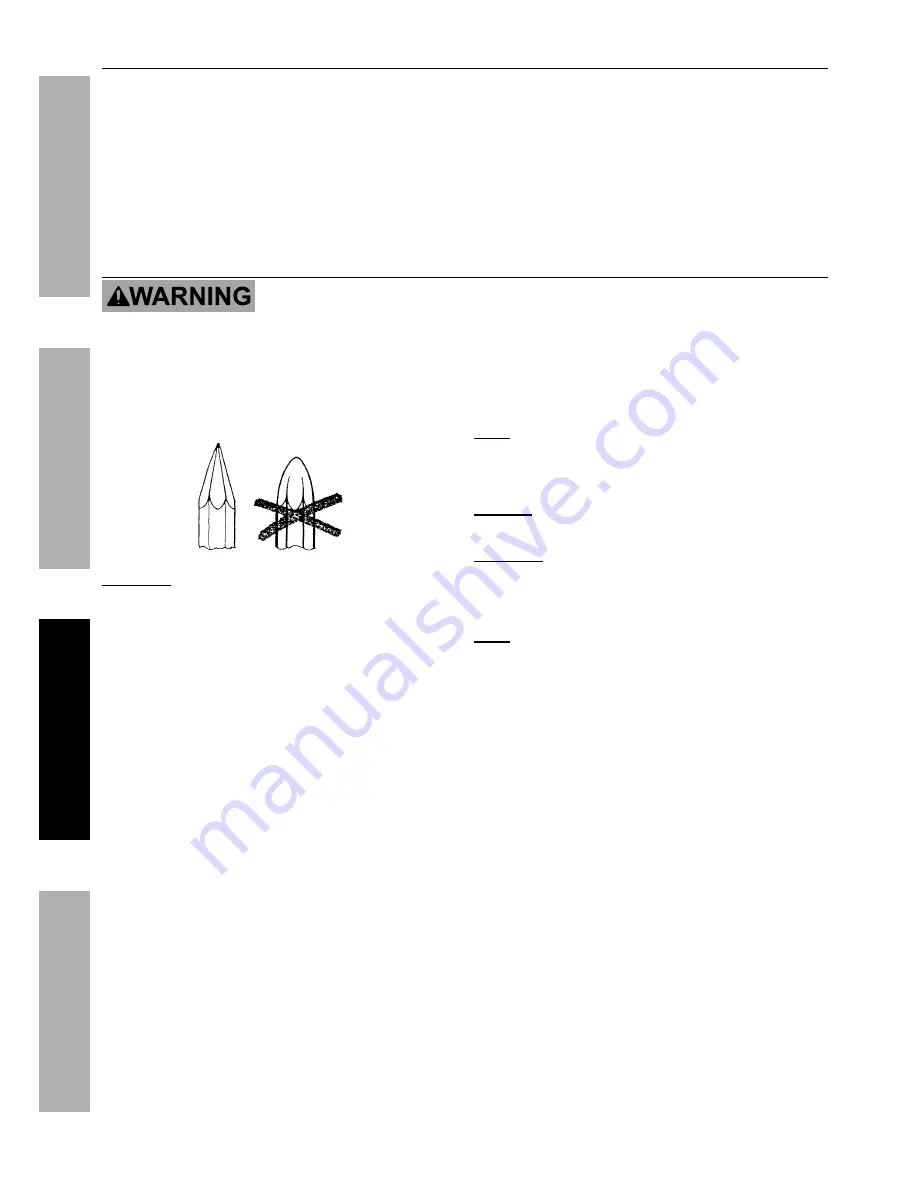
Page 10
For equipment technical questions, please call 1-888-866-5797.
For engine technical questions, please call 1-800-520-0882.
ITEM 61924
SAFETY
SETUP
O
PERA
TION
M
AINTENANCE
Break-in Period:
a. Breaking-in the engine will help to ensure
proper equipment and engine operation.
b. The operational break-in period will last
about 3 hours of use. During this period:
• Do not apply a heavy load to the equipment.
• Do not operate the engine at
its maximum speed.
c. The maintenance break-in period
will last about 20 hours of use.
• Change the engine fuel/oil
mixture after this period.
Under normal operating conditions subsequent
maintenance follows the schedule explained
in the MAINTENANCE section.
General Operating Instructions
TO PREVENT SERIOUS INJURY:
Wear ANSI-approved safety goggles, ear protection, steel-toe boots, and dust mask during use.
Keep feet clear of Breaker Hammer.
Keep children and animals well clear of the work area.
1. Check Chisel for dullness, cracks, or other
damage. Sharpen or replace if necessary.
CAUTION!
Dull tipped chisels can cause unnecessary
chisel movement, resulting in tool wear and
possible injury. Use only sharp tipped chisels.
2. Clearly mark the work area.
3. Start the Engine as detailed in
Starting
the Engine
on page 8.
4. Grip the Handlebar of the
Breaker Hammer with both hands.
5. Set the bit against the work area.
6. Press down on the Throttle.
Note:
Throttle does not lock. Keep pressure
on the Throttle to keep running the tool.
7. Push the tool down to begin striking material.
NOTICE:
Running tool with no load or “empty
blows” will damage the Breaker Hammer.
CAUTION!
Once activated, do not press,
bear down, or thrust forcibly against the work
surface. Allow the Breaker Hammer’s own
weight to supply the needed force.
Note:
If the Breaker Hammer has not been used for
a long time or is being used in low temperatures,
the tool may require 3-5 minutes to warm up.
8. When work is complete, release the
Throttle and shut off the Engine. Refer to
Stopping the Engine
on page 11.
9. Clean, then store the tool indoors
out of children’s reach.