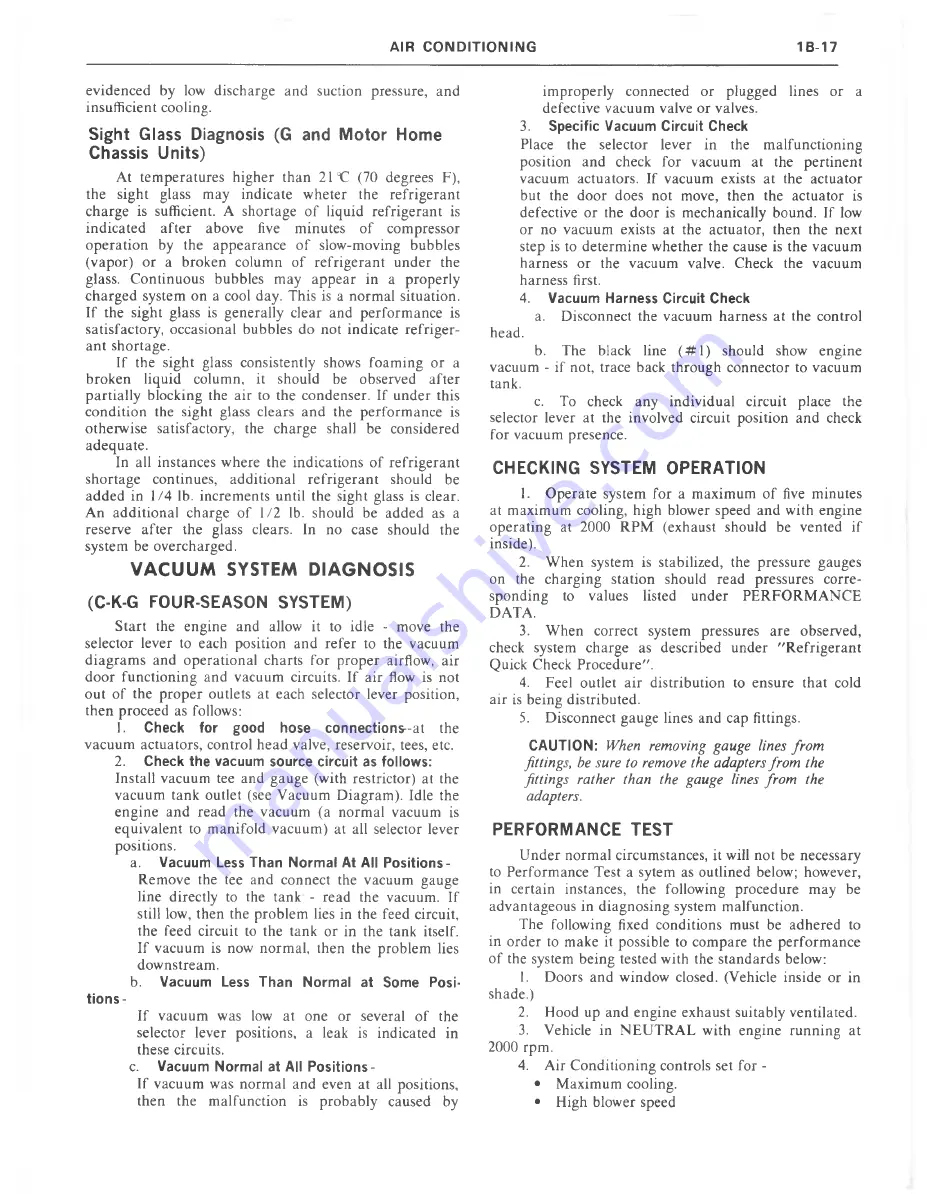
evidenced by low discharge and suction pressure, and
insufficient cooling.
S ight Glass Diagnosis (G and M o to r H om e
Chassis U nits)
At tem peratures higher th an 21 XT (70 degrees F),
the sight glass may indicate w heter the refrig eran t
charge is sufficient. A shortage o f liquid re frig eran t is
in dicated
a fte r above five minutes o f compressor
o p e ra tio n by the app earan ce o f slow-moving bubbles
(vapor) or a broken column o f re frig eran t under the
glass. C ontinuous bubbles m ay a p p e a r in a properly
c h arg ed system on a cool day. This is a n o rm a l situation.
If the sight glass is generally clear and pe rfo rm a n c e is
satisfactory, occasional bubbles do not indicate re frig e r
an t shortage.
If the sight glass consistently shows fo am in g o r a
broken liquid column, it should be observed after
p artially blocking the air to the condenser. If und er this
condition the sight glass clears an d the p erfo rm an ce is
otherwise satisfactory, the charge shall be considered
adequate.
In all instances w here the indications o f re frig e ran t
shortage continues, additional r e frig e ran t should be
a d d ed in 1/4 lb. increments until the sight glass is clear.
A n additional charge o f 1/2 lb. should be added as a
reserve a fte r the glass clears. In no case should the
system be overcharged.
VACUUM SYSTEM DIAGNOSIS
(C-K-G FOUR-SEASON S YS TE M )
Start the engine and allow it to idle - move the
selector lever to each position and refer to the vacuum
d ia g ra m s and operational charts for pro p er airflow, air
d oor functioning and vacuum circuits. If air flow is not
out o f the p ro p e r outlets at each selector lever position,
then proceed as follows:
1.
Check
fo r
good
hose
co n n ectio n s-at
the
vacuum actuators, control h e a d valve, reservoir, tees, etc.
2.
Check the vacuum source circuit as follows:
Install vacuum tee and gauge (with restrictor) at the
vacuum tank outlet (see V acuum D iagram ). Idle the
en g in e and read the vacuum (a norm al vacuum is
equivalent to m anifold vacuum ) at all selector lever
positions.
a.
Vacuum Less Than N orm al At All P osition s-
Remove the tee and connect the vacuum gauge
line directly to the tank - read the vacuum. If
still low, then the problem lies in the feed circuit,
the feed circuit to the tank or in the tank itself.
If vacuum is now norm al, then the problem lies
downstream.
b.
Vacuum Less T han N orm al at Some Posi
tio n s -
If vacuum was low at one or several o f the
selector lever positions, a leak is indicated in
these circuits.
c.
Vacuum N orm al at Alt P o sition s-
If vacuum was n o rm al and even at all positions,
then the m alfunction is pro b ab ly caused by
im properly connected or plugged lines or a
defective vacuum valve or valves.
3.
Specific Vacuum Circuit Check
Place the selector lever in the m alfunctioning
position and check for vacuum at the p ertinent
vacuum actuators. If vacuum exists at the actuator
but the d oor does not move, then the actuator is
defective or the door is mechanically bound. If low
or no vacuum exists at the actuator, then the next
step is to d eterm ine w hether the cause is the vacuum
harness o r the vacuum valve. Check the vacuum
harness first.
4.
Vacuum Harness Circuit Check
a.
Disconnect the vacuum harness at the control
head.
b.
The black line ( # 1 ) should show engine
vacuum - if not, trace back through connector to vacuum
tank.
c.
To check any individual circuit place the
selector lever at the involved circuit position and check
for vacuum presence.
C H EC K IN G SYSTEM O P E R A T IO N
1.
O perate system for a m axim um o f five minutes
at m axim um cooling, high blower speed and with engine
operating at 2000 R P M (exhaust should be vented if
inside).
2.
W hen system is stabilized, the pressure gauges
on the charging station should read pressures corre
sponding to values listed und er P E R F O R M A N C E
DATA.
3.
W h e n correct system pressures are observed,
check system charge as described under " R e frig e ra n t
Quick Check Procedure".
4.
Feel outlet air distribution to ensure th at cold
air is being distributed.
5.
Disconnect gauge lines and cap fittings.
C A U T IO N :
When removing gauge lines fr o m
fittings, be sure to remove the adapters fr o m the
fittin g s rather than the gauge lines fr o m the
adapters.
PER FO R M A N C E TEST
U n d e r norm al circumstances, it will not be necessary
to Perform ance Test a sytem as outlined below; however,
in certain instances, the following procedure m ay be
advantageous in diagnosing system malfunction.
The following fixed conditions must be adhered to
in o rder to make it possible to com pare the pe rfo rm a n c e
o f the system being tested with the standards below:
1.
Doors and window closed. (Vehicle inside or in
shade.)
2.
Hood up and engine exhaust suitably ventilated.
3.
Vehicle in N E U T R A L with engine run n in g at
2000 rpm.
4.
Air C o nditioning controls set for -
•
M axim um cooling.
•
High blower speed
Summary of Contents for 1977 light duty truck
Page 1: ......
Page 28: ......
Page 70: ...Fig IB 24 Four Season System Vacuum Diagram C K Models 1B 24 LIGHT TRUCK SERVICE M A N U A L...
Page 71: ...Fig lB 25 Overhead System Wiring Diagram C K Models AIR C O N D ITIO N IN G 1 B 2 5...
Page 72: ...Fig IB 26 C60 System Wiring Diagram G Models...
Page 74: ......
Page 75: ...Fig lB 29 Motor Home Chassis Wiring Diagram THERMOSTATIC SWITCH AIR C O N D ITIO N IN G IB 2 9...
Page 106: ......
Page 128: ......
Page 129: ...Fig 2D 5 Typical 05 and 0 6 Vans...
Page 136: ......
Page 148: ...Fig 2D 51 Rear Door Controls...
Page 158: ...Fig 2D 79 Folding Top Assembly...
Page 159: ...Fig 2D 80 Folding Top Side Moldings and Header...
Page 161: ...Fig 2D 85 Dnver s Bucket Seat 14 Fig 2D 86 Passenger s Bucket Seat 14...
Page 162: ...Fig 2D 89 Rear Folding Seat 06 Fig 2D 9 0 Rear Bench Seat 14...
Page 163: ......
Page 164: ......
Page 165: ......
Page 185: ......
Page 186: ......
Page 190: ......
Page 225: ......
Page 226: ......
Page 248: ...Fig 3B 77 Removing Bearing Housing Pivot Pins Fig 3B 79 Replacing Lock Bolt Spring...
Page 278: ...C 10 G 10 20 C 20 30 G 30 P 10 30 9 Fig 3C l Front Suspension C P Series...
Page 284: ...BALL JOINT DIAGNOSTIC PROCEDURE...
Page 316: ......
Page 321: ...Fig 3D 12 Rear Spring Installation G Models...
Page 322: ......
Page 325: ......
Page 326: ......
Page 336: ......
Page 352: ......
Page 378: ......
Page 395: ...Fig 5 2 Front Brake Pipes and Hoses C K Models...
Page 396: ......
Page 397: ...Fig 5 4 Front Brake Pipes and Hoses P Models BRAKES 5 1 3...
Page 400: ......
Page 401: ...V 8 N 4 0 L 6 N 4 0...
Page 402: ......
Page 404: ......
Page 405: ...P300 42 M40 JB9...
Page 438: ......
Page 448: ...Fig 6A 4 P Series Engine Rear Mount...
Page 451: ...Fig 6A 8 K Series Engine Rear Mount...
Page 452: ...ENGINE M O U N T BRACKET ALL K SERIES W ITH L 6 ENGINE 6A14 LIGHT TRUCK SERVICE M A N U A L...
Page 483: ...FUEL PUMP PUSH ROD OILING OIL F LTER AND BY PASS VALVE...
Page 484: ...FUEL PUMP PUSH ROD OILING CRANKCASE AND CRANKSHAFT OILING VALVE MECHANISM OILING...
Page 487: ......
Page 488: ...MOUNT VIEW A V AUTOMATIC TRANSMISSION FRONT MANUAL TRANSMISSION...
Page 489: ......
Page 490: ......
Page 568: ......
Page 602: ......
Page 605: ......
Page 612: ...Fig 6D 3i High Energy Ignition Basic W iring...
Page 644: ......
Page 648: ...DISTRIBUTOR VALVE Fig 6E 3 Vacuum Hose Schematic L6 292 CID Calif HD Emissions...
Page 649: ...V A LV E Fig 6E 5 Vacuum Hose Schematic V8 305 CID HD Emissions...
Page 650: ...Fig 6E 7 Vacuum Hose Schematic V8 350 CID High Altitude Calif LD Emissions...
Page 651: ...VALVE Fig 6E 9 Vacuum Hose Schematic V8 350 400 CID Except Calif HD Emissions...
Page 652: ...CANISTER...
Page 653: ...PCV V AL VE Fig 6E 13 Vacuum Hose Schematic V8 454 CID Except Calif HD Emissions...
Page 672: ...Fig 6E 29 Air Cleaner 305 350 400 V8 CK...
Page 682: ......
Page 692: ......
Page 700: ...Fig 7A 6B Detent Downshift Cable C K and P Series...
Page 709: ...Fig 7 A 12B CBC 350 Hydraulic Circuit A U TO M A T IC T R A N S M IS S IO N 7 A 1 7...
Page 743: ...VIEW B FLAT IvEwfDl l6 G tO 2 GAGE...
Page 744: ......
Page 755: ...V I E W B WITH AUTOMATIC TRANSMISSION WITH MANUAL TRANSMISSION V I E W A...
Page 760: ...r...
Page 766: ......
Page 767: ...V I E W D 1 6 ENGINE VIEW V 8 ENGINE...
Page 768: ......
Page 775: ......
Page 788: ......
Page 794: ...G A S G A U G E...
Page 805: ......
Page 836: ...Fig 8 58 Seat Belt Reminder System Schematic...
Page 844: ...C H E C K n...
Page 852: ......
Page 853: ...SPECIAL TOOLS J 2 3 5 2 0...