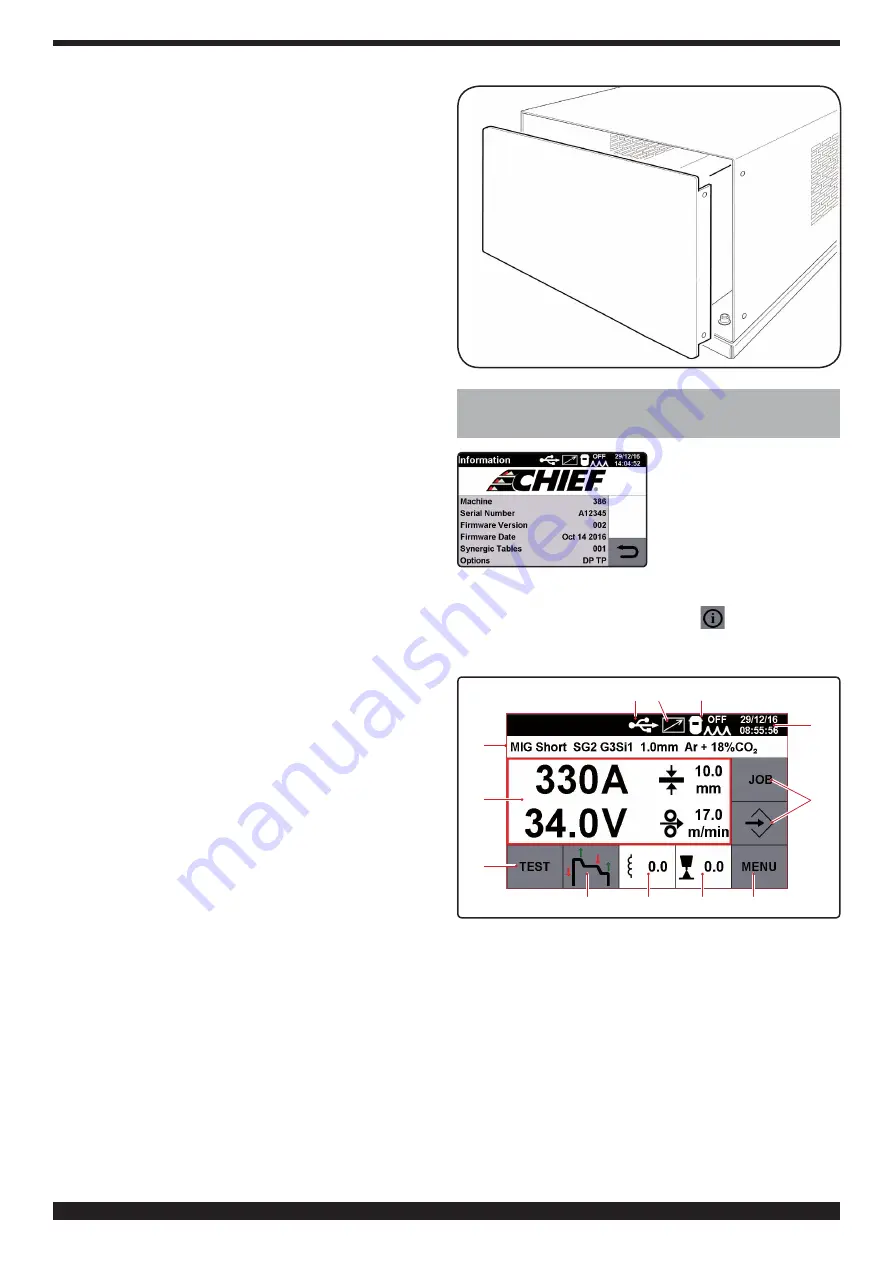
5
• Connect the gas hose to the outlet of the pressure regulator.
• Open the side door.
• Connect the power cord to the socket
4
and through
the clamp to the workpiece.
• Connect the earth lead clamp
4
to the piece to be welded.
• Fit the wire coil on the support inside the compartment.
The coil must be fitted so that the wire unwinds in an
anticlockwise direction.
• Make sure the drive roller is correctly positioned according
to the diameter and type of wire used.
• Cut the welding wire with a well-sharpened tool, keeping
it between your fingers so that it cannot unwind, insert it
inside the pipe exiting from the gear motor and, with the aid
of a finger, insert it inside the steel tube until it comes out of
the adapter.
• Fit the welding torch.
After fitting the reel and torch, switch on the machine, select
the suitable synergic curve, following the instructions given
in the service functions (
PROCESS PARAMS
) paragraph.
Remove the gas nozzle and unscrew the current nozzle
of the torch. Press the torch button until the wire comes
out.
BE CAREFUL to keep your face away from the end
lance while the wire is coming out
, screw up the current
nozzle and fit the gas nozzle.
Open the canister adapter and adjust the gas flow to 8 –
10 l/min.
During welding, the display screen
1
displays the actual
work current and voltage. The displayed values may
be slightly different to those set. This can depend on
numerous different factors - type of torch, thickness
different to nominal thickness, distance between current
nozzle and the material being welded, and the welding
speed.
The current and voltage values, at the end of the welding
operation remain stored on the display
1
where the word
"HOLD is displayed. To display the set values, the handle
2
will have to be moved slightly, while, by pushing the
torch button without welding, the display screen
1
shows
the empty voltage value and a current value of 0.
If, while welding the maximum current and voltage values
are exceeded, said values are not stored on the display
and the written "HOLD" is not displayed.
NOTE
If 0.6mm diameter wires are used the welding torch
sheath should be replaced with one of suitable internal
diameter. If the internal diameter of the sheath is too big it
does not guarantee smooth wire feeding
6 DESCRIPTION OF THE TOUCH SCREEN 1
DISPLAY FUNCTIONS .
When the machine is
switched on, for a few mo-
ments the display shows: the
article number of the ma-
chine, the serial number, the
Firmware version, the date of
the Firmware development
and the release number of the synergic curves table and the
power supply options.
This information is also given in menu
.
6.1 MIG PROCESS. INITIAL DISPLAY.
A
B
C
D
E
F
G
N
O
M L
I
A
The screen displays the welding current in Amperes,
the welding voltage in Volts, the suggested thickness
in mm and the welding wire speed in m/min. During weld-
ing the display shows the current and voltage values in a
continuous manner and, once welding is completed, the
last value in Amperes and Volts is displayed along with
the HOLD word.
When the display is in HOLD, BLUE color appears. If If
we press on the center of the display opens a screen that
displays the main parameters of the last welding: the arc
time in seconds switched on, the main current time in
seconds, the average current in amperes, the average
voltage Volt and the total energy in Kj.
Summary of Contents for MultiMig 721 Multivoltage
Page 45: ...45 WIRING DIAGRAM ...
Page 46: ...46 GENERATORE POWER SOURCE POWER SOURCE ART 386 64 ...
Page 48: ...48 TROLLEY ...
Page 50: ...50 WIRE FEED MOTOR ...
Page 52: ...52 ...