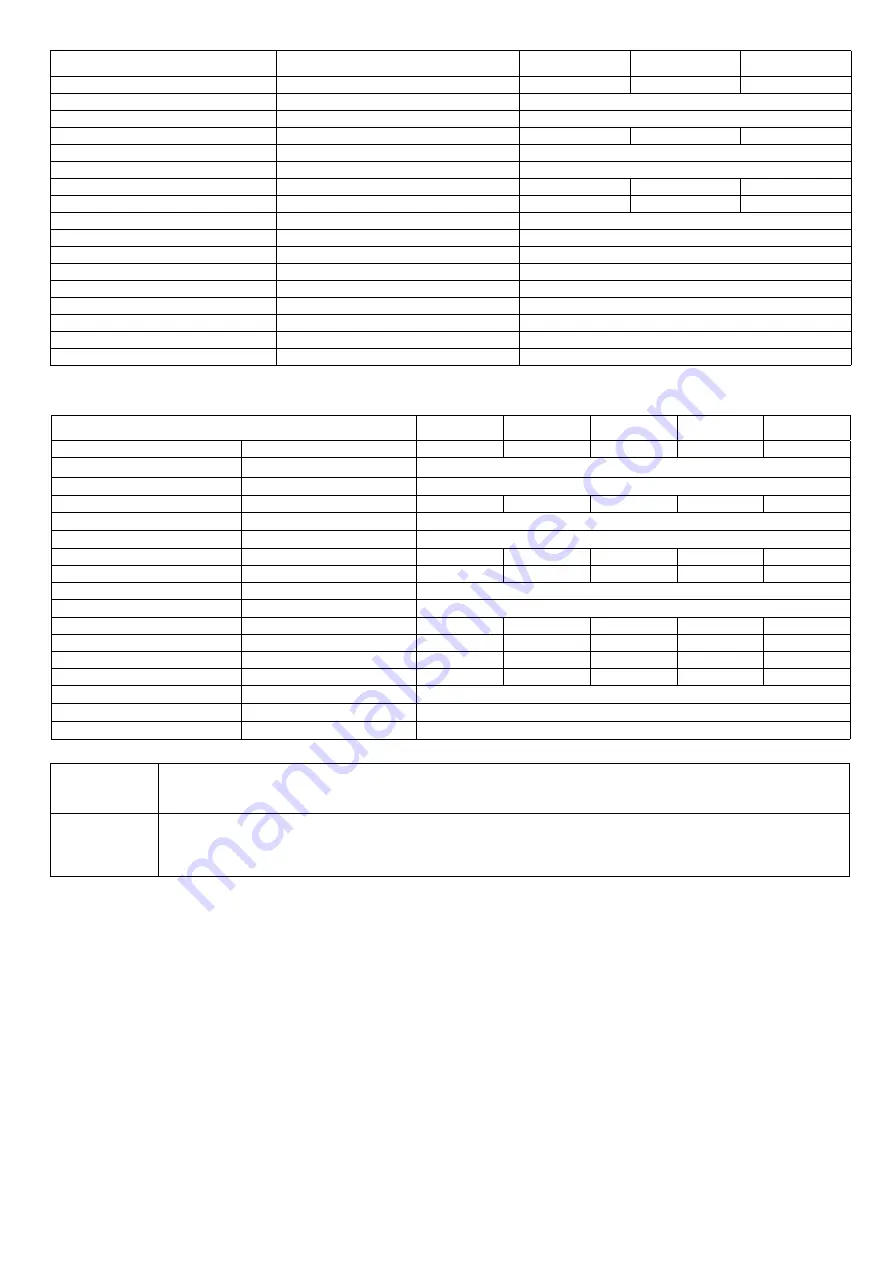
PART I: SPECIFICATIONS
7
(*) NOTE ON THE BURNER WORKING SERVICE:
LMV2x automatically stops after 24h of continuous working. The device immedia-
telystarts up, automatically. LMV3x performs countinuous operation.
BURNER TYPE
R91A L-..
R92A L-..
R93A L-..
Output
min. - max. kW
480 - 2670
480 - 3050
550 - 4100
Fuel
L -
LPG
Category
I
3B/P
Gas rate-
LPG
min.- max. (Stm
3
/h)
17.9 - 100
17.9 - 114
20 - 153
Gas pressure
mbar
(
see Note 2
)
Power supply
230V 3~ / 400V 3N ~ 50Hz
Total power consumption
kW
4.5
6.0
8.0
Electric motor
kW
4
5.5
7.5
Protection
IP40
Operation
Progressive - Fully modulating
Gas train 50
Valves size / Gas connection
50 / Rp 2
Gas train 65
Valves size / Gas connection
65 / DN65
Gas train 80
Valves size / Gas connection
80 / DN80
Gas train 100
Valves size / Gas connection
100 / DN100
Operating temperature
°C
-10 ÷ +50
Storage Temperature
°C
-20 ÷ +60
Working service (*)
Intermitent
BURNER TYPE
R512A M-..
R515A M-..
R520A M-..
R525A M-...50 R525A M-...xx
Output
min. - max. kW
600 - 4500
770 - 5200
1000 - 6400
2000 - 6700
2000 - 8000
Fuel
M -
Natural gas
Category
(
see next paragraph
)
Gas rate-
Natural gas
min.- max. (Stm
3
/h)
63 - 476
81 - 550
106 - 677
212 - 709
212 - 847
PressureGas pressure
mbar
(
see Note 2
)
Power supply
230V 3~ / 400V 3N ~ 50Hz
Total power consumption
kW
9.7
11.5
16.5
19
19
Electric motor
kW
9.2
11
15
18.5
18.5
Protection
IP40
Operation
Progressive - Fully modulating
Gas train 50
Valves size / Gas connection
50 / Rp2
50 / Rp2
50 / Rp2
50 / Rp2
Gas train 65
Valves size / Gas connection
65 / DN65
65 / DN65
65 / DN65
-
65 / DN65
Gas train 80
Valves size / Gas connection
80 / DN80
80 / DN80
80 / DN80
-
80 / DN80
Gas train 100
Valves size / Gas connection
100 / DN100
100 / DN100
100 / DN100
-
100 / DN100
Operating temperature
°C
-10 ÷ +50
Storage Temperature
°C
-20 ÷ +60
Working service (*)
Intermitent
Note1:
All gas flow rates are referred to Stm
3
/h (1013 mbar absolute pressure, 15 °C temperature) and are valid for G20 gas
(net calorific value H
i
= 34.02 MJ/Stm
3
); for L.P.G. (net calorific value H
i
= 93.5 MJ/Stm
3
)
Note2:
Maximum gas pressure = 360mbar (with
Dungs MBDLE)
= 500mbar (with
Siemens VGD)
Minimum gas pressure = see gas curves.