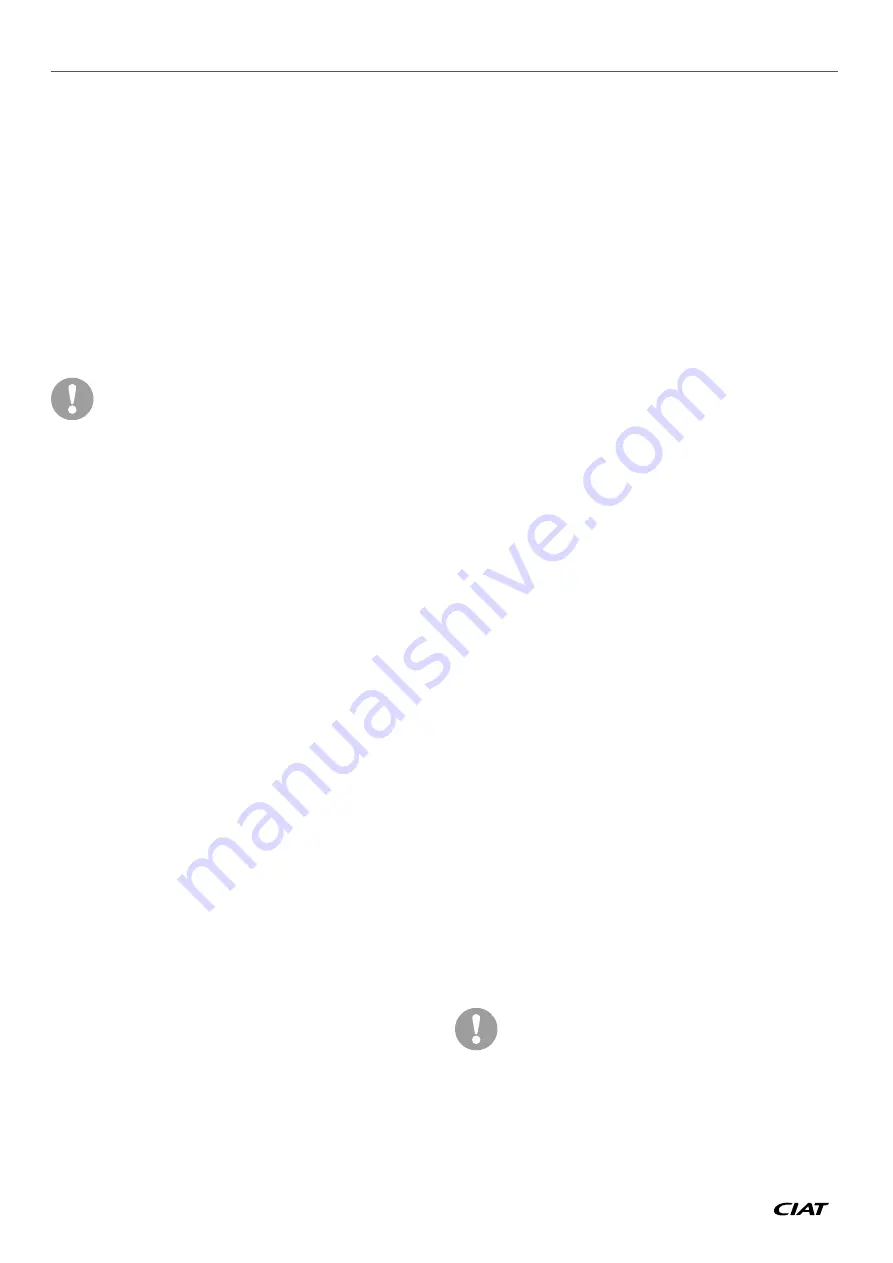
13 - STANDARD MAINTENANCE
To ensure optimal efficiency and reliability of the equipment and
all its functions, we recommend taking out a maintenance contract
with the local organisation set up by your manufacturer.
This contract will include regular inspections by the manufacturer’s
Service specialists so that any malfunction is detected and
corrected quickly, ensuring that no serious damage can occur.
The manufacturer's service maintenance contract is the best way
to ensure the maximum operating life for your equipment and,
through the expertise of manufacturer's qualified personnel,
provides the ideal way to manage your system energy consumption
effectively.
The refrigeration equipment must be serviced by professionals;
however, routine checks may be carried out locally by specially-
trained technicians. See standard EN 378-4.
All refrigerant charging, removal and draining operations must be
carried out by a qualified technician and with the correct equipment
for the unit. Any inappropriate handling can lead to uncontrolled
fluid or pressure leaks.
Before performing any work on the unit, ensure it is
de-energised. If a refrigerant circuit is opened, it must
be evacuated, recharged and tested for leaks. Before
any operation on a refrigerant circuit, it is necessary
to evacuate the refrigerant charge from the device
using a charge transfer unit.
Simple preventive maintenance will allow you to get the best
performance from your HVAC unit:
-
Optimisation of energy performance,
-
Reduced electricity consumption,
-
Prevention of accidental component failure,
-
Prevention of major time-consuming and costly work,
- Protection of the environment.
There are five maintenance levels for refrigeration units, as defined
by the AFNOR X60-010 standard.
NOTE: Any deviation from or failure to comply with these
maintenance criteria will render the guarantee conditions for
the refrigeration unit null and void, and will release the
manufacturer from its liability.
13.1 - Level 1 maintenance
These simple procedures can be carried out by the user:
-
Visual inspection for oil traces (sign of a refrigerant leak),
-
Check for leaks in the circuit (monthly),
-
Clean the air-cooled exchangers (see the dedicated chapter),
- Check that the protective grilles are present and in good
condition, and that the doors and covers are properly closed,
- Check the alarm report if the unit does not operate (see the
control manual),
-
Verify the refrigerant charge in the liquid line sight glass,
-
Verify the temperature difference at the heat exchanger inlet
and outlet is correct,
-
Check for any general signs of deterioration,
- Check the anti-corrosion coatings.
13.2 - Level 2 maintenance
This level requires specific expertise in electrical, hydraulic and
mechanical systems.It is possible that this expertise may be
available locally; there may be a maintenance service, industrial
site or specialist subcontractor in the area.
The frequency of this maintenance level may be monthly or annual,
depending on the verification type.
In these cases, the following maintenance work is recommended:
Carry out all level 1 operations, then:
Electrical checks (annual checks):
-
At least once a year, tighten the electrical connections for the
power circuits (see tightening torques table),
-
Check and tighten all control connections, if required,
-
Check the labelling of the system and instruments, re-apply the
missing labels if required,
- Remove the dust and clean the interior of the electrical boxes.
Be careful not to blow dust or debris into components; use a
brush and vacuum wherever possible,
- Clean the insulators and bus bar supports (dust combined with
moisture reduces the insulation gaps and increases current
leakage between phases and from phase to ground),
-
Check the presence, condition and operation of electrical
protective devices,
-
Check the presence, condition and operation of control
components,
-
Check that all heaters are operating correctly,
-
Replace the fuses every 3 years or every 15000 hours (ageing),
-
Check that no water has penetrated into the electrical box,
-
On the main electrical box and for units equipped with offset
electrical boxes, regularly check the cleanliness of the filter
media to maintain the correct air flow.
- Check that the capacitor is operating correctly (Power factor
correction option).
Mechanical checks:
- Check that the mounting bolts for the ventilation
sub-assemblies, fans, compressors and electrical box are
securely tightened
Hydraulic checks:
-
When working on the hydraulic circuit, take care not to damage
the adjacent air-cooled exchanger,
-
Check the hydraulic connections,
- Check the condition of the expansion tank (presence of
corrosion or loss of gas pressure) and replace it if required,
-
Drain the hydraulic circuit (see chapter “Water flow control
procedure”),
-
Clean the water filter (see chapter “Water flow control
procedure”),
- Replace the gland packing of the pump after 20000 hours of
operation and the bearings after 17500 hours,
-
Check the operation of the low water flow safety device,
-
Check the condition of pipe thermal insulation,
- Check the concentration of the anti-freeze protection (ethylene
glycol or propylene glycol),
- Check the water flow via the heat exchanger pressure
difference,
-
Check the condition of the heat-transfer fluid or the water quality,
- Check for corrosion of the steel pipe work.
Refrigerant circuit checks:
- The unit is subject to F-gas tight regulatory checks. Please refer
to the table in the introduction.
- Check the unit operating parameters and compare them with
the previous values,
- Check the operation of the high-pressure switches. Replace
them if there is a fault,
-
Check the fouling of the filter dryer. Replace it if required,
-
Keep and maintain a maintenance sheet, attached to each
HVAC unit.
Ensure all adequate safety measures are taken for all
these operations: use appropriate PPE (personal
protective equipment), comply with all industry and
local regulations, use common sense.
AQUACIAT
POWER
™ LD/ILD
EN-74
Summary of Contents for AQUACIAT POWER LD 1100R
Page 1: ...AQUACIAT POWER LD 602R 3500R ILD 602R 2000R 12 2021 10590 Instruction manual...
Page 81: ...EN 81 AQUACIATPOWER LD ILD...
Page 82: ......
Page 83: ......