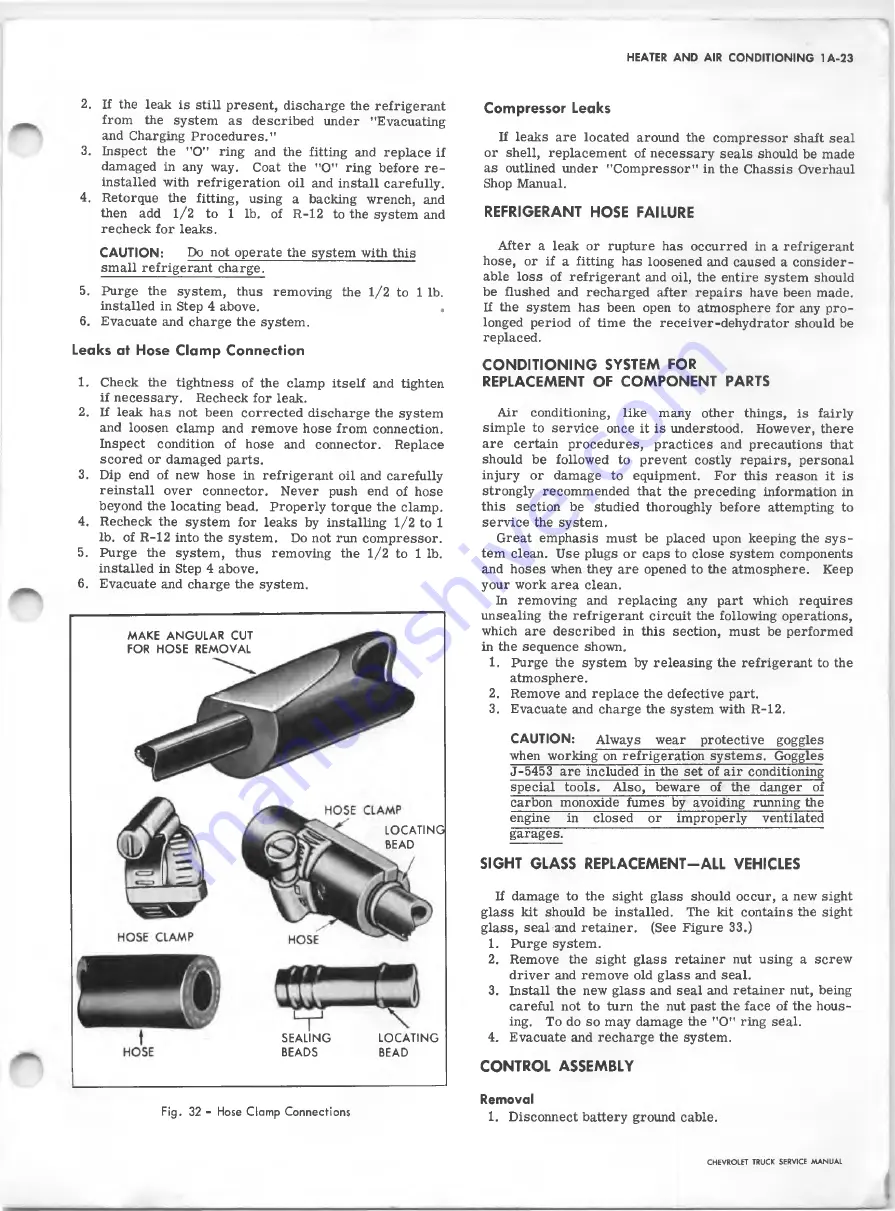
HEATER AND AIR CONDITIONING 1A-23
2.
3.
4.
If the leak is still present, discharge the refrigerant
from the system as described under "Evacuating
and Charging Procedures."
Inspect the "O" ring and the fitting and replace if
damaged in any way. Coat the "O" ring before r e
installed with refrigeration oil and install carefully.
Retorque the fitting, using a backing wrench, and
then add 1/2 to 1 lb. of R-12 to the system and
recheck for leaks.
CAUTION:
Do not operate the system with this
small refrigerant charge.
5. Purge the system, thus removing the 1/2 to 1 lb.
installed in Step 4 above.
,
6
. Evacuate and charge the system.
Leaks at Hose Clamp Connection
1. Check the tightness of the clamp itself and tighten
if necessary. Recheck for leak.
2. If leak has not been corrected discharge the system
and loosen clamp and remove hose from connection.
Inspect condition of hose and connector. Replace
scored or damaged parts.
3. Dip end of new hose in refrigerant oil and carefully
reinstall over connector. Never push end of hose
beyond the locating bead. Properly torque the clamp.
4. Recheck the system for leaks by installing 1/2 to 1
lb. of R-12 into the system. Do not run compressor.
5. Purge the system, thus removing the 1/2 to 1 lb.
installed in Step 4 above.
6
. Evacuate and charge the system.
MAKE A N G U LA R CUT
FOR H O SE REM OVAL
LOCATING
BEAD
SEA LIN G
BEADS
LOCATING
BEAD
Compressor Leaks
If leaks are located around the compressor shaft seal
or shell, replacement of necessary seals should be made
as outlined under "Compressor" in the Chassis Overhaul
Shop Manual.
REFRIGERANT HOSE FAILURE
After a leak or rupture has occurred in a refrigerant
hose, or if a fitting has loosened and caused a consider
able loss of refrigerant and oil, the entire system should
be flushed and recharged after repairs have been made.
If the system has been open to atmosphere for any pro
longed period of time the receiver-dehydrator should be
replaced.
CONDITIONING SYSTEM FOR
REPLACEMENT OF COMPONENT PARTS
Air conditioning, like many other things, is fairly
simple to service once it is understood. However, there
are certain procedures, practices and precautions that
should be followed to prevent costly repairs, personal
injury or damage to equipment. For this reason it is
strongly recommended that the preceding information in
this section be studied thoroughly before attempting to
service the system.
Great emphasis must be placed upon keeping the sy s
tem clean. Use plugs or caps to close system components
and hoses when they are opened to the atmosphere. Keep
your work area clean.
In removing and replacing any part which requires
unsealing the refrigerant circuit the following operations,
which are described in this section, must be performed
in the sequence shown.
1. Purge the system by releasing the refrigerant to the
atmosphere.
2. Remove and replace the defective part.
3. Evacuate and charge the system with R-12.
CAUTION:
Always wear protective goggles
when working on refrigeration systems. Gogglei
J-5453 are included in the set of air conditioning
special tools. Also, beware of the danger of
carbon monoxide fumes by avoiding running the
engine
in closed or improperly ventilated
garages.
F ig . 32 - Hose Clamp Connections
SIGHT GLASS REPLACEMENT-ALL VEHICLES
If damage to the sight glass should occur, a new sight
glass kit should be installed. The kit contains the sight
glass, seal and retainer. (See Figure 33.)
1. Purge system.
2. Remove the sight glass retainer nut using a screw
driver and remove old glass and seal.
3. Install the new glass and seal and retainer nut, being
careful not to turn the nut past the face of the hous
ing. To do so may damage the "O" ring seal.
4. Evacuate and recharge the system.
CONTROL ASSEMBLY
Removal
1. Disconnect battery ground cable.
CHEVROLET TRUCK SERVICE M ANUAL
Summary of Contents for 10 Series 1967
Page 1: ...CHASSIS V3 a n s W U gw...
Page 2: ......
Page 28: ......
Page 80: ...BODY IB 18 Fig 41 Exploded View of Level Ride Seat CHEVROLET TRUCK SERVICE MANUAL...
Page 89: ...BODY IB 27 CHEVROLET TRUCK SERVICE MANUAL...
Page 105: ...BODY IB 43 Fig 94 Check Link Assembly Typical CHEVROLET TRUCK SERVICE MANUAL...
Page 117: ...BODY IB 55 Fig 116 A uxiliary Seat CHEVROLET TRUCK SERVICE MANUAL...
Page 121: ...Fig 4 1 0 3 0 Series Truck Frame...
Page 122: ...Fig 5 4 0 6 0 Single A xle Truck Frames Exc T ilt Cab FRAME 2 4...
Page 124: ...CHEVROLET TRUCK SERVICE MANUAL 1 Ficu 7 4 0 6 0 Series T ilt Cab Truck Frames FRAME 2 6...
Page 228: ...BRAKES 5 12 TD 50 60 Fig 23 Parking Brake Cables T Models CHEVROLET TRUCK SERVICE MANUAL...
Page 280: ......
Page 324: ...I I...
Page 336: ...ENGINE FUEL 6M 12 CHEVROLET TRUCK SERVICE MANUAL...
Page 342: ......
Page 348: ......
Page 386: ......
Page 393: ...CHEVROLET TRUCK SERVICE MANUAL CLUTCHES AND TRANSMISSIONS 7 7...
Page 472: ...STEERING 9 18 Fig 31 Typical Power Steering Hose Routing CHEVROLET TRUCK SERVICE MANUAL...
Page 474: ...w j...
Page 486: ......
Page 500: ...1...
Page 502: ...l c t r iC al 12 2...
Page 568: ......
Page 576: ......
Page 580: ...1...
Page 587: ...SPECIFICATIONS 7 ENGINE SECTION 6 8 25 1 on CE TE400 Series CHEVROLET TRUCK SERVICE MANUAL...
Page 590: ...SPECIFICATIONS 10 ENGINE TORQUES CHEVROLET TRUCK SERVICE MANUAL...