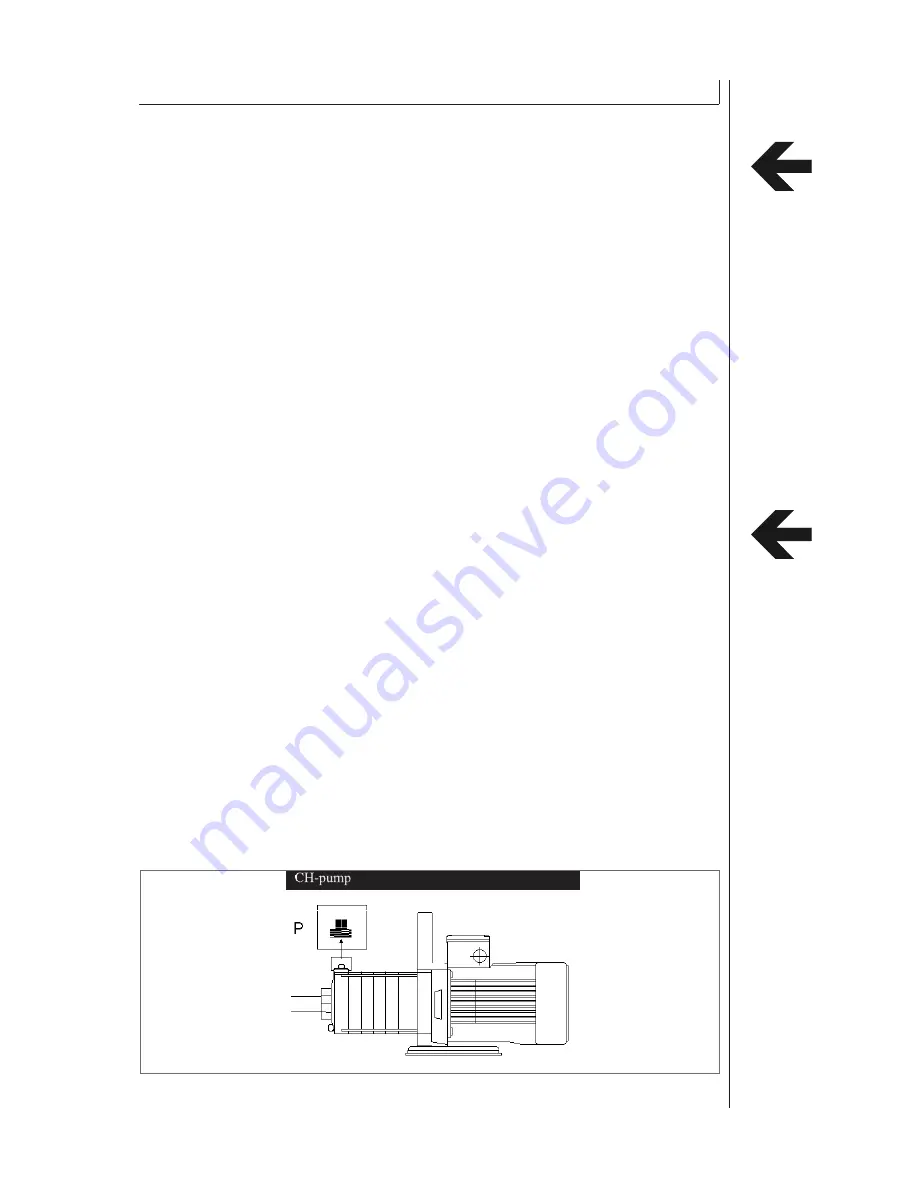
Operating Instructions
7
3
INSTALLATION AND INITIAL OPERATION
Important:
Prior to fi lling of the tank it is esessential to test the water quality and if required carry out watertreatment (re-
fer to chapter 7).
To avoid corrosion at the stainless steel evaporator, we recommend to use water with a low salt content (chloride
content < 20 mg/l). To avoid thickening of the tank water, we recommend to replace the system content every 1 to
3 months.
an increasing evaporation of the tank water means an increasing chloride content
(
please refer to chapter 6).
For chillers running at temperatures lower than freezing point, a water/glycol mixture at the
appropriate ratio should be fi lled.
30% Glycol up to –10°C, at lower temperatures
please refer to the manufacturer.
The tank should be fi lled to the max. level of the water level tube.
Prior to start up it is always necessary to prime the pump with the medium to be transported.
Prior to start up the pump must be bled in order to remove air from the pump.
Bleeding of the pump
Remove bleeding screw P (option)
Reinstall bleeding screw and tighten as soon as medium exits from fi ller fi tting.
Important: Ventilation of the pump
before start the process,following steps are to relize for ventilate the pump:
check the waterlevel in the tank and refi ll it, if necessary
open the outlet of the pump, or
connect only the outlet of the pump, let the inlet free fl ow out
If there is still some air in the system, you have to repeat the steps as described before.
After open the outlet start the pump for a short time.
Attention
before start the operation of the pump, the function of this pump must be absolutly check.
In case that the pump after a longer standstill and ventilation stopp , you have to introduce a
screwdriver through the airgrille into the shaft and turn it clockwise (1-2 turns min. ), until a easiness is produ-
ced.
Summary of Contents for 45-M
Page 18: ...Operating Instructions 17 FOR YOUR NOTICE...
Page 30: ......
Page 31: ......
Page 32: ...I N S T R U C T I O N M A N U A L C H I L L Y Dok ID V0 01 xx 02 2016...