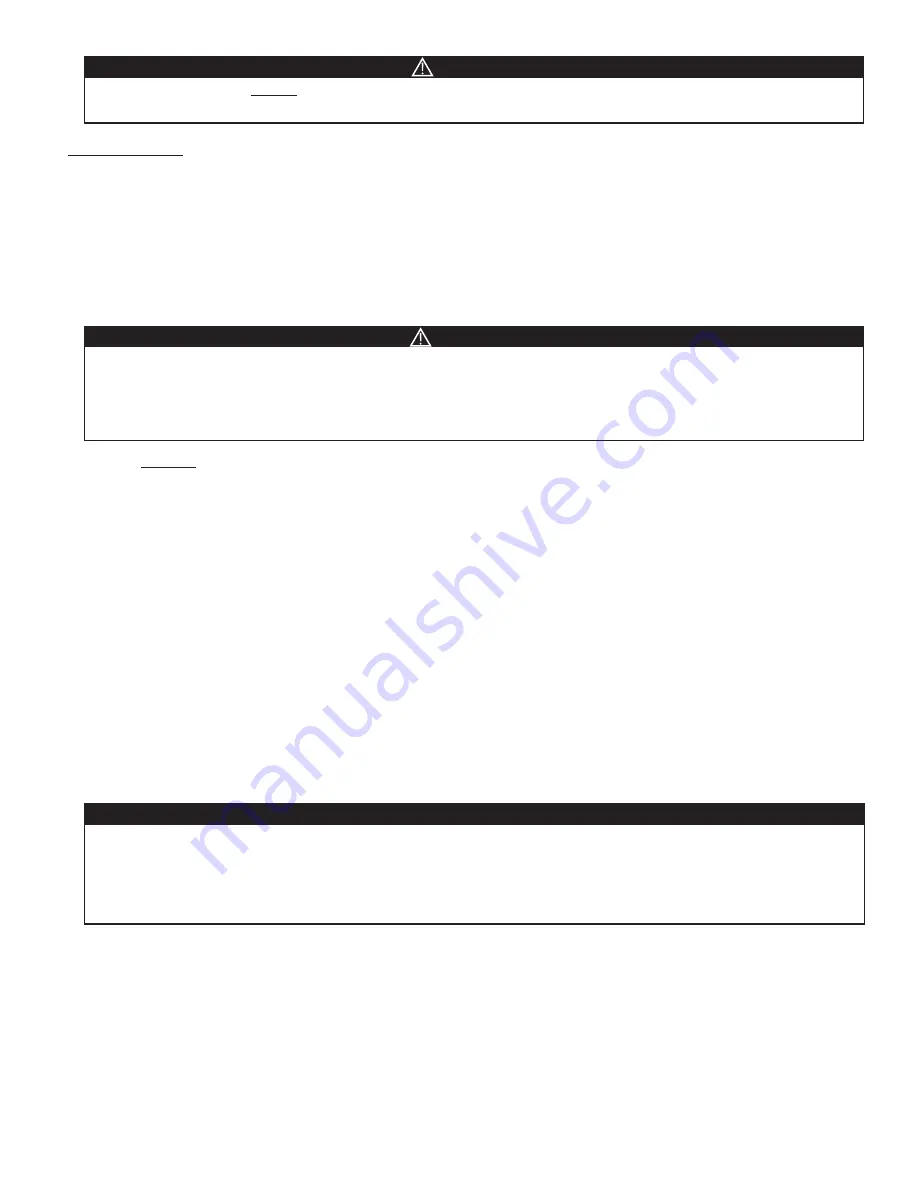
OMM-14-0509-page 5
Set screws should NEVER be used more than once. If the set screws are loosened, they MUST be replaced.
Use only knurled, cup-point, set screws with a nylon locking patch.
CAUTION
ALL WIRING CONNECTIONS, INSPECTION AND MAINTENANCE OF ANY MOTOR MUST BE PERFORMED BY A
LICENSED ELECTRICIAN IN ACCORDANCE WITH THE MOTOR MANUFACTURERS RECOMMENDATIONS, ALL
ELECTRICAL CODES AND OSHA REGULATIONS. FAILURE TO PROPERLY INSTALL, MAKE WIRING
CONNECTIONS, INSPECT OR PERFORM ANY MAINTENANCE TO A MOTOR CAN RESULT IN
MOTOR FAILURE, PROPERTY DAMAGE, EXPLOSION, ELECTRICAL SHOCK AND DEATH.
DANGER
III. ELECTRICAL
A. Disconnect Switches:
All fan motors should have an independent disconnect switch located in close visual proximity to turn off the electri-
cal service to the fan motor.
Disconnects must be locked out in accordance with OSHA “lock out-tag out” pro-
cedures any time inspection or maintenance is being performed on the fan and/or motor assembly. The
“lock out-tag out” procedure should be performed by a licensed electrician or authorized personnel.
All disconnects should be sized in accordance with the latest NEC codes (National Electric Codes) and any local
codes and should be installed only by a licensed electrician. “Slow blow” or “time delay” fuses or breakers should be
used since the initial start-up time for the fan motor, although rare, can be up to 10 seconds.
B. Motors:
1.
DO NOT connect or operate a motor without reading the motor manufacturers instructions supplied with the
fan.
The basic principle of motor maintenance is:
KEEP THE MOTOR CLEAN AND DRY.
This requires periodic
inspections of the motor. The frequency of the inspections depends on the type of motor, the service and environ-
ment it will be subjected to and the motor manufacturers instructions.
2. Cleaning:
Cleaning should be limited to exterior surfaces only.
Follow motor manufacturers cleaning instruc-
tions.
3. Lubrication:
Most small motors have sealed bearings that are permanently lubricated for the life of the motor. Some
larger motors have grease plugs that should be replaced with grease fittings to perform re-lubrication. These motors,
or any motor with grease fittings, should be lubricated in accordance with the motor manufacturers recommenda-
tions. Lubrication frequency depends on the motor horsepower, speed and service.
BE SURE
you use compatible
grease and
DO NOT
over grease.
4. Location:
On Model
DDF
fans, the motor is in the airstream. The standard motor is a Totally Enclosed type motor
which is suitable in a clean, dry airstream below 104°F. (40°C). If the airstream will be wet, dirty or reach tempera-
tures above 104°F (40°C), a completely different type of fan should be used. Consult our local sales office for your
area for proper fan selection assistance. On 12” and 15” fan sizes, if the motor is an Explosion Proof type, the motor
conduit box will not fit on the motor inside the fan drum. It is removed from the motor, shipped loose with the fan,
and will require the Purchaser of User to install it outside the drum. All wiring and connections between the conduit
box and the motor must meet NEC (National Electric Codes) standards. This assembly process should only be com-
pleted by a licensed electrician.
In order to properly perform the pre-start and the post-start checks on page 7, it is strongly recommended that an
additional conduit box be purchased and mounted on the outside of the fan drum. This will allow you to make
electrical connections from the conduit box on the motor to the outside of the fan and take motor amperage
checks outside of the fan. It will also allow you to make any fan rotation changes, if necessary. Additional motor
conduit boxes can be purchased from your local electrical supply house, motor distributor or repair shop.
NOTICE
5. Wiring Connections:
All wiring connections should be made for the proper voltage and phase as shown on the
motor nameplate. Connections should follow the motor manufacturers recommendations as shown on the wiring
schematic. This wiring diagram will be located on the outside of the motor, inside of the motor conduit box or on
the motor nameplate.
Reversing some wires might be necessary to get the correct fan rotation.
6. Motors with Thermal Overload Protection:
If a motor is equipped with thermal overloads, the thermal overload
must be wired per the wiring schematic to be operable.
There are 3 types of thermal overloads:
a. Automatic:
These will automatically shut the motor down if the internal temperature exceeds the
design limits.