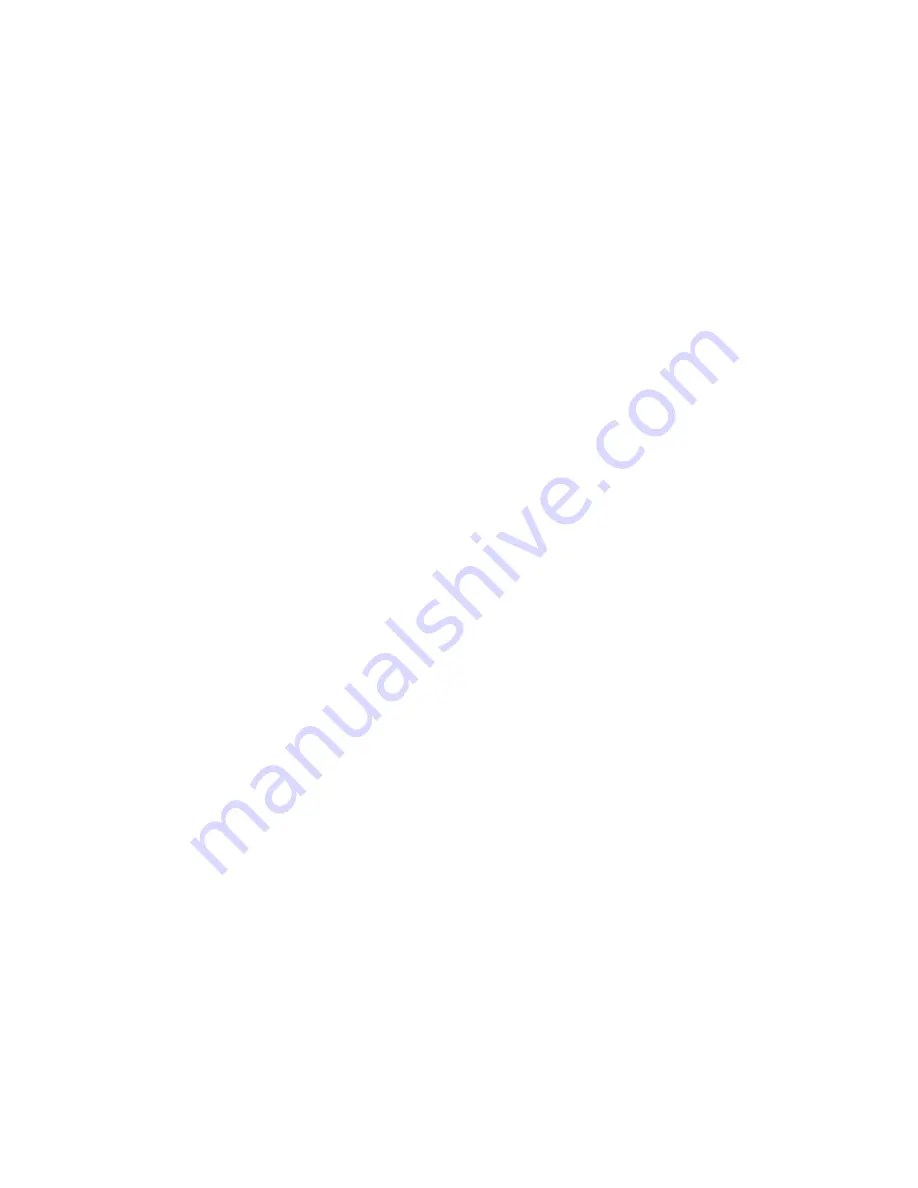
Instruction 2111-801C
01-04
6
LUBRICATION
MOTOR LUBRICATION:
Lubricate the motor according to motor manufacturer's instruction, avoiding over lubrication.
LUBRICATION:
CHICAGO PUMP Dry Pit Pumps are equipped with ball or roller type bearings. The bearings are packed
with grease at the factory and will require additional grease approximately once every fifteen hundred hours
depending on the severity of operation. When adding grease always use a good grade such as those listed
below.
CAUTION-DO NOT OVER-GREASE
A ball bearing requires only a few ounces of grease a year. For most efficient operation bearings should be
filled to fifty percent of their capacity.
Under no circumstances should a bearing be greased until the grease oozes out of the bearing housing.
Excess grease does not in any way lubricate the bearing and acts as a dirt catcher. The grease in an over
greased bearing has a churning action, which tends to over-heat the bearing. In some cases, these
bearings may over-heat to the point where the temper is drawn from the balls rendering them soft and
causing bearing failure. A bearing under normal conditions will require from 1/2 ounce to 1 ounce of grease
each lubrication period.
Lubrication periods will have to be determined by the maintenance man depending upon the severity of the
operation.
CAUTION:
Use only grease which is specified for use with ball bearings. Acids contained in other
lubricants will ruin the bearings.
RECOMMENDED LUBRICANTS
Arco…………………...Litholine E2
Mobil…………………. Mobilux #2
Phillips……………….. Phillips 113 & RB #2
Shell …………………. Alvania EP2
Amoco…………………Super Permalube
Texaco…………………Regal AF132
Union…………………. UNOBAE2
In cases where abnormal conditions exist, such as very high temperatures, it is advisable to consult a
lubrication engineer to determine the proper lubricant to use. If this is not practical, write to CHICAGO
PUMP Company stating your conditions, and we will procure the information for you.
PACKING BOXES, PACKING AND PACKING SEALS:
1. Packing Boxes:
The pumps employ gland adjusted packing boxes for sealing around the shafts. Packing boxes are packed
before shipment. Packing material is replaceable. The packing material recommended for use within the
pump is a combination of Super Seal #3 packing rings (white metal particles, synthetic oil-proof binder,
special long-fiber acrylic with dry-graphite) and Metallic number 101M rings (flexible all metallic packing,
continuous ribbons, soft babbitt foil, spirally wrapped, crinkled, folded and squared to size, layers lubricated
with oil and graphite).
2. Water Seals:
On pumps handling liquids with solids, a water seal used principally to flush the packing and prevent
entrance of solids or grit which would score the shaft or shaft sleeve. It also serves to cool and lubricate
packing, and in the case of suction lift applications it is required as a seal against entrance of air. Non-Clog
pumps are furnished with water seals for external or outside connection to a clear water supply having a
pressure approximately 3 to 10 lbs. (7 ft. to 23 ft. head) greater than the pump discharge pressure. If the
available pressure is too high (20 pounds or more above the operating head of pump) or if gland leakage is
excessive a pressure-reducing valve should be used. If available pressure is below operating head of pump,
or when required, it is often necessary to employ a small water seal pumping unit (see tag attached to water
seal connection). The most economical consumption of sealing water is obtained by installing a solenoid
valve in the water seal line, wired with the pump circuit to open automatically when the pump operates.