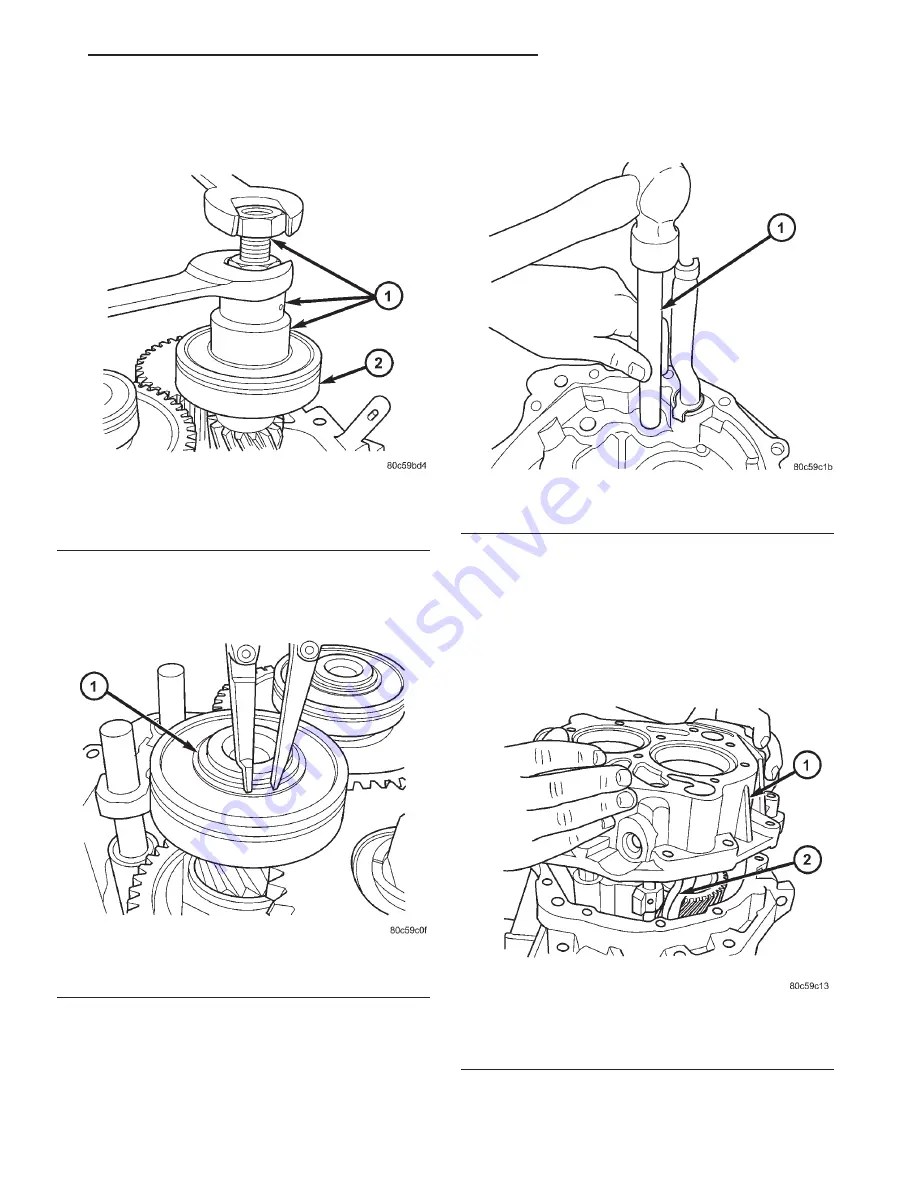
(14) Install input shaft sealed roller bearing using
installer 8482 (Fig. 58).
(15) Install new input shaft bearing snap ring
(Fig. 59).
(16) Install shift rail bushing to end cover using
installer 8475 (Fig. 60).
(17) Apply a 1 mm (0.04 in.) bead of Mopar
t
Gas-
ket Maker to transaxle end cover and install to
transaxle case (Fig. 61). While installing end
cover, be sure to guide oil trough into pocket
(Fig. 62). Torque end cover-to-case bolts to 28 N·m
(250 in. lbs.) (Fig. 63).
Fig. 58 Install Input Shaft Sealed Roller Bearing
1 - INSTALLER 8482
2 - SEALED ROLLER BEARING
Fig. 59 Input Shaft Bearing Snap Ring
1 - SNAP RING
Fig. 60 Shift Rail Bushing Installation
1 - INSTALLER 8475
Fig. 61 End Cover Removal/Installation
1 - END COVER
2 - OIL TROUGH
RS
T850 MANUAL TRANSAXLE
21 - 333
T850 MANUAL TRANSAXLE (Continued)
Summary of Contents for Dodge Caravan 2002
Page 4: ...Fig 2 FASTENER IDENTIFICATION RS INTRODUCTION 3 FASTENER IDENTIFICATION Continued...
Page 5: ...Fig 3 FASTENER STRENGTH 4 INTRODUCTION RS FASTENER IDENTIFICATION Continued...
Page 8: ...Fig 5 METRIC CONVERSION CHART RS INTRODUCTION 7 METRIC SYSTEM Continued...
Page 13: ......
Page 23: ......
Page 129: ......
Page 249: ......
Page 453: ......
Page 469: ......
Page 475: ......
Page 501: ......
Page 541: ......
Page 609: ......
Page 637: ......
Page 659: ......
Page 675: ......
Page 680: ......
Page 681: ......
Page 682: ......
Page 683: ......
Page 684: ......
Page 685: ......
Page 686: ......
Page 687: ......
Page 688: ......
Page 689: ......
Page 690: ......
Page 691: ......
Page 692: ......
Page 693: ......
Page 694: ......
Page 695: ......
Page 696: ......
Page 697: ......
Page 698: ......
Page 699: ......
Page 700: ......
Page 701: ......
Page 702: ......
Page 703: ......
Page 704: ......
Page 705: ......
Page 706: ......
Page 707: ......
Page 708: ......
Page 709: ......
Page 710: ......
Page 711: ......
Page 712: ......
Page 713: ......
Page 714: ......
Page 715: ......
Page 716: ......
Page 717: ......
Page 718: ......
Page 719: ......
Page 720: ......
Page 721: ......
Page 722: ......
Page 723: ......
Page 724: ......
Page 725: ......
Page 726: ......
Page 727: ......
Page 728: ......
Page 729: ......
Page 730: ......
Page 731: ......
Page 732: ......
Page 733: ......
Page 734: ......
Page 735: ......
Page 736: ......
Page 737: ......
Page 738: ......
Page 739: ......
Page 740: ......
Page 741: ......
Page 742: ......
Page 743: ......
Page 744: ......
Page 745: ......
Page 747: ......
Page 748: ......
Page 749: ......
Page 750: ......
Page 751: ......
Page 752: ......
Page 753: ......
Page 754: ......
Page 755: ......
Page 756: ......
Page 757: ......
Page 758: ......
Page 759: ......
Page 760: ......
Page 761: ......
Page 762: ......
Page 763: ......
Page 764: ......
Page 765: ......
Page 766: ......
Page 767: ......
Page 768: ......
Page 769: ......
Page 770: ......
Page 771: ......
Page 773: ......
Page 774: ......
Page 775: ......
Page 776: ......
Page 777: ......
Page 779: ......
Page 780: ......
Page 781: ......
Page 783: ......
Page 784: ......
Page 785: ......
Page 787: ......
Page 788: ......
Page 789: ......
Page 790: ......
Page 791: ......
Page 792: ......
Page 793: ......
Page 794: ......
Page 795: ......
Page 796: ......
Page 797: ......
Page 798: ......
Page 799: ......
Page 800: ......
Page 801: ......
Page 802: ......
Page 803: ......
Page 804: ......
Page 805: ......
Page 806: ......
Page 807: ......
Page 808: ......
Page 809: ......
Page 810: ......
Page 811: ......
Page 812: ......
Page 813: ......
Page 814: ......
Page 815: ......
Page 816: ......
Page 817: ......
Page 819: ......
Page 820: ......
Page 821: ......
Page 822: ......
Page 823: ......
Page 824: ......
Page 825: ......
Page 826: ......
Page 827: ......
Page 829: ......
Page 830: ......
Page 831: ......
Page 833: ......
Page 834: ......
Page 835: ......
Page 837: ......
Page 838: ......
Page 839: ......
Page 840: ......
Page 841: ......
Page 842: ......
Page 843: ......
Page 844: ......
Page 845: ......
Page 846: ......
Page 847: ......
Page 848: ......
Page 849: ......
Page 850: ......
Page 851: ......
Page 853: ......
Page 854: ......
Page 855: ......
Page 856: ......
Page 857: ......
Page 858: ......
Page 859: ......
Page 860: ......
Page 861: ......
Page 862: ......
Page 863: ......
Page 865: ......
Page 866: ......
Page 867: ......
Page 869: ...2002 RS Service Manual Publication No 81 370 02062 TSB 26 12 01 December 2001...
Page 870: ......
Page 871: ......
Page 872: ......
Page 873: ...2002 RS Service Manual Publication No 81 370 02062 TSB 26 12 01 December 2001...
Page 874: ......
Page 875: ......
Page 876: ......
Page 877: ......
Page 878: ......
Page 879: ......
Page 880: ......
Page 881: ......
Page 882: ......
Page 883: ......
Page 884: ......
Page 885: ......
Page 887: ......
Page 888: ......
Page 889: ......
Page 890: ......
Page 891: ......
Page 892: ......
Page 893: ......
Page 895: ......
Page 896: ......
Page 897: ......
Page 898: ......
Page 899: ......
Page 900: ......
Page 901: ......
Page 903: ......
Page 904: ......
Page 905: ......
Page 906: ......
Page 907: ......
Page 908: ......
Page 909: ......
Page 910: ......
Page 911: ......
Page 912: ......
Page 913: ......
Page 914: ......
Page 915: ......
Page 916: ......
Page 917: ......
Page 918: ......
Page 919: ......
Page 920: ......
Page 921: ......
Page 923: ......
Page 925: ......
Page 926: ......
Page 927: ......
Page 928: ......
Page 929: ......
Page 930: ......
Page 931: ......
Page 932: ......
Page 933: ......
Page 934: ......
Page 935: ......
Page 937: ......
Page 938: ......
Page 939: ......
Page 941: ......
Page 942: ......
Page 943: ......
Page 945: ......
Page 946: ......
Page 947: ......
Page 948: ......
Page 949: ......
Page 950: ......
Page 951: ......
Page 952: ......
Page 953: ......
Page 954: ......
Page 955: ......
Page 957: ......
Page 958: ......
Page 959: ......
Page 960: ......
Page 961: ......
Page 963: ......
Page 964: ......
Page 965: ......
Page 966: ......
Page 967: ......
Page 969: ......
Page 970: ......
Page 971: ......
Page 972: ......
Page 973: ......
Page 975: ......
Page 976: ......
Page 977: ......
Page 979: ......
Page 980: ......
Page 981: ......
Page 982: ......
Page 983: ......
Page 984: ......
Page 985: ......
Page 987: ......
Page 988: ......
Page 989: ......
Page 990: ......
Page 991: ......
Page 992: ......
Page 993: ......
Page 994: ......
Page 995: ......
Page 996: ......
Page 997: ......
Page 998: ......
Page 999: ......
Page 1000: ......
Page 1001: ......
Page 1002: ......
Page 1003: ......
Page 1004: ......
Page 1005: ......
Page 1007: ......
Page 1008: ......
Page 1009: ......
Page 1010: ......
Page 1011: ......
Page 1012: ......
Page 1013: ......
Page 1014: ......
Page 1015: ......
Page 1017: ......
Page 1018: ......
Page 1019: ......
Page 1020: ......
Page 1021: ......
Page 1022: ......
Page 1023: ......
Page 1024: ......
Page 1025: ......
Page 1027: ......
Page 1028: ......
Page 1029: ......
Page 1030: ......
Page 1031: ......
Page 1423: ......
Page 1433: ......
Page 1444: ...Fig 6 CROSSMEMBER DIMENSIONS RS FRAME BUMPERS 13 5 FRAME Continued...
Page 1445: ...Fig 7 ENGINE BOX TOP VIEW 13 6 FRAME BUMPERS RS FRAME Continued...
Page 1446: ...Fig 8 ENGINE COMPARTMENT AND FRAME RAIL SIDE VIEW RS FRAME BUMPERS 13 7 FRAME Continued...
Page 1447: ...Fig 9 FULL VEHICLE BOTTOM VIEW 13 8 FRAME BUMPERS RS FRAME Continued...
Page 1487: ......
Page 1514: ...Fig 2 Steering Column And Components Typical RS COLUMN 19 11 COLUMN Continued...
Page 1557: ......
Page 1559: ...Power Transfer Unit Components 21 2 POWER TRANSFER UNIT RS POWER TRANSFER UNIT Continued...
Page 1623: ...Drive Third Not Locked Up 21 66 31TH AUTOMATIC TRANSAXLE RS 31TH AUTOMATIC TRANSAXLE Continued...
Page 1624: ...Drive Third Lock Up RS 31TH AUTOMATIC TRANSAXLE 21 67 31TH AUTOMATIC TRANSAXLE Continued...
Page 1628: ...Reverse RS 31TH AUTOMATIC TRANSAXLE 21 71 31TH AUTOMATIC TRANSAXLE Continued...
Page 1774: ...Neutral Speed Over 8 MPH RS 41TE AUTOMATIC TRANSAXLE 21 217 41TE AUTOMATIC TRANSAXLE Continued...
Page 1775: ...Reverse 21 218 41TE AUTOMATIC TRANSAXLE RS 41TE AUTOMATIC TRANSAXLE Continued...
Page 1777: ...First Gear 21 220 41TE AUTOMATIC TRANSAXLE RS 41TE AUTOMATIC TRANSAXLE Continued...
Page 1778: ...Second Gear RS 41TE AUTOMATIC TRANSAXLE 21 221 41TE AUTOMATIC TRANSAXLE Continued...
Page 1779: ...Second Gear EMCC 21 222 41TE AUTOMATIC TRANSAXLE RS 41TE AUTOMATIC TRANSAXLE Continued...
Page 1780: ...Direct Gear RS 41TE AUTOMATIC TRANSAXLE 21 223 41TE AUTOMATIC TRANSAXLE Continued...
Page 1781: ...Direct Gear CC On 21 224 41TE AUTOMATIC TRANSAXLE RS 41TE AUTOMATIC TRANSAXLE Continued...
Page 1782: ...Overdrive RS 41TE AUTOMATIC TRANSAXLE 21 225 41TE AUTOMATIC TRANSAXLE Continued...
Page 1783: ...Overdrive EMCC 21 226 41TE AUTOMATIC TRANSAXLE RS 41TE AUTOMATIC TRANSAXLE Continued...
Page 1784: ...Overdrive CC On RS 41TE AUTOMATIC TRANSAXLE 21 227 41TE AUTOMATIC TRANSAXLE Continued...
Page 1961: ......
Page 1976: ...VEHICLE LEAD DIAGNOSIS AND CORRECTION CHART RS TIRES WHEELS 22 15 TIRES Continued...
Page 2099: ...Fig 1 GAP FLUSH MEASUREMENTS 23 116 BODY STRUCTURE RS GAP AND FLUSH Continued...
Page 2102: ...Fig 3 LIFTGATE OPENING RS BODY STRUCTURE 23 119 OPENING DIMENSIONS Continued...
Page 2103: ...Fig 4 BODY SIDE OPENINGS 23 120 BODY STRUCTURE RS OPENING DIMENSIONS Continued...
Page 2143: ...Fig 64 STRUT TOWER AND REINFORCEMENTS RIGHT 23 160 BODY STRUCTURE RS WELD LOCATIONS Continued...
Page 2145: ...Fig 66 STRUT TOWER AND REINFORCEMENTS LEFT 23 162 BODY STRUCTURE RS WELD LOCATIONS Continued...
Page 2147: ...Fig 68 FLOOR PAN REINFORCEMENTS SIDE RAILS 23 164 BODY STRUCTURE RS WELD LOCATIONS Continued...
Page 2148: ...Fig 69 REAR SUSPENSION BRACKETS RS BODY STRUCTURE 23 165 WELD LOCATIONS Continued...
Page 2149: ...Fig 70 FLOOR PAN CROSS MEMBERS 23 166 BODY STRUCTURE RS WELD LOCATIONS Continued...
Page 2154: ...Fig 75 FRONT SEAT CROSS MEMBER RS BODY STRUCTURE 23 171 WELD LOCATIONS Continued...
Page 2155: ...Fig 76 FLOOR PAN SIDE RAIL REINFORCEMENT 23 172 BODY STRUCTURE RS WELD LOCATIONS Continued...
Page 2156: ...Fig 77 SILL BULKHEAD REINFORCEMENTS RS BODY STRUCTURE 23 173 WELD LOCATIONS Continued...
Page 2157: ...Fig 78 FLOOR PAN CROSS MEMBER REINFORCEMENTS 23 174 BODY STRUCTURE RS WELD LOCATIONS Continued...
Page 2158: ...Fig 79 FRONT SEAT CROSS MEMBER RS BODY STRUCTURE 23 175 WELD LOCATIONS Continued...
Page 2163: ...Fig 84 ENGINE MOUNTING PLATE AND TOW BRACKET 23 180 BODY STRUCTURE RS WELD LOCATIONS Continued...
Page 2164: ...Fig 85 HEADLAMP MOUNTING PLATE RS BODY STRUCTURE 23 181 WELD LOCATIONS Continued...
Page 2165: ...Fig 86 LOWER RADIATOR CROSS MEMBER BRACKETS 23 182 BODY STRUCTURE RS WELD LOCATIONS Continued...
Page 2166: ...Fig 87 CROSS MEMBER EXTENSIONS RS BODY STRUCTURE 23 183 WELD LOCATIONS Continued...
Page 2181: ...Fig 106 DASH PANEL REINFORCEMENT 23 198 BODY STRUCTURE RS WELD LOCATIONS Continued...
Page 2182: ...Fig 107 LOWER COWL PLENUM RS BODY STRUCTURE 23 199 WELD LOCATIONS Continued...
Page 2183: ...Fig 108 UPPER COWL PLENUM SUPPORT 23 200 BODY STRUCTURE RS WELD LOCATIONS Continued...
Page 2184: ...Fig 109 UPPER DASH PANEL RS BODY STRUCTURE 23 201 WELD LOCATIONS Continued...
Page 2187: ...Fig 114 FRONT SIDE RAILS TO LOWER DASH PANEL 23 204 BODY STRUCTURE RS WELD LOCATIONS Continued...
Page 2189: ...Fig 116 FRONT HINGE TAPPING PLATE 23 206 BODY STRUCTURE RS WELD LOCATIONS Continued...
Page 2190: ...Fig 117 FRONT HINGE PILLAR RS BODY STRUCTURE 23 207 WELD LOCATIONS Continued...
Page 2191: ...Fig 118 INNER WINDSHIELD FRAME 23 208 BODY STRUCTURE RS WELD LOCATIONS Continued...
Page 2192: ...Fig 119 WINDSHIELD FRAME RS BODY STRUCTURE 23 209 WELD LOCATIONS Continued...
Page 2193: ...Fig 120 FENDER BRACKET 23 210 BODY STRUCTURE RS WELD LOCATIONS Continued...
Page 2194: ...Fig 121 INNER B PILLAR RS BODY STRUCTURE 23 211 WELD LOCATIONS Continued...
Page 2217: ...Fig 148 LOWER SLIDING DOOR TRACK 23 234 BODY STRUCTURE RS WELD LOCATIONS Continued...
Page 2219: ...Fig 151 FRONT FENDER SHIELD BEAM 23 236 BODY STRUCTURE RS WELD LOCATIONS Continued...
Page 2221: ...Fig 153 HINGE PILLAR REINFORCEMENT 23 238 BODY STRUCTURE RS WELD LOCATIONS Continued...
Page 2222: ...Fig 154 INNER SIDE SILL LONG WHEEL BASE ONLY RS BODY STRUCTURE 23 239 WELD LOCATIONS Continued...
Page 2243: ......
Page 2297: ...Fig 4 Blower Motor Noise Vibration Diagnosis 24 54 DISTRIBUTION REAR RS BLOWER MOTOR Continued...
Page 2387: ......