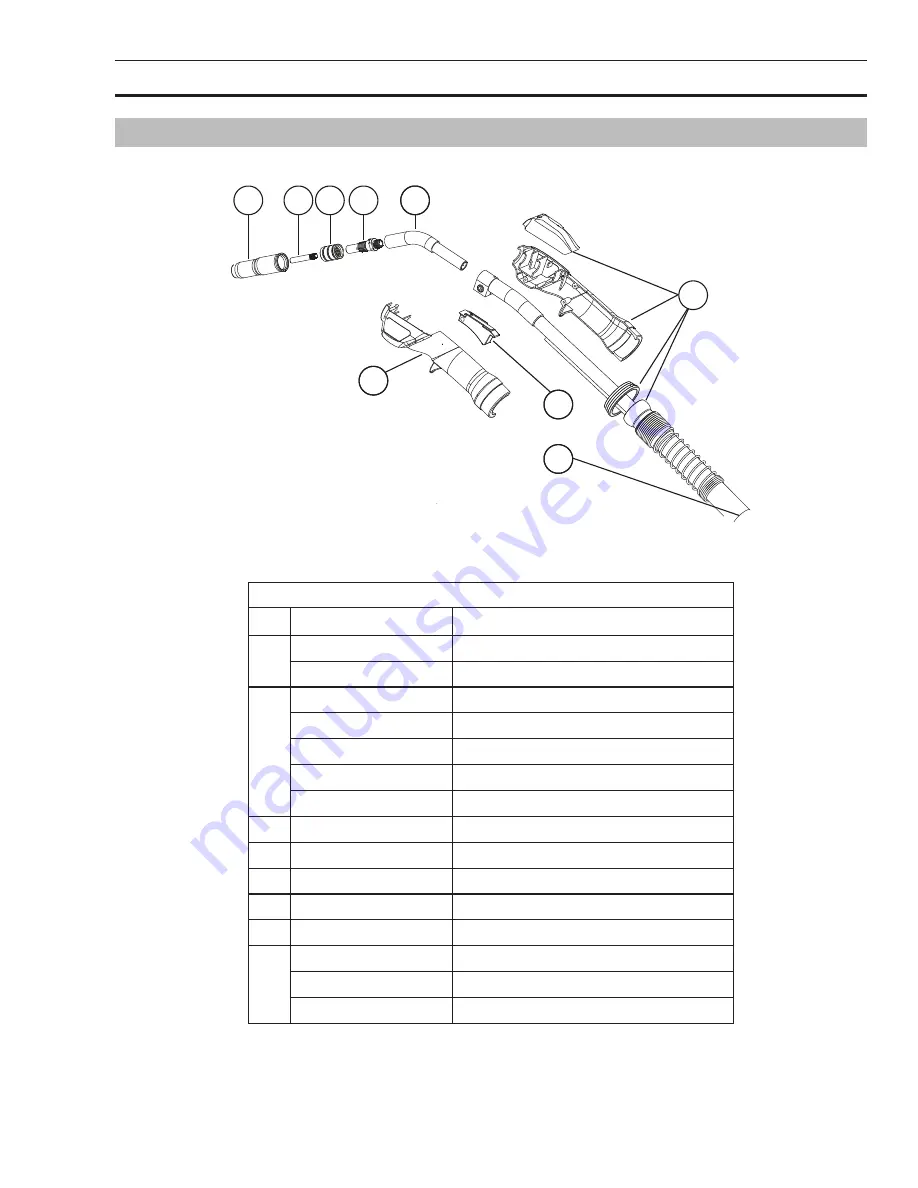
REPLACEMENT PARTS
TRANSMIG 250i
Manual 0-5188
8-1
REPLACEMENT PARTS
SECTION 8: REPLACEMENT PARTS
8.01 TWECO FUSION 250 MIG TORCH
A-10341
2
1
4
3
7
55
7
6
7
8
Figure 8-1
TWECO FUSION MIG TORCH PARTS
ITEM
PART NO.
DESCRIPTION
1
OTW22/50
Nozzle 13mm
OTW22/62
Nozzle 16mm
2
OTW14/23
Contact Tip 0.6mm
OTW14/30
Contact Tip 0.8mm
OTW14/35
Contact Tip 0.9mm
OTW14/40
Contact Tip 1.0mm
OTW14/45
Contact Tip 1.2mm
3
OTW32
Insulator
4
OTW52
Gas Diffuser
5
62J-45S
Conductor Tube, 45 Degree
6
W7005001
Trigger Assembly
7
W7005000
Handle Mouldings
8
OTW42/3035
Liner 0.8-0.9mm Hard Wire
OTW42N/3545
Liner 0.9-1.2mm Soft Wire
OTW42/4045
Liner 1.0-1.2mm Hard Wire
Table 8-1
Summary of Contents for 250i Transmig
Page 56: ...TRANSMIG 250i INSTALLATION SETUP INSTALLATION SETUP 3 38 Manual 0 5188 Notes...
Page 121: ...APPENDIX TRANSMIG 250i Manual 0 5188 A 3 APPENDIX Art A11458...
Page 122: ...TRANSMIG 250i APPENDIX APPENDIX A 4 Manual 0 5188 Notes...
Page 123: ...This page intentionally blank...
Page 127: ......